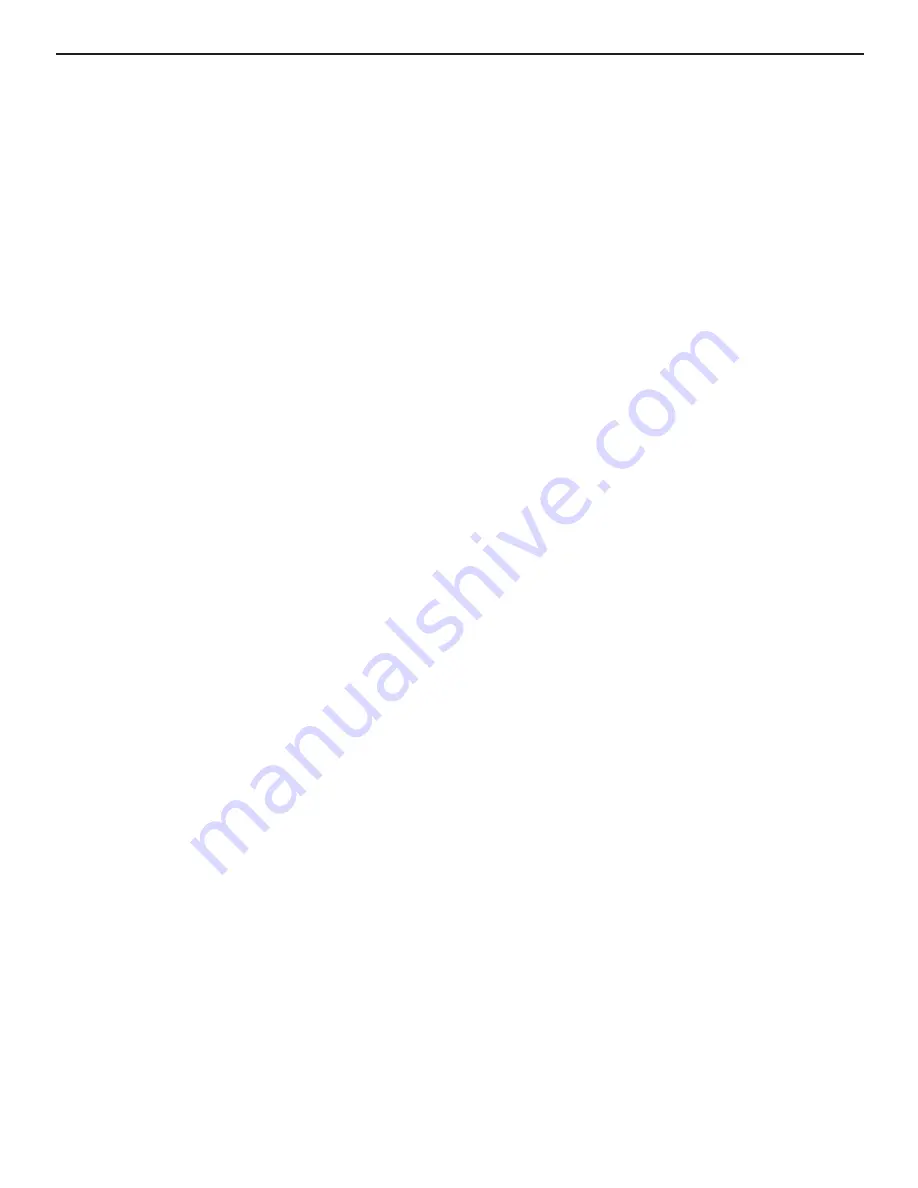
X-Axis Travel (w/tailstock installed)
15”
Y-Axis Travel
7-3/8”
Mill Specifications
Column Diameter
3-1/8”
Dial Calibration Drill-Coarse Feed
0.042”
Dial Calibration Mill-Fine Feed
0.042”
Drawbars Size (included)
12 mm, 3/8”
Drill Chuck Size (included)
1/2”
Drill Chuck Arbor Size (included)
MT3/JT33
Feed Rates
N/A
Head Rotation
360 Degrees
Head Travel
3-1/4”
Quill Diameter
2-3/4”
Quill Travel
3-5/8”
Spindle Center to Front of Chuck
3-3/16”
Spindle Center to Lathe Spindle Flange
5-1/2”
Spindle Center to Support Column
6-7/8”
Spindle to Table Distance(min-max)
6-1/4” - 13”
Spindle Speeds
12 (125-1600 rpm)
Spindle Taper
MT3
Tool Size Limits
1”
X-Axis Travel
6-5/8”
Y-Axis Travel
7-3/8”
Electrical
Amperage
11 amps
Horsepower
3/4 hp
Motor Type
A/C
Phase
Single
Voltage
110 Volts A/C
Full Specifications
26-2
Or Visit www.smithy.com
Summary of Contents for Midas 1220 XL
Page 6: ......