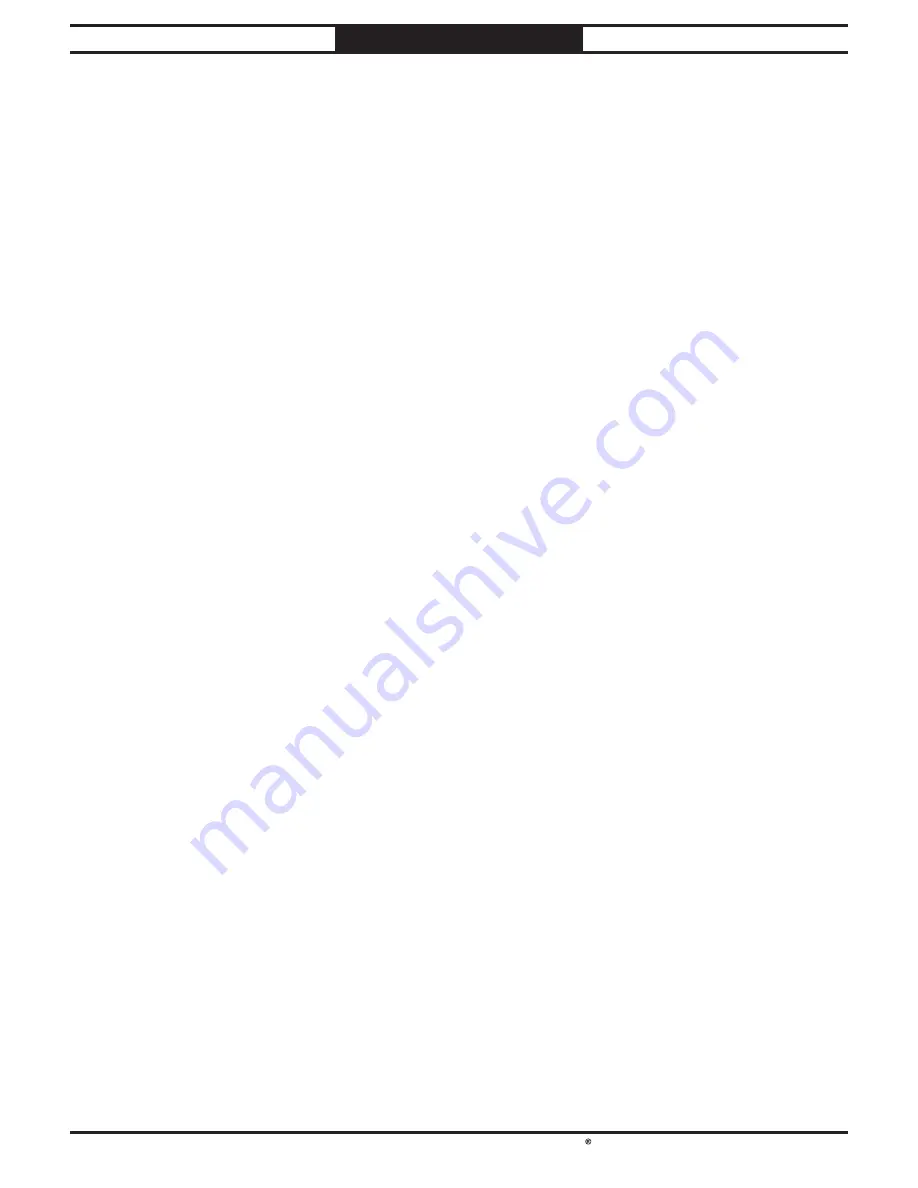
-30-
For Machines Mfd. Since 10/21
South Bend Tools
Model SB1118
O P E R A T I O N
Pitch & Glue Build-up
Problem:
Glue and resin buildup on the rollers
and cutterhead will cause overheating by
decreasing cutting sharpness while increasing
drag in the feed mechanism. The result can
include scorched lumber, uneven knife/insert
marks, and chatter.
Solution:
Clean the rollers and cutterhead.
Chip Marks or Indentations
Problem:
Chip indentation or chip bruising is
the result of wood chips not being thrown away
from the cutterhead and out of the machine.
Instead they are carried around the cutterhead,
deposited on the planed surface and crushed by
the outfeed roller. Some of the causes of chip
indentation are:
• Wood chips/sawdust not being properly
expelled from the cutterhead.
• The type of lumber being planed. Certain
species have a tendency to chip bruise.
• Dull knives/inserts.
• Excessive depth of cut.
Solution:
• Use a proper dust-collection system; adjust
chip defl ector in or out as necessary.
• Lumber must be completely dry, preferably
kiln-dried (KD). Air-dried (AD) lumber must
be seasoned properly and have no surface
moisture. DO NOT surface partially-air-dried
(PAD) lumber.
• Make sure planer knives/inserts are sharp.
• Reduce depth of cut.
Rippled Cut
Problem:
Regularly spaced indentations across
face of workpiece are caused by excessive outfeed
roller pressure or excessive feed rate.
Solution:
Reduce outfeed roller pressure; reduce
feed rate.
Snipe
Problem:
Occurs when board ends have more
material removed than the rest of the board.
Usually caused when the workpiece is not
properly supported as it goes through the
machine. In many cases, however, a small
amount of snipe is inevitable and cannot be
completely prevented.
Solution:
Hold workpiece up slightly as it leaves
the outfeed end of the planer. The best way to
deal with snipe is by planing lumber longer than
your intended work length and then cutting off
the excess after planing is completed.
Rippled Cut
Problem:
Regularly spaced indentations across
face of workpiece are caused by excessive outfeed
roller pressure or excessive feed rate.
Solution:
Reduce outfeed roller pressure; reduce
feed rate.