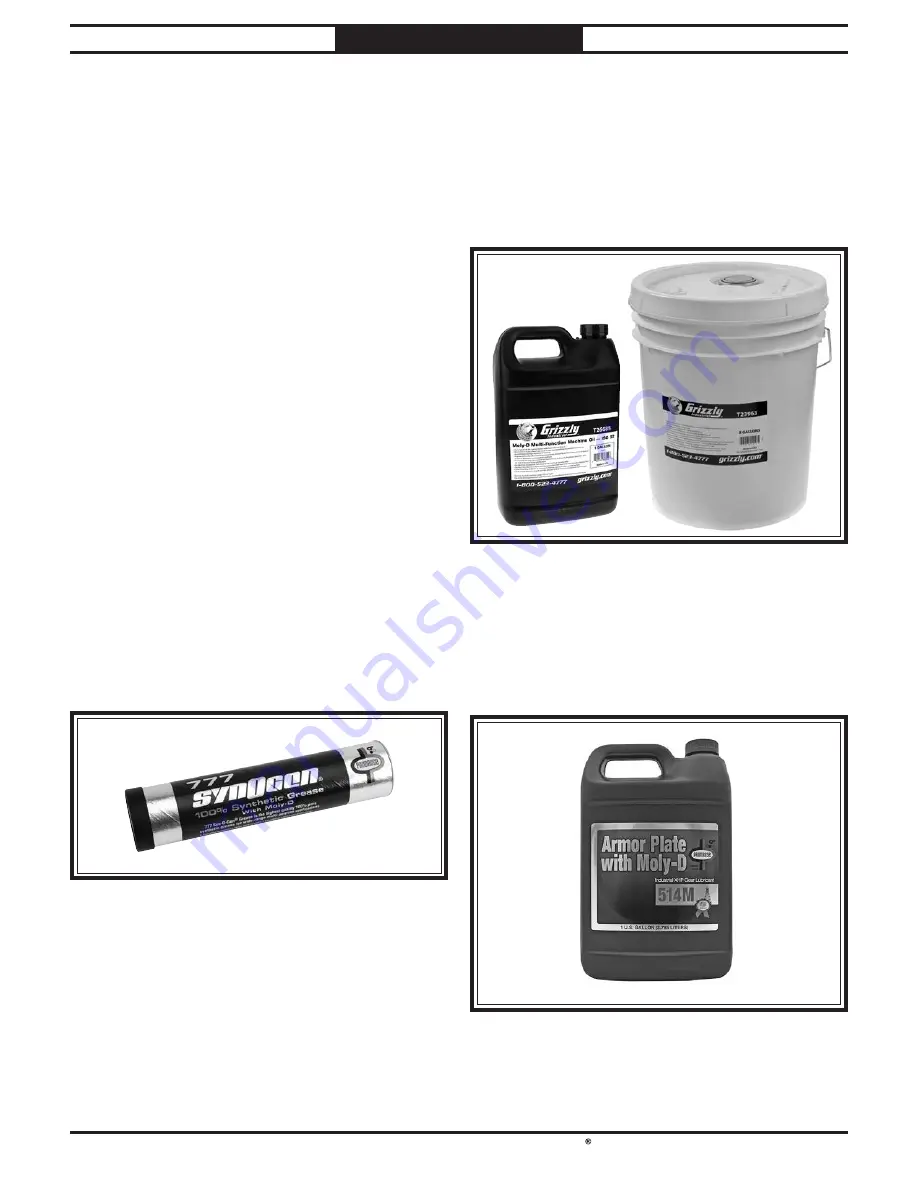
-38-
For Machines Mfd. Since 02/21
South Bend Tools
Model SB1097
M A I N T E N A N C E
Lubrication
An essential part of lubrication is cleaning the
components before lubricating them. This step
is critical because dust builds up on lubricated
components, which makes them hard to move.
Simply adding more grease to built-up grime will
not result in smooth moving parts. Clean the
components in this section with an oil/ grease
solvent cleaner or mineral spirits before applying
lubrication.
All the bearings are sealed and permanently
lubricated. Leave them alone until they need to
be replaced.
The following are the main components that
need to be lubricated:
• Rack & Pinion Gear
• Oil Ports & Grease Fittings
• Gearbox
T26419—Syn-O-Gen Synthetic Grease
Formulated with 100% pure synthesized
hydrocarbon basestocks that are compounded
with special thickeners and additives to
make Syn-O-Gen non-melt, tacky, and water-
resistant. Extremely low pour point, extremely
high temperature oxidation, and thermal
stability produce a grease that is unmatched in
performance.
Figure
Figure 70. T26419 Syn-O-Gen Synthetic Grease.
. T26419 Syn-O-Gen Synthetic Grease.
Figure 72. Model T28042 ISO 320 Gear Oil.
Model T28042 ISO 320 Gear Oil.
T28042—Primrose Moly-D ISO 320 Gear Oil
Armor Plate with Moly-D Industrial XHP 514M
is an industrial gear oil from Primrose that has
been developed specifically for the significantly
higher temperatures and pressures typical of
modern industrial applications. 1 gallon size.
Figure 71. ISO 32 Multi-Function Machine Oil.
ISO 32 Multi-Function Machine Oil.
T26685—ISO 32 Moly-D Way Oil, 1 Gal.
T23963—ISO 32 Moly-D Way Oil, 5 Gal.
Moly-D oils are some of the best we have found
for maintaining the critical components of
machinery because they tend to resist run-off
and maintain their lubricity under a variety of
conditions—as well as reduce chatter or slip. Buy
in bulk and save with 5-gallon quantities.