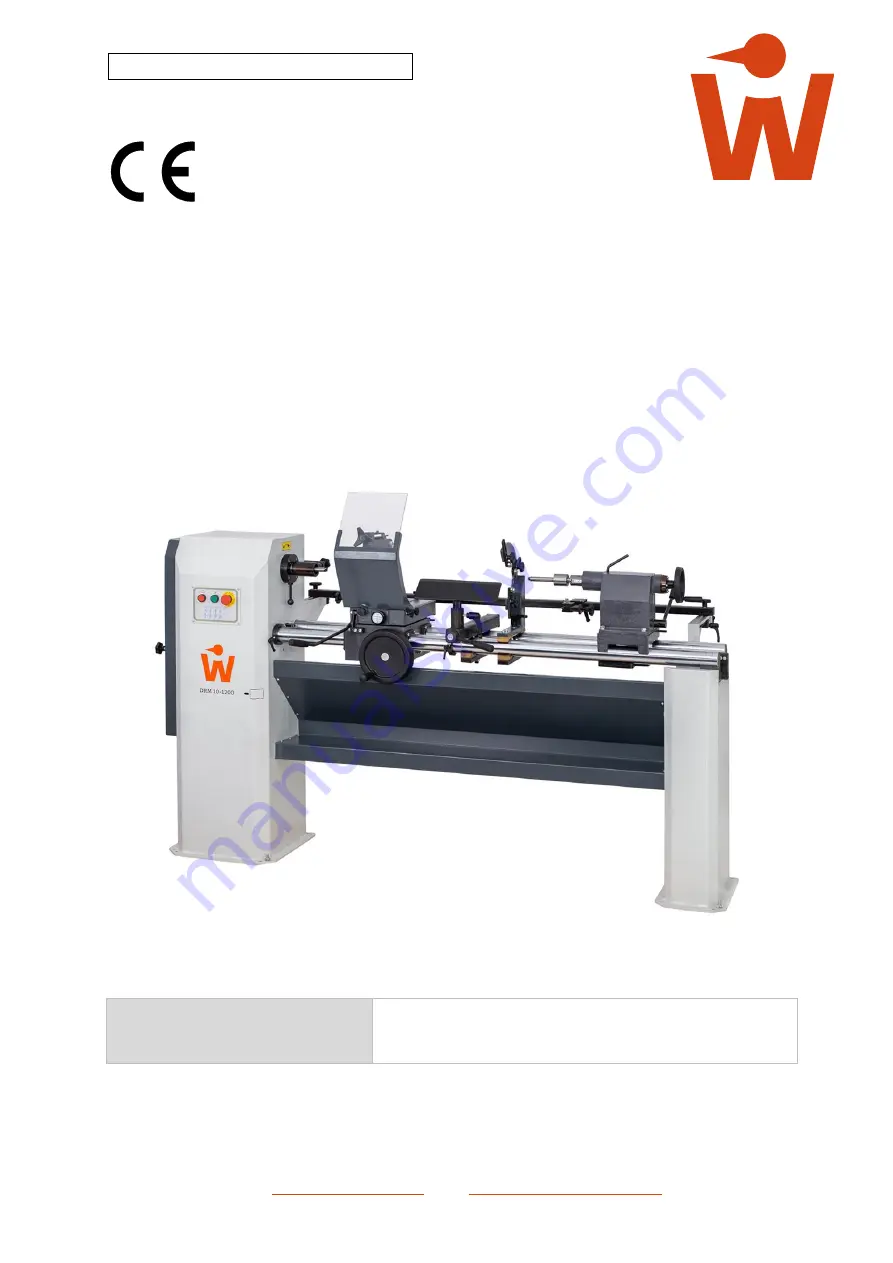
TRANSLATION OF THE ORIGINAL VERSION
WOOD
PECKER
HOKUBEMA Maschinenbau GmbH
Graf-Stauffenberg-Kaserne, Binger Str. 28 | Halle 120
DE 72488 Sigmaringen | Tel. +49 07571 755-0
E-Mail:
https://www.ichbinwoodpecker.de
Operating Manual
Copy Woodturning Lathe
WOOD
PECKER
DRM 10-1200
Machine Type:
DRM 10-1200