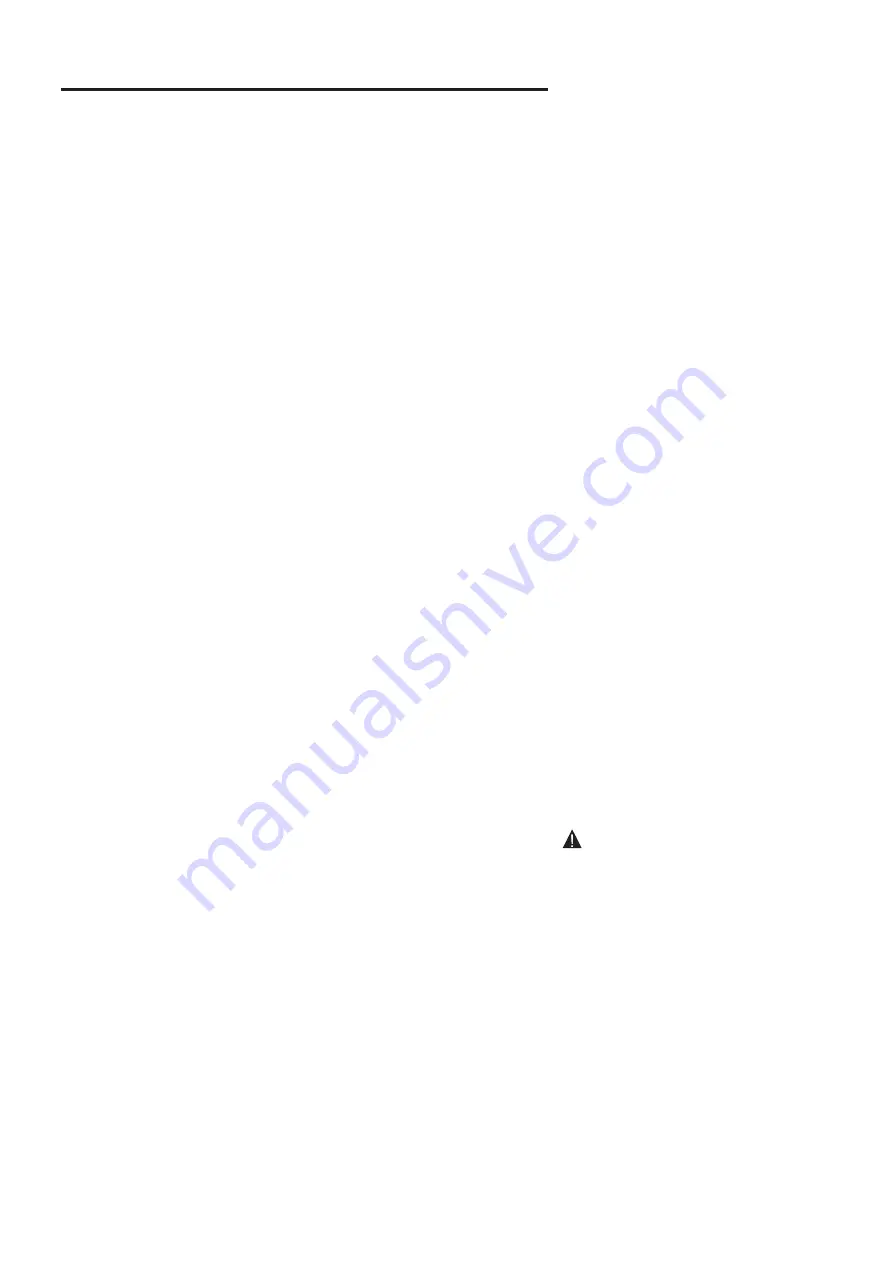
ü
Always make sure work platform is in stowed
position - blocked or the weight removed by a
suitable lifting device before disconnecting the
hydraulic hose from the motor/pump unit to the lift
cylinder.
ü
When raising a portion of the machine, be sure that
adequate blocking is properly positioned - Do not
depend on lifting device to hold and secure weight.
ü
If a part resists removal, check to see if all fasteners,
electrical wiring, hydraulic lines, etc., have been
removed or that other parts are not interfering.
Parts should be thoroughly inspected before
restoring to service at the time of reassembly. Burrs,
nicks or scratches may be removed from machined
surfaces by honing or polishing with #600 crocus
cloth, followed by a thorough cleaning in an
approved cleaning solvent, and blown dry with
compressed air. Do not alter the contour of any part.
If this operation does not restore the part to a
serviceable condition, replace the part.
Replace all O-rings, seals, and gaskets at
reassembly. Use new roll pins or cotter pins. Dip all
packing rings and seals in hydraulic oil before
reassembling in cylinder and manifold installations.
Replace any part having imperfect threads. In
general, units that have been disassembled can be
reassembled by reversing the order of disassembly.
Remember that the service life of a machine can be
increased by keeping dirt and foreign materials out
of the vital components. Precautions have been
taken to safeguard against this; shields, covers,
seals and filters are provided to keep air and oil
supplies clean; however, these items must be
maintained on a scheduled basis in order to function
properly.
At any time air or oil lines are disconnected, clean
surrounding areas as well as the opening and
fittings themselves. As soon as a line or component
is disconnected, cap or cover all openings to
prevent the entry of dirt or foreign materials.
New parts should remain in their container until they
are ready to be used.
Clearly mark or tag hydraulic lines and electrical
wiring connections when disconnecting or removing
them from unit. This will assure that they are
correctly reinstalled.
Proper assembly is critical to the successful
rebuilding of any unit. Carefully inspect any parts
which are to be reused. If in doubt, replace.
“SAFETY FIRST”
is a good slogan.
Replace any guards and protective devices that
have been removed to carry out maintenance and
repair work.
■
Maintenance schedules
Snorkel has established a Preventive Maintenance
Schedule that includes:
ü
Daily Maintenance (Operator’s Inspection)
ü
90 Day or 150 Hour (frequent) Maintenance
ü
Yearly or 500 Hour (annual) Maintenance,
These schedules should ensure the detection of any
defective, damaged or improperly secured parts
and provide information regarding lubrication and
other minor maintenance items.
The Maintenance Schedule following, outlines the
requirements of these maintenance checks for each
time interval. The Operator’s Pre-operational
inspection must be performed by a trained operator.
All other maintenance and inspections must be
performed by a trained service technician only.
Note that the 90 Day or 150 hour (frequent) and
yearly or 500 hour (annual) Maintenance, require
use of the Preventive Inspection Maintenance
Checklist to pinpoint all inspection items. Retain a
copy of these forms for your records.
They also require that all placards and decals on the
unit are to be inspected.
All placards and decals must be in place and legible.
Use the placards installation drawing and parts
listing in the repair parts section 1 of this manual to
check these placards and decals.
Snorkel recommends that you make additional
copies of the Preventive Inspection Maintenance
Checklist forms for your use in performing these
F a i l u r e t o p e r f o r m t h e P r e v e n t i v e
Maintenance at the intervals outlined in the
Maintenance Schedule may result in a unit
being operated with a defect that could result
in INJURY or DEATH of the unit operator. DO
NOT allow a unit to be operated that has been
found to be defective.
Repair all defects before returning the unit to service
Maintenance Information
DANGER