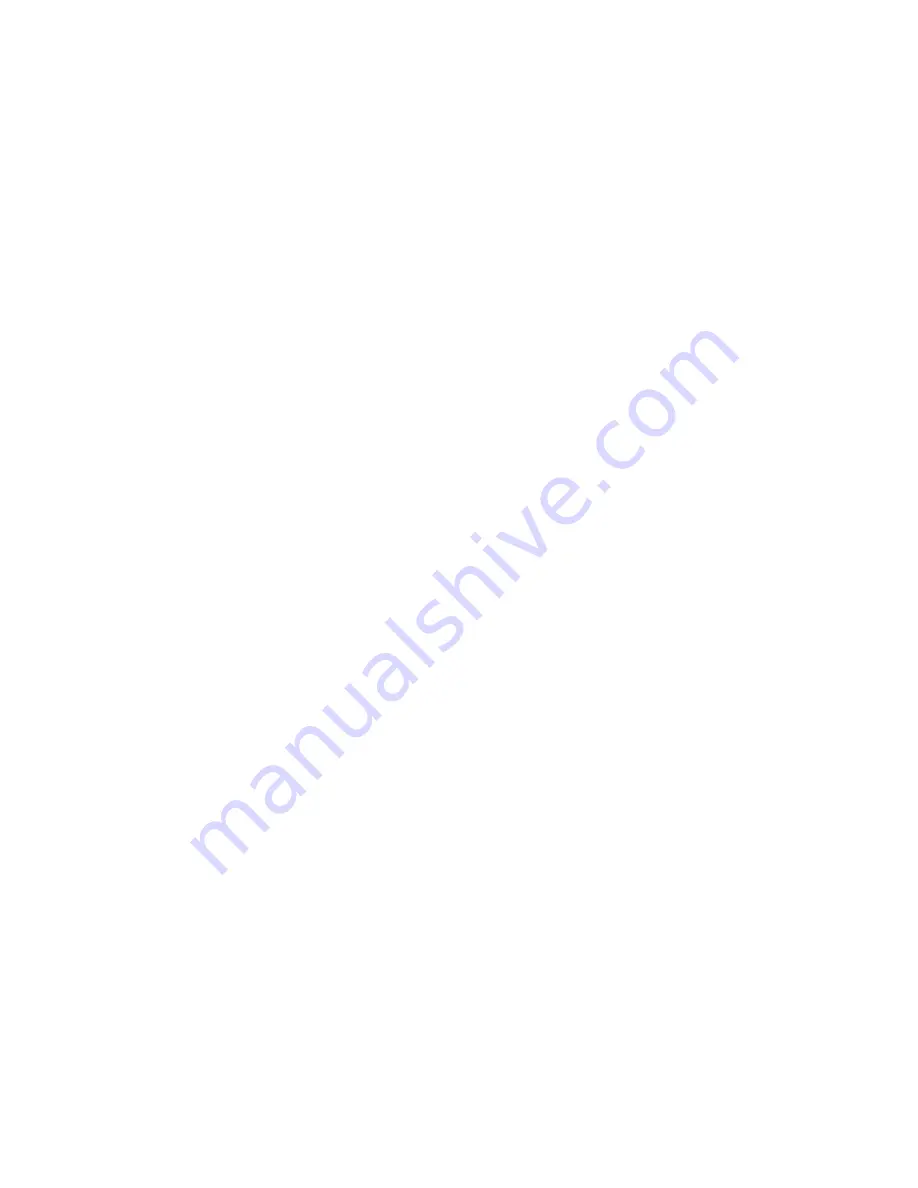
18
Start-Up
Warning…
Use
only
…
No. 2 fuel oils
.
Note:
Do not attempt to start the burner if excess oil has accumulated.
Note:
Do not use gasoline, crankcase draining or any oil containing gasoline.
1.
Make sure that normal water level has been obtained in the boiler and system.
2.
Check that all safety devices are in place.
3.
Check that thermostats are correctly connected and set.
4.
Check that the inside of the boiler is free of any fuel residue or foreign materials and that the ceramic
fiber insulation on the burner door has not been damaged.
5.
Check oil burner nozzle to ensure that the right size and type is installed and tight in the adapter. See
preliminary settings for proper nozzle size and type.
6.
Check electrode settings, as they may have been jarred out of position during transportation. See burner
instructions for nozzle and electrode setting
7. Check that the Burner mounting bolts are tight.
8.
Lubricate burner motor and circulator motor if required.
9.
Open all fuel valves.
10.
Set room thermostat to call for heat.
11.
Set aquastat high limit between 180
o
F and 200
o
F
12.
Turn service switch on. Burner should start. On one pipe fuel system only you may have to bleed the oil
system. To bleed attach a clear plastic tube to the oil pump bleed port and allow oil to run until all the
air is out of the oil suction line feeding the oil burner. See burner and fuel pump manufacturers
recommendations for proper bleeding of the fuel system.
13.
Turn “OFF” burner and install pressure gauge into the gauge port on the pump. See the burner
manufacture’s manual for location of ports.
14.
Start burner again and check oil pressure for conformance to preliminary oil burner settings. Adjust if
necessary. See oil burner manufacturer’s instructions for pump adjustment.
Start-up Equipment
THE FOLLOWING PROPER COMBUSTION INSTRUMENTS ARE REQUIRED TO DETERMINE
PROPER AIR ADJUSTMENTS AND DRAFT WHEN SETTING UP OR SERVICING THE BURNER.
1.
CO
2
Analyzer
2.
CO Analyzer
3.
Draft gauge
4.
Fuel pressure gauge
5.
Stack thermometer
6.
Smoke tester
7.
Manometer
Do not attempt to make any adjustments or start the boiler without the proper equipment.
Burner Adjustments
Consult the enclosed burner manufacturer’s installation and operation manual for proper
adjustment of the burner.