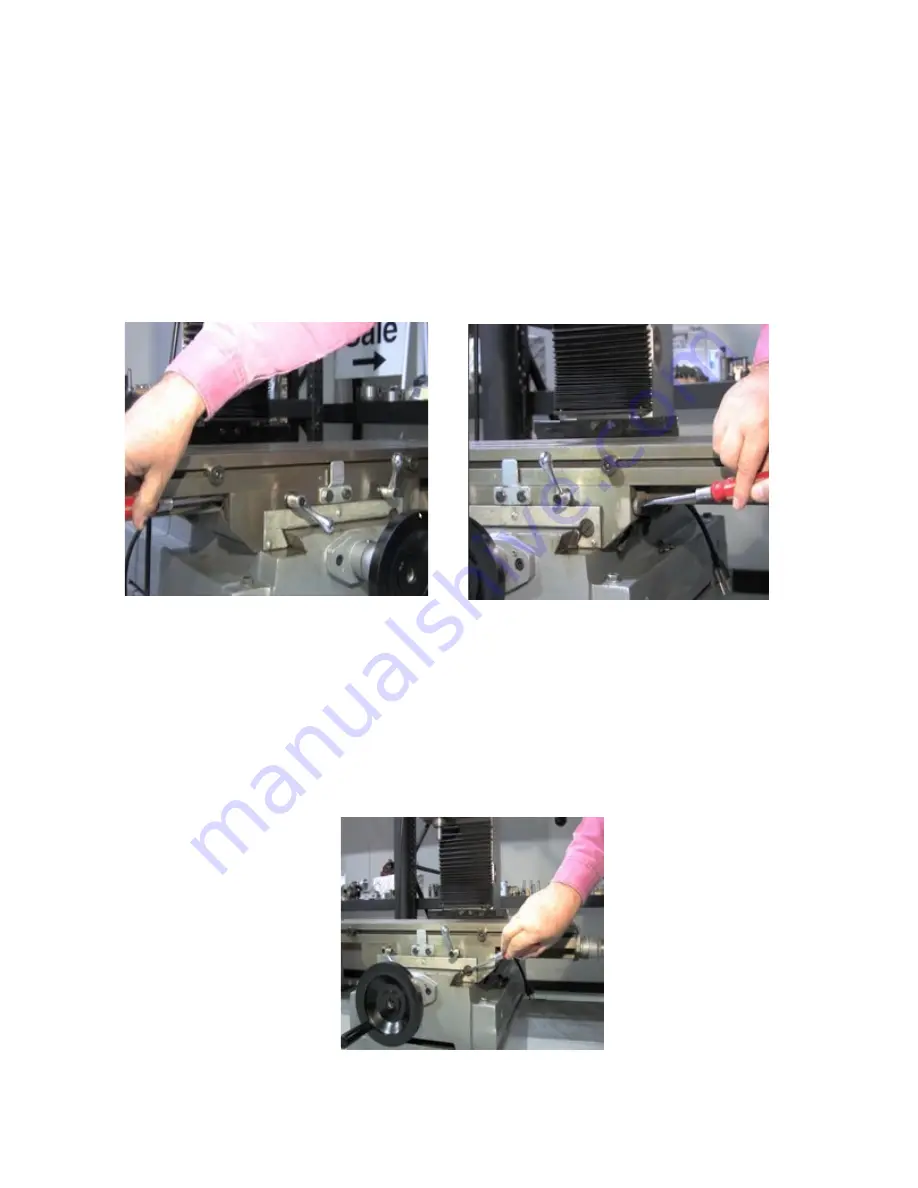
X Axis Gib Adjustment
There are two adjustment screws for X, Y and Z axis. One on the left and the
other one on the right end which shown in the images below. Turning in the
right screw will adjust the gib tighter and turning in the left screw will makes
everything loose. Have both of them loose, and then start turning the right
screw a little bit of a time to make it tighter. When you fill drag on the hand
wheel that's the time to stop and tighten the other screw on the left. You
tighten both screws to hold the device.
Y Axis Gib Adjustment
There are also two adjustment screws. One in the front and the other one on
the back end which also shown in the image below. To loosen the gib for Y-
axis, screw out the front screw and screw in the rear screw. While screw in
the front screw and screw out the rare screw will tighten the gib.
20
Summary of Contents for MI-409MZ
Page 1: ...Smithy MI 409MZ Operator s Manual 1 ...
Page 31: ...Chapter 13 Parts Diagrams in work ...
Page 32: ...Chapter 14 Electrical Diagrams ...
Page 33: ......