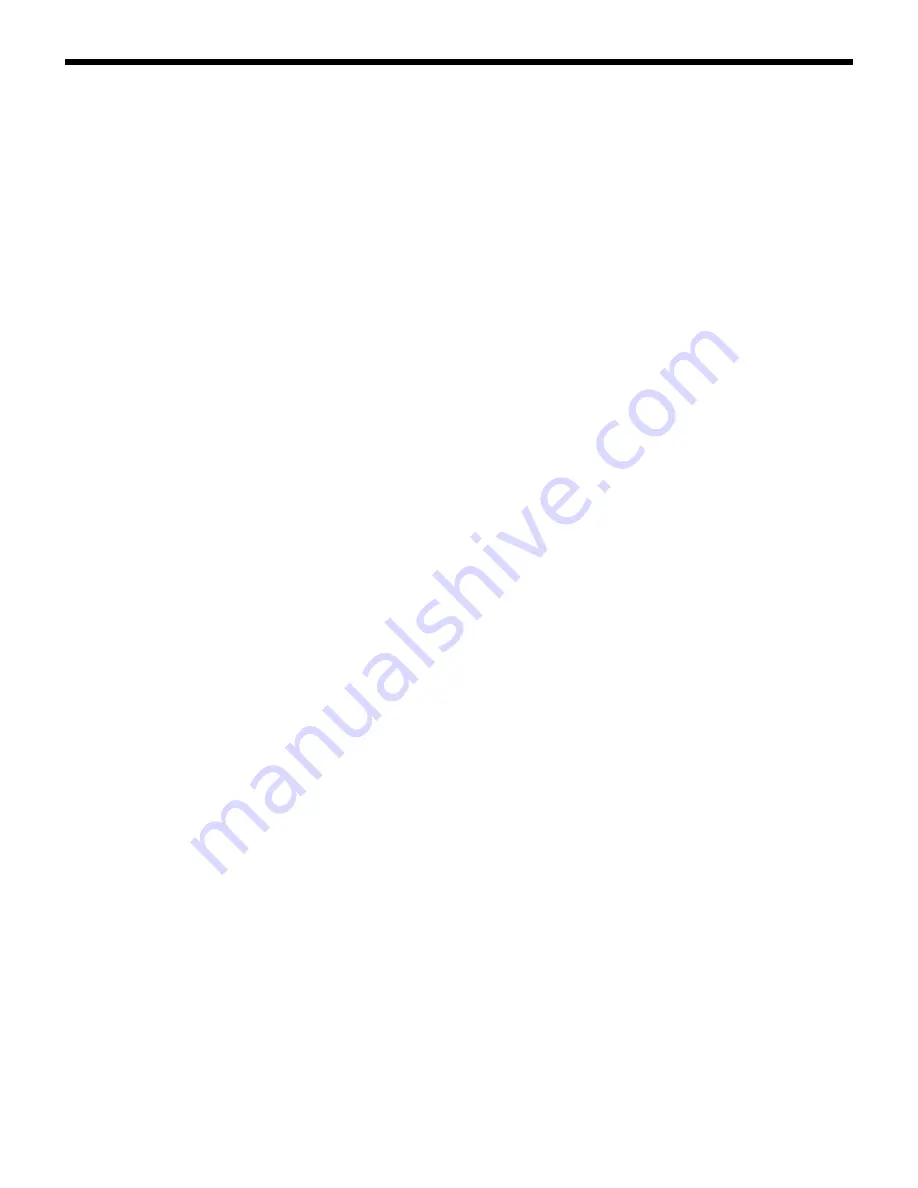
TC6
®
System Descriptions
3-5
c. Control Features
The MC33035's circuitry contains all except one major element for
closed-loop speed control. The missing element is that which
monitors motor rpm (speed) and generates a signal proportional to
motor speed, a function that has been the domain of a tachometer
Once provided with a motor speed signal, the MC33035's high
performance error amplifier and its internal oscillator form the last
major links in the speed control loop.
The MC33035's on-board oscillator operates at a frequency set by an
external resistance/capacitance (R-C). Each cycle capacitor is charged
from the reference output through a resistor and then rapidly
discharged through an internal transistor.
At each positive or negative transition of the Hall-effect sensors,
the MC33039 generates a pulse with a fixed on time. The output
signal can then be filtered to obtain a voltage proportional to motor
speed. Design of an MC33035/39 based system should begin with
setting the system timing, which originates in the MC33039. Selection
of timing components for MC33039 is based on the desired maximum
motor rpm. For the motor used in this application, there are two
electrical degrees for every mechanical degree since the permanent
magnet on the rotor has two pairs of poles. Therefore, for every
mechanical revolution each Hall-effect sensor delivers two pulses
and the three sensors generate six pulses. The MC33039 generates
12 pulses for each revolution, one for each rising and falling edge.
For a given maximum rotor speed, the output pulse width has a
maximum limit. For example, the maximum speed is 6000␣rpm,
which is 100␣r evolutions per second, the MC33039 will generate
100␣x␣12, or 1200␣pulses per second. The >1kHz␣fr equency deter-
mines that the maximum pulse width must be less than 1␣ms. One
can determine that R1 and C1 values of 30␣k and 22␣nF r esults in a
pulse width of 600␣
µ
s. To set the system PWM frequency, refer to the
MC33035's data sheet. There it shows that setting R2 and Cw to
5.1␣k and 0.01␣
µ
F gives a nominal PWM frequency of 24␣kHz, just
above the audible range.
Both inputs and the outputs of the MC33035's error amplifier are
accessible to accommodate various control methods. For open-loop
control a reference signal proportional to the desired speed can be
fed into the error amplifier's non-inverting input. The error ampli-
fier output is then configured as a unity gain voltage follower by
connecting its inverting input to its output. The error amplifier's
output is then compared to the output of the oscillator to obtain a
PWM signal proportional to the desired motor speed--unless the
control loop is overridden by an overcurrent or fault condition.
Summary of Contents for TC6
Page 101: ...Illustrated Parts SORVALL Centrifuges 8 2 Figure 8 1 TC6 Main Assembly ...
Page 103: ...Illustrated Parts SORVALL Centrifuges 8 4 Figure 8 2 TC6 Chassis Assembly ...
Page 105: ...NOTES ...
Page 106: ...NOTES ...
Page 107: ...NOTES ...
Page 108: ...NOTES ...