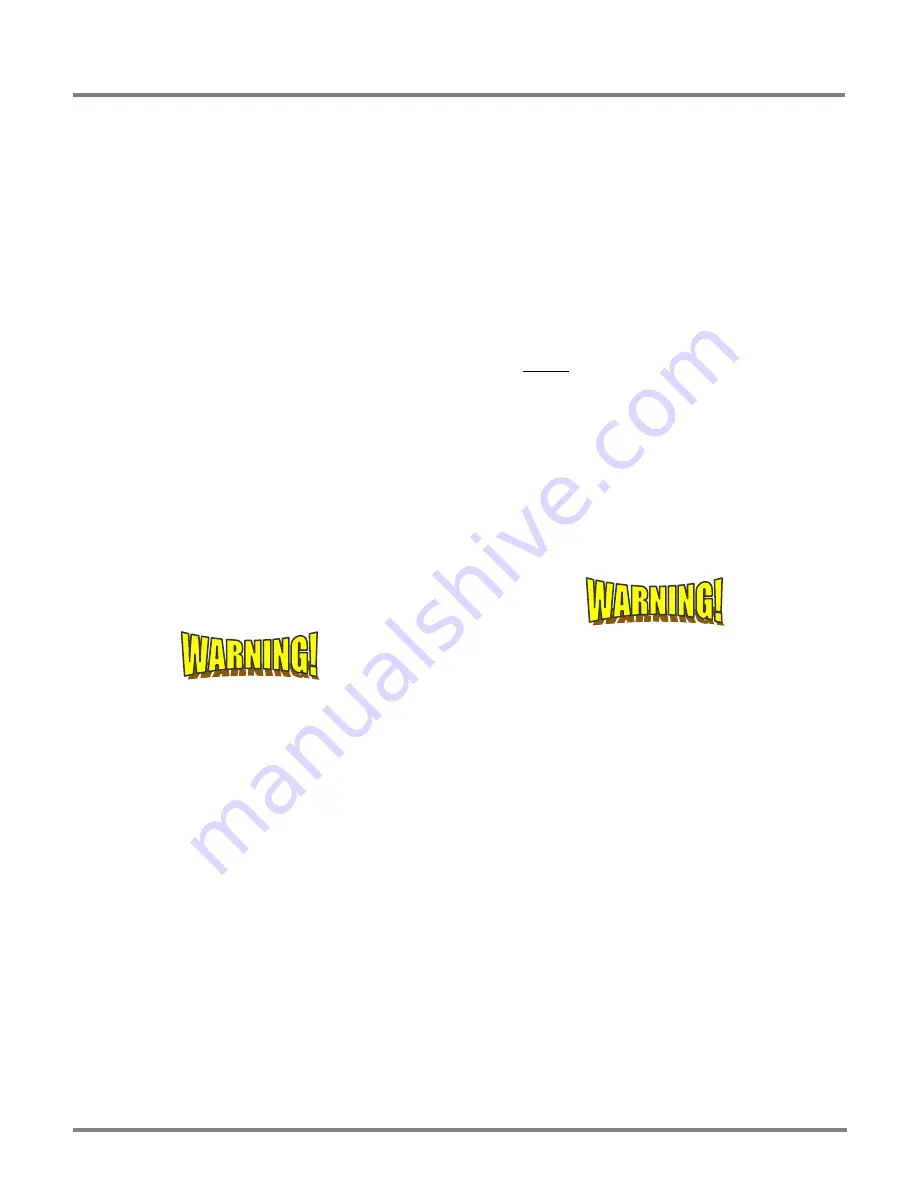
SECTION 6
Glass Thickness Adjustment
The Washer allows for adjustment of the entire upper
assembly to accommodate various thicknesses of
glass. On pneumatic lift equipped Washers, the glass
thicknesses are factory pre-adjusted. However, on
manual glass thickness Washers, a gauge and pointer
is provided as a guide. The following procedure is
used to adjust the glass thickness:
Loosen the jam nut on one corner of the machine.
Move the lower nut up or down.
When the pointer shows the desired glass
thickness on the gauge, retighten the jam nut.
Repeat this procedure at each of the remaining
three corners of the Washer.
Conveyor Chain Idler
Apply several drops of oil to all of the conveyor
chain idlers and take-up sprocket bushings. A
molybdenum disulfide spray lubricant is also
acceptable.
GLASS WASHING MACHINES
18
Drive Chain
Do not overtighten the drive chain. This will
result in a permanently stretched chain.
The drive chain will stretch with use and needs to be
retightened periodically. The take-up sprocket
(located on the infeed side above the gearmotor) is a
chain tensioner mounted on a vertical channel.
Loosen the appropriate nuts and draw the chain
taught by sliding the tensioner into the chain to
remove the excess slack. If the chain has been
stretched beyond the adjustment of the chain
tensioner, remove two links from the chain and
reconnect the chain.
Blower Tube (Air Knife) Adjustment
The blower tubes (air knives) have slots that can be
clogged due to contaminated air, even with the
blower filter in place. If wet stripes are observed on
the glass after running through the Washer, clean the
slots by sliding a piece of flat metal
1
/
32
inch thick or
less through the slot to remove particles from it.
Belt Adjustment
The V-belts will stretch slightly with use and must be
re-tensioned periodically to transmit full power
without slippage. The brush drive belt is tensioned at
the motor by lowering the motor base and locking it
into place.
On Washers that have multiple drive belts, the belts
must be matched in length to assure even distribution
of the load. The belts must be replaced in matched
sets.
Do not
make a set by mixing old and new belts.
Some Washers have a spring-loaded tensioner. The
spring tension is adjusted by using the multi-holed
mounting bracket. If the belts appear to be slipping,
adjust the bracket for more tension.
Control Panel
The control panel is relatively maintenance free.
However, fuses, relays and switches may require
replacement occasionally.
Disconnect the main power to the Washer before
performing any maintenance tasks on the control
panel.
Use a fuse puller to replace any fuses. The circuit
protector fuse may be replaced by hand.
Before replacing any switch, make a notation of
where the wire attaches using the wire color and wire
number. After disconnecting the wires from the
switch, a new switch can be installed. The wiring is
then done to the new switch following the previous
wire notation.
To replace a relay, unplug it from the socket by
pulling straight out. Orient the relay in the same
manner (it will only fit in one way) and push the new
relay in all the way.