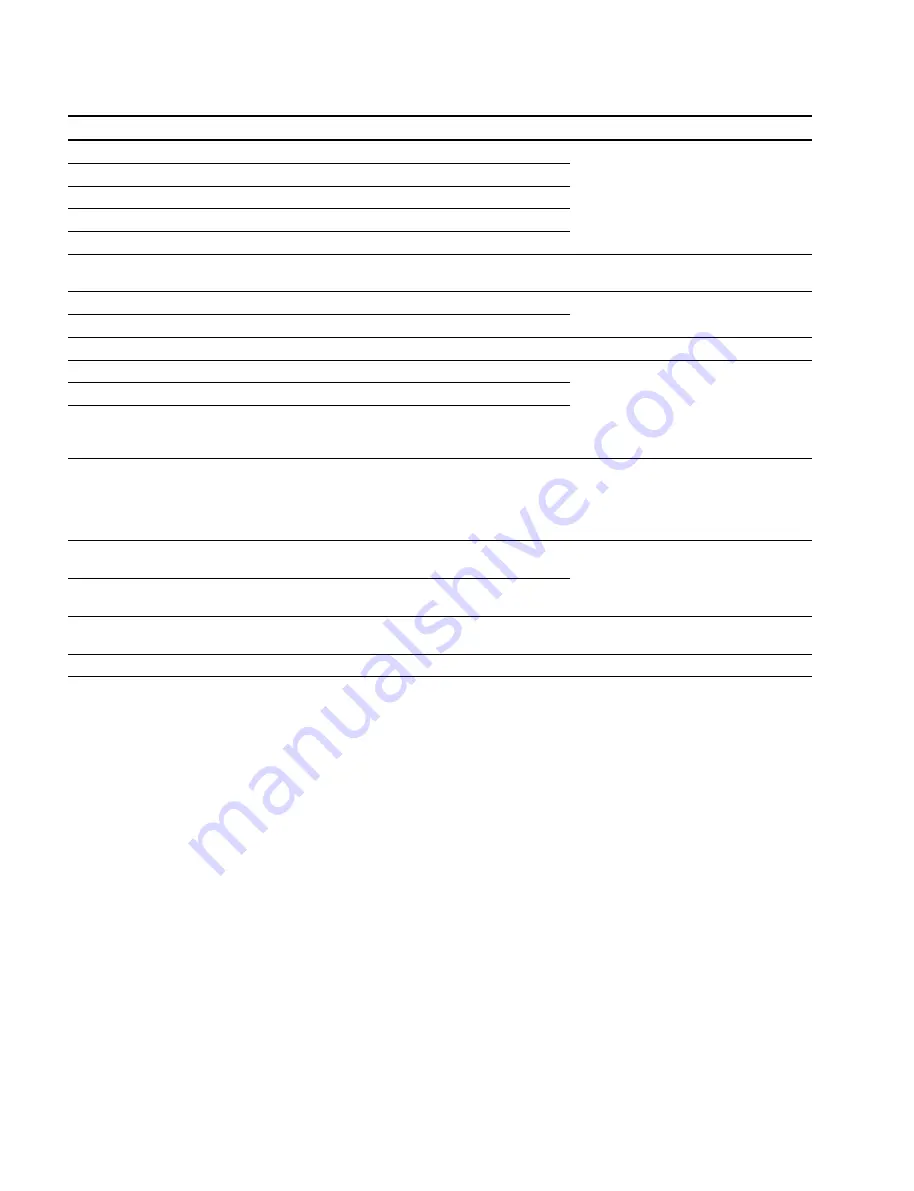
5-150
GY-8240UWD
GY-8240FC
Error Code
Details
Remedy
3x28
Drum overcurrent
Correct according to SV error code
3x2A
Checksum error of SV adjustment value data
3x34
The reference signal from the FM-75 board is not detected during operating
3x3A
Capstan and T reel not synchronized in the speed rate
3xYY
Other errors
4010
Tele-File CRC data differs from calculated value.
Recover.
Replace cassette.
4011
Tele-File Humming code differs from calculated value.
Restore tape to former state.
4012
Failed in verification of block data.
4013
Attempted to update write-prohibit block.
Software error
4014
Power supply of CCM-33 board did not turn ON or OFF
Hardware error
4015
No corresponding block (From CCM-33)
.
Self-diagnosis
4016
Writing ended abnormally (From CCM-33).
.
Replace CCM-33 board, DSP-90 board.
.
Replace harness between CCM-33
board and DSP-90 board.
4017
Failed in communication between IF-780 board and DSP-90 board.
Hardware error
.
Self-diagnosis
.
Replace DSP-90 board.
.
Replace harness between MB-887
board and DSP-90 board.
4018
Failed in communication between label and CCM-33.
Hardware error
Or, failed in communication between DSP-90 board and CCM-33 board
.
Replace cassette.
4019
Checksum error occurred between DSP-90 board and CCM-33 board.
.
Replace CCM-33 board/harness.
.
Replace DSP-90 board.
40F0
Unrecoverable error
Software error
Replace IF-780 board.
40YY
Other errors
5-13. Troubleshooting