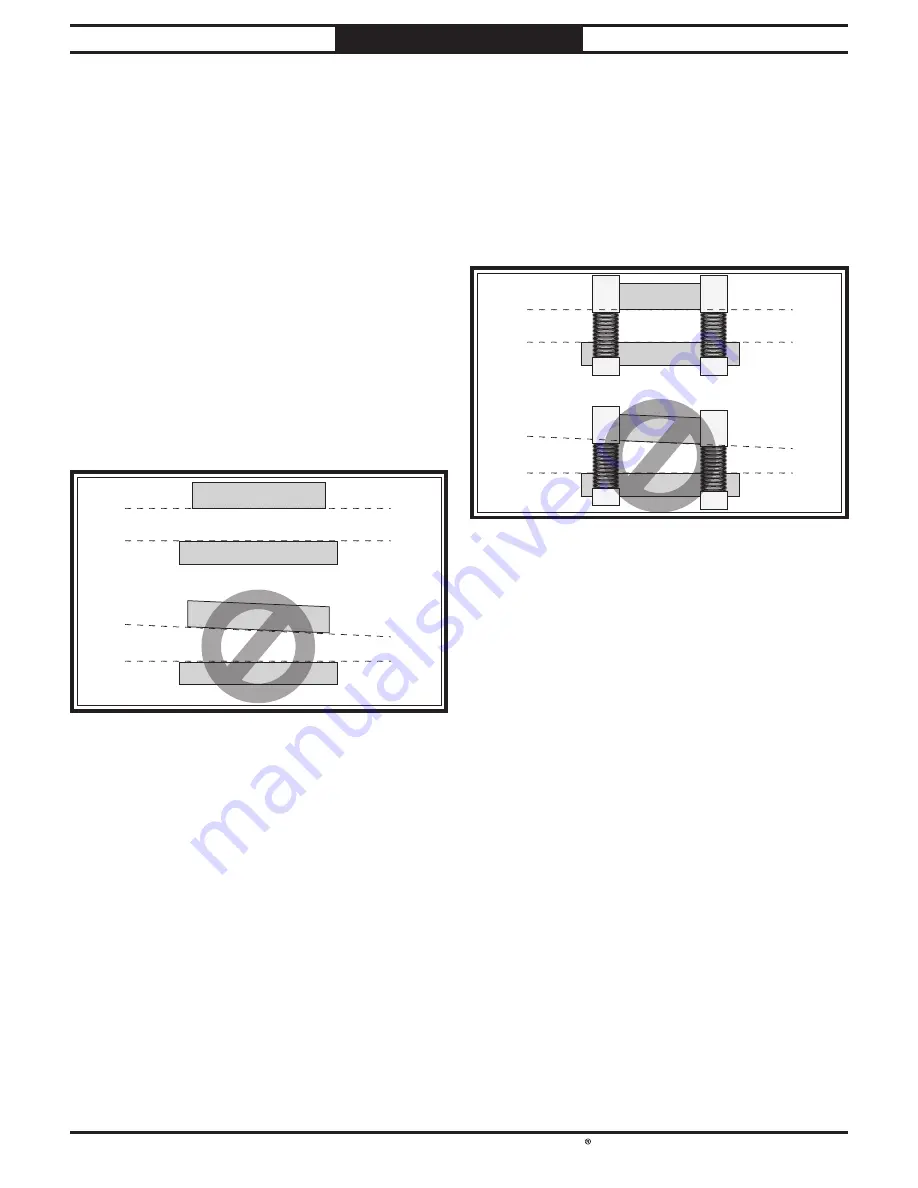
South Bend Tools
For Machines Mfd. Since 12/20
Model SB1108/SB1109
-45-
S E R V I C E
Adjusting Table
Parallelism
Maximum Allowable Tolerances
Cutterhead/Table Side-to-Side .....................0.002"
Head Casting/Table Front/Back ...................0.020"
Tools Needed
Qty
Rotacator ...............................................................1
Phillips Screwdriver #2 ........................................1
Wrench or Socket 14mm .......................................1
Hex Wrench 6mm .................................................1
Figure 64. Side-to-side parallelism of table and
cutterhead.
Cutterhead
Cutterhead
Table
Table
Parallel
Parallel
Not Parallel
Not Parallel
FRONT
VIEW
SIDE-TO-SIDE
How the table sits in relation to the head casting
from front-to-back is also important. Because the
feed rollers, pressure bar, and chip breaker are
adjusted off the table position, the tolerances on
the front-to-back positioning are not as critical
as the cutterhead/table side-to-side positioning.
Therefore, the maximum allowable tolerance for
the front-to-back parallelism is within 0.020" (see
Figure 65).
Figure 65. Front-to-back parallelism of table and
cutterhead.
Table
Table
Head
Head
Parallel
Parallel
Not Parallel
Not Parallel
FRONT
BACK
Table parallelism is critical to the operation of
the machine. As such, it is essential that the
table is adjusted parallel with the cutterhead
(within 0.002") from side-to-side, as illustrated in
Figure 64.
Table Parallelism Inspection
The easiest way to determine if your head
casting has a parallelism problem is to plane a
workpiece and measure the thickness in multiple
locations. If the workpiece is tapered from left-to-
right or from front-to-back, then parallelism may
be a problem.
Use your Rotacator to further inspect the table
parallelism. If you do not have a Rotacator, a
wood block and feeler gauges may be used, but
extra care must be taken to ensure accuracy. If
the table is not within the maximum allowable
tolerances, it must be adjusted.