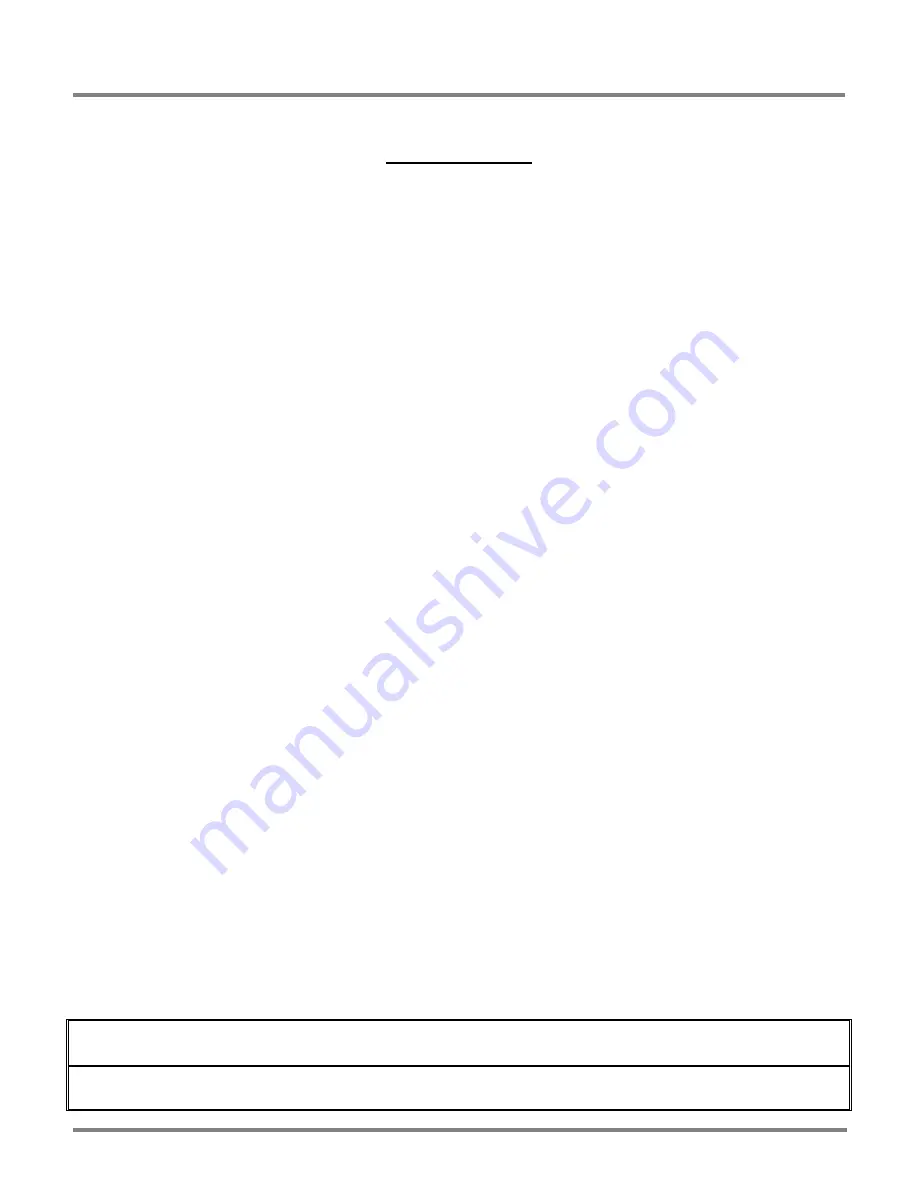
GLASS WASHING MACHINES
3
SECTION 2
DESCRIPTION
GENERAL DESCRIPTION
All Somaca Glass Washing Machines operate in
basically the same way. The glass is scrubbed clean
(sometimes with a pre-wash) by cylindrical bristle
brushes as it is conveyed through the machine on
rubber covered rollers. Spray pipes apply detergent
water followed by rinse water to the top and bottom
of the glass. After this process, the glass is dried by
internal air dryers that remove the water from both
surfaces, leaving the glass thoroughly dry.
Four brush models can be used with regular plant
water to remove such contaminants as fingerprints,
shop dust or glass grindings. Cold water is
satisfactory in most cases; however, warm water is
preferred.
Six brush models with the recirculating detergent
system are recommended for cutting oil, grease and
heavier contaminants.
Four and six brush Washers use the same air blast
method. However, six brush Washers typically have
more air knives for drying with a larger blower.
36 inch GLASS WASHING MACHINE
Model TTW 366, 6 Brush Washer
Capacity -
The Washer accepts 5½ inch glass circles
up to full width sheets from single strength to ¼ inch
thicknesses. The line speed is variable from 0 to 35
feet per minute.
Brushes -
The cylindrical bristle brushes are 3½
inches in diameter, mounted on stainless steel cores
and individually adjusted for proper height by raising
the tilt-top. Brushes are V-belt driven by a common
motor.
Drying System -
A 10 HP blower with an air intake
filter is connected to four air knives; two knives
above the glass and two knives underneath the glass.
Rollers -
The feed and pinch rollers are 2½ inches in
diameter, made with stainless steel journals and
heavy steel tubing with a precision ground Nitrile
covering. The rollers are driven by a
⅛
HP DC gear
motor using chain and sprockets.
Bearings -
The brushes are supported on ball
bearings. The upper pinch rollers are mounted on
pivoting brackets. The rotating action of the pivots
smoothes the movement of the thicker pieces of glass
through the machine.
Frame -
The frame is a one piece steel weldment
with machined upper sidebars. The infeed and
unloading conveyors are two feet long each. All
sections that become wet through normal operation
are either plated, coated or made from a corrosion
resistant material.
Electrical -
The control panel is mounted on the
machine with conduit wiring. All electrical circuitry
is built to NEMA 12 specifications to meet OSHA
requirements. Every panel is UL approved.
The power requirements are 3 phase, 60 cycle,
208/230/460 volts. The electrical panel name plate
specifies the full load amperage.
Water -
A water/detergent solution is applied
through spray pipes; one on either side of the glass
per brush. Threaded plugs on the spray pipe ends
allow for easy cleaning. The water usage is about 4½
gallons per minute without the Aqua-Miser rinse;
about 1½ gallons per minute with. There will be
minimal (zero) consumption (due to drag out and
evaporation) when used with the Aqua-Miser ready
option.
Options -
The recirculating detergent system, miser
rinse system, Aqua-Miser ready (zero water), auto
glass thickness adjustments, power brush adjustment
and hydraulic power tilt-top are all options. A wetted
parts package constructed out of stainless steel for
use with a de-ionized water system is also an option.
MODEL
NUMBER
STYLE BRUSH MOTORS
WIDTH LENGTH HEIGHT
BLOWER
HP
HEATER
TTW 366
36 inch
6 brush
one 2 HP
one
⅛
HP
4 feet
6 inches
6 feet
4 inches
3 feet
6 inches
10 5
kW