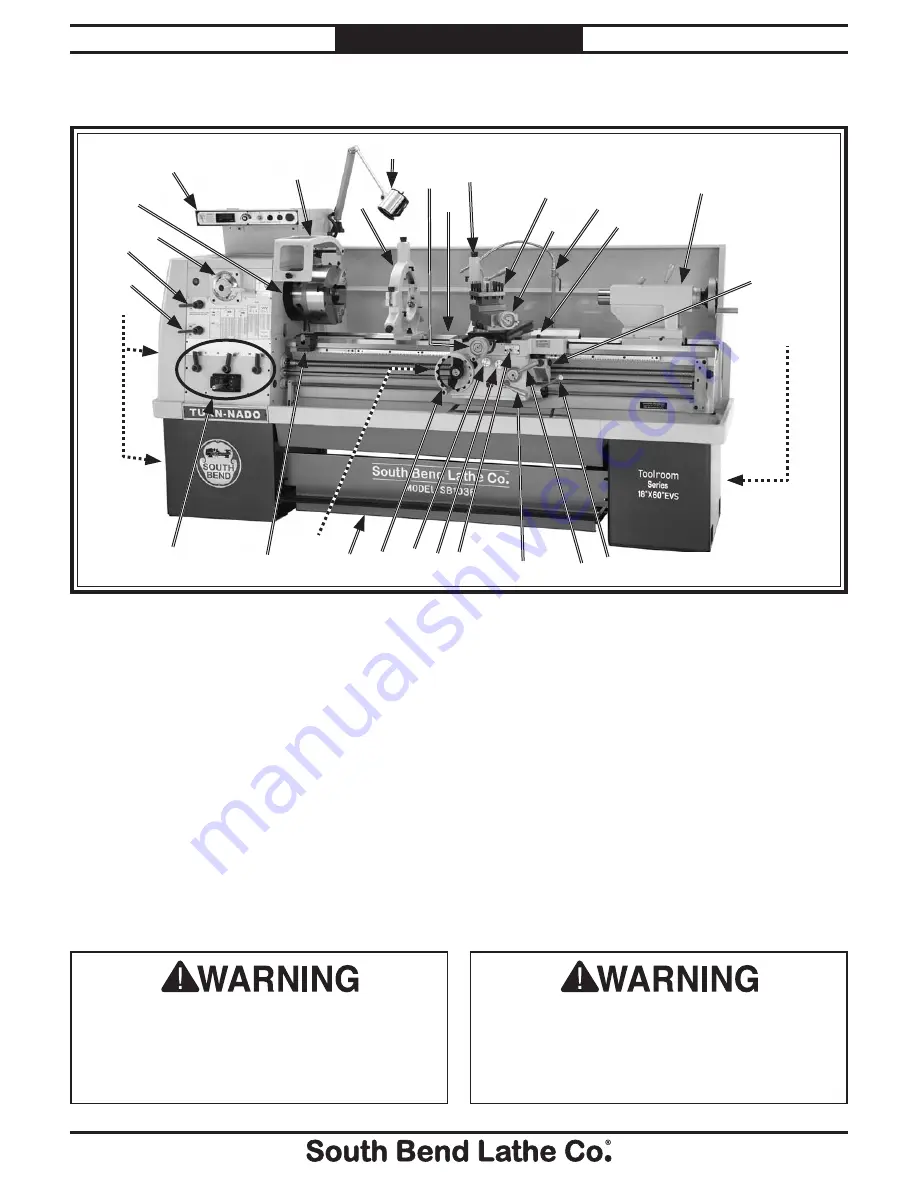
-4-
For Machines Mfg. Since 7/09
Model SB1016/SB1036
I N T R O D U C T I O N
Identification
Serious personal injury could occur if
you connect the machine to power before
completing the setup process. DO NOT
connect power until instructed to do so later
in this manual.
Untrained users have an increased risk
of seriously injuring themselves with this
machine. Do not operate this machine until
you have understood this entire manual and
received proper training.
P.
Half Nut Lever
Q.
Feed ON/OFF Lever
R.
Way Oil Pump
S.
Apron Feed Direction Knob
T.
Feed Selection Knob
U.
Carriage Handwheel w/Safety Position
V.
Brake
Pedal
W.
Adjustable Feed Clutch Knob
X.
Micrometer Stop
Y.
Quick Change Gearbox Levers
Z.
Headstock Oil Pump & Reservoir Access
AA.
Headstock Feed Direction Lever
AB.
Quick Change Range Lever
AC.
Spindle Speed and Range Lever
AD.
D1-8 Camlock MT#7 Spindle
A.
Control
Panel
B.
Chuck Guard w/Safety Switch
C.
Steady Rest w/Ball Bearing Fingers
D.
Halogen Work Lamp
E.
Cross Slide Handwheel
F.
Three-Vee Bed and Way System
G.
Follow Rest w/Brass Fingers
H.
4-Way Tool Post
I.
Compound Rest Handwheel
J.
Cutting Fluid Nozzle
K.
Carriage Lock
L.
Double-Clamping
Tailstock
M.
Thread Dial for Cutting Inch Threads
N.
Cutting Fluid Pump/Tank
O.
Spindle ON/OFF Lever
Figure 1. The 18" x 60" Variable Speed Toolroom Lathe (EVS).
A
B
C
D
E
F
H
L
K
M
O
Y
V
X
Z
Q
P
N
R
W
T
U
S
I
J
G
AB
AA
AC
AD