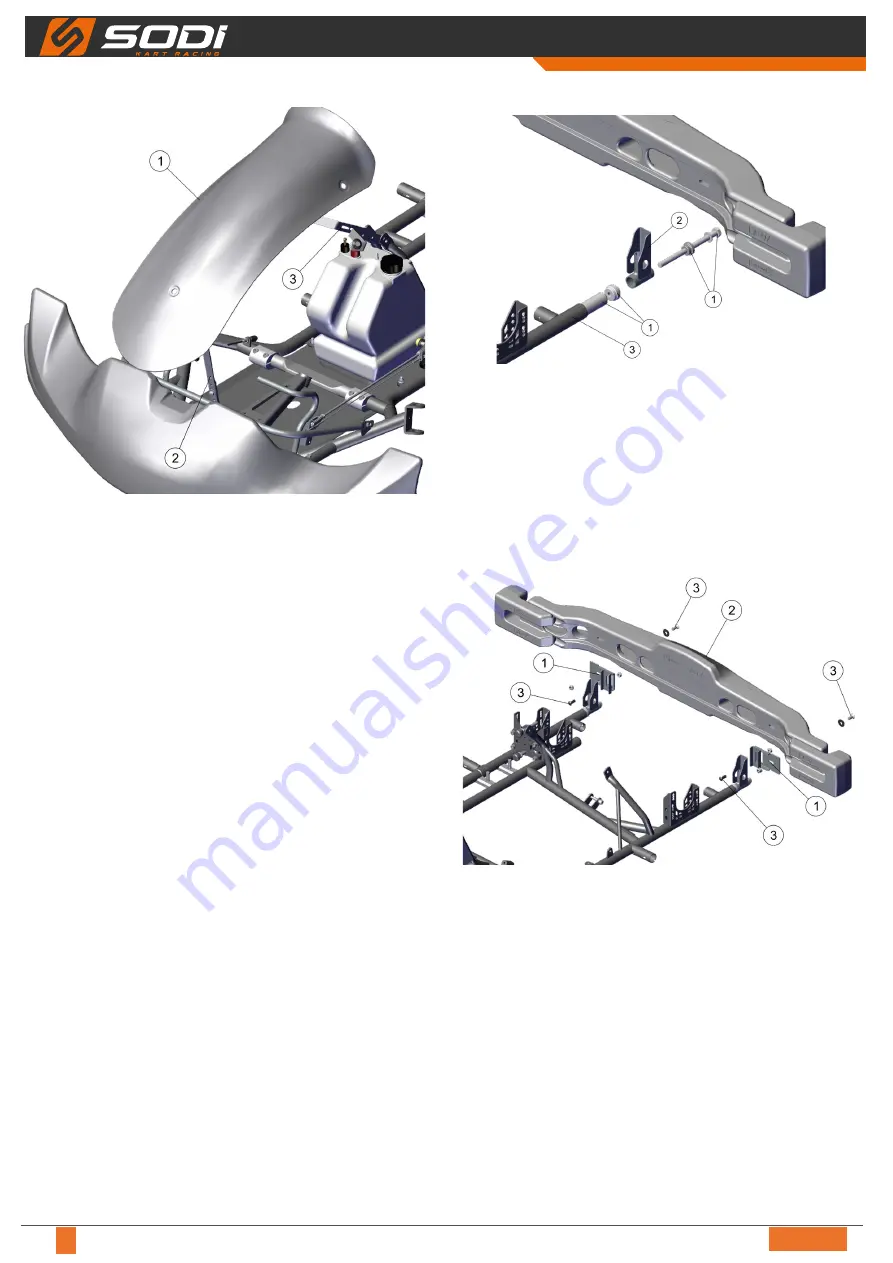
10/2022
14
EN
USER AND MAINTENANCE MANUAL
Étape 9
Legend
1 Nassau panel
2 Lower support
3 Upper support
● Tighten the nassau panel (1) on its supports (2) and (3)
with screws, nuts, and washers.
3.9 - Mounting the rear protections
Legend
1 Mounting kit
2 Bumper support
3 Tube chassis
● Assemble the mounting kit (1) with the element of the
bumper support (2).
● Mount the assembly in the tube chassis (3), tighten with
the screw of the fixing kit (1).
● Apply the same procedure for the other side.
Legend
1 Bumper support
2 Bumper
3 Screw + nut
● Assemble bumper support (1) on the bumper (2) using
screws and nuts (3).
● Assemble the bumper (2) on the chassis with screws and
nuts (3).
Summary of Contents for RS3 KZ DD2
Page 1: ...MAN_Sigma_EN_02 USER AND MAINTENANCE MANUAL EN ...
Page 41: ...MAN_Sigma_EN_02 USER AND MAINTENANCE MANUAL 41 EN 9 Homologation ...
Page 42: ...10 2022 42 EN USER AND MAINTENANCE MANUAL ...
Page 43: ...MAN_Sigma_EN_02 USER AND MAINTENANCE MANUAL 43 EN ...
Page 44: ...10 2022 44 EN USER AND MAINTENANCE MANUAL ...
Page 45: ...MAN_Sigma_EN_02 USER AND MAINTENANCE MANUAL 45 EN ...
Page 46: ...10 2022 46 EN USER AND MAINTENANCE MANUAL ...
Page 47: ...MAN_Sigma_EN_02 USER AND MAINTENANCE MANUAL 47 EN ...
Page 48: ...10 2022 48 EN USER AND MAINTENANCE MANUAL ...
Page 49: ...MAN_Sigma_EN_02 USER AND MAINTENANCE MANUAL 49 EN ...