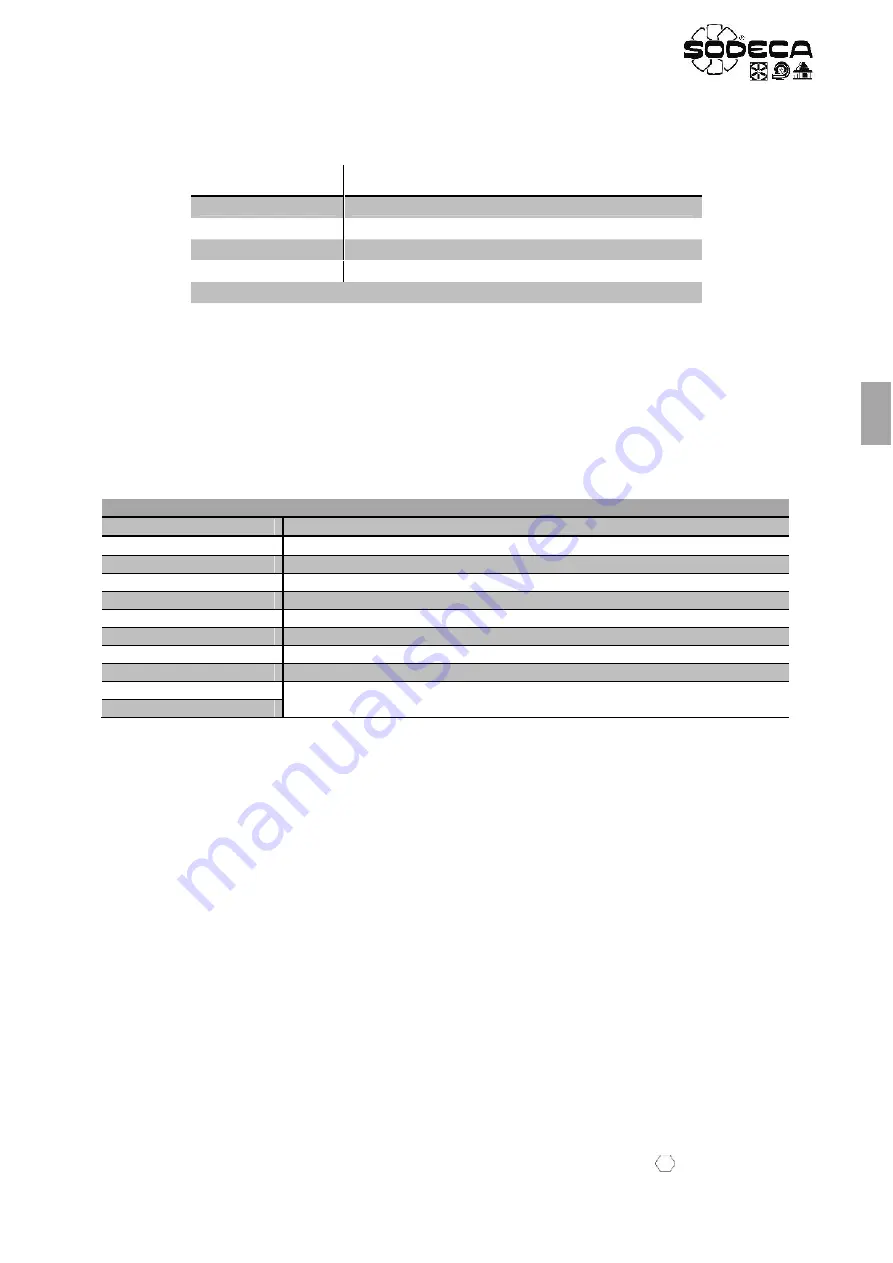
12
EN
7.2 SETPOINT ADJUSMENT OF THE CO2 CONCENTRATION
The setpoint is adjusted in the
parameter. This parameter is shown as a percentage and will translate to a different
value of CO
2
concentration in ppm, subject to the chosen scale of the probe.
Scale
CO
2
concentration in ppm
per every 10% of the Setpoint
450-1850 ppm
140 ppm
*
0-1000 ppm
100 ppm
0-1500 ppm
150 ppm
0-2000 ppm
200 ppm
(*) Increase for every 10%, add 450 ppm to obtain the real value
7.3 WIRING
Before the start of the programming, wire the L1-L2-L3 input phases when using three phase equipment and wire the
L1-L2/N input phases when using single phase equipment.
Once the
“CO2”
control mode is selected, that is after introducing the parameters of the CO
2
mode table (section 7.1),
wire the drive as seen in the picture.
(See Fig. 9.)
.
The RUN signal must be connected between the terminals 1 & 2, and the switch is always closed, the drive will start
automatically when given power. If the user wants to stop the operation with a selector, timer, etc.… Set up a free
potential contact in series between the terminals 1 & 2.
7.4 PROBE SI-CO2 IND CONFIGURATION
It’s advised to adjust the scale of the probe SI-CO2 IND between 0 and 1000 ppm and the output signal 0-10 V. This
adjustment by means of the jumpers JP5 and JP1 respectively. Remove the cover of the probe to find this jumpers. (
See
Fig. 10)
7.5 “CO2” OPERATION MODE
1.
Close the RUN switch connected between the terminals 1 & 2 to start the drive. The display will show
and
the drive will increase the speed until reaching the objective speed. This speed is subjected to the CO2
concentration level detected by the probe and the setpoint adjusted in
.
2.
If the CO2 level goes over the setpoint adjusted in
the drive will increase the speed in order to decrease the
CO2 level below the setpoint.
3.
If the CO2 level goes below the setpoint adjusted in
the drive will decrease the speed in order to keep the
CO2 level below the setpoint.
4.
If the user wants the drive to be always working, short-circuit the terminals 1 & 2 with a copper wire.
5.
If the
parameter has a value >0.0s, the drive will disconnect automatically when the CO2 level goes below
the setpoint for a certain amount of time, adjusted in this parameter. If this feature is active and the CO2 level goes
below the setpoint for an amount of time higher than the one set in
, the drive will stop even when the RUN
switch is closed and won’t start again until the CO2 level goes over the setpoint.
6.
While the drive is ON, the user can see the motor consume pressing the Navigator key
>2 seconds.
VSD*/A Wirings
Terminal VSD*/A
Description
L/N+PE
Single phase input, only for VSD1/A
L1/L2/L3+PE
Three phase input, only for VSD3/A
U/V/W+PE
Three phase motor output
1
+24 VDC (100 mA)
2
Run signal
6
Analog input 1
7
0 V analog input
9
0 V
10
Output relay
11
‘Drive OK’ = Closed
Summary of Contents for VSD/A
Page 2: ......
Page 3: ...Fig 6 Fig 9 VSD A...