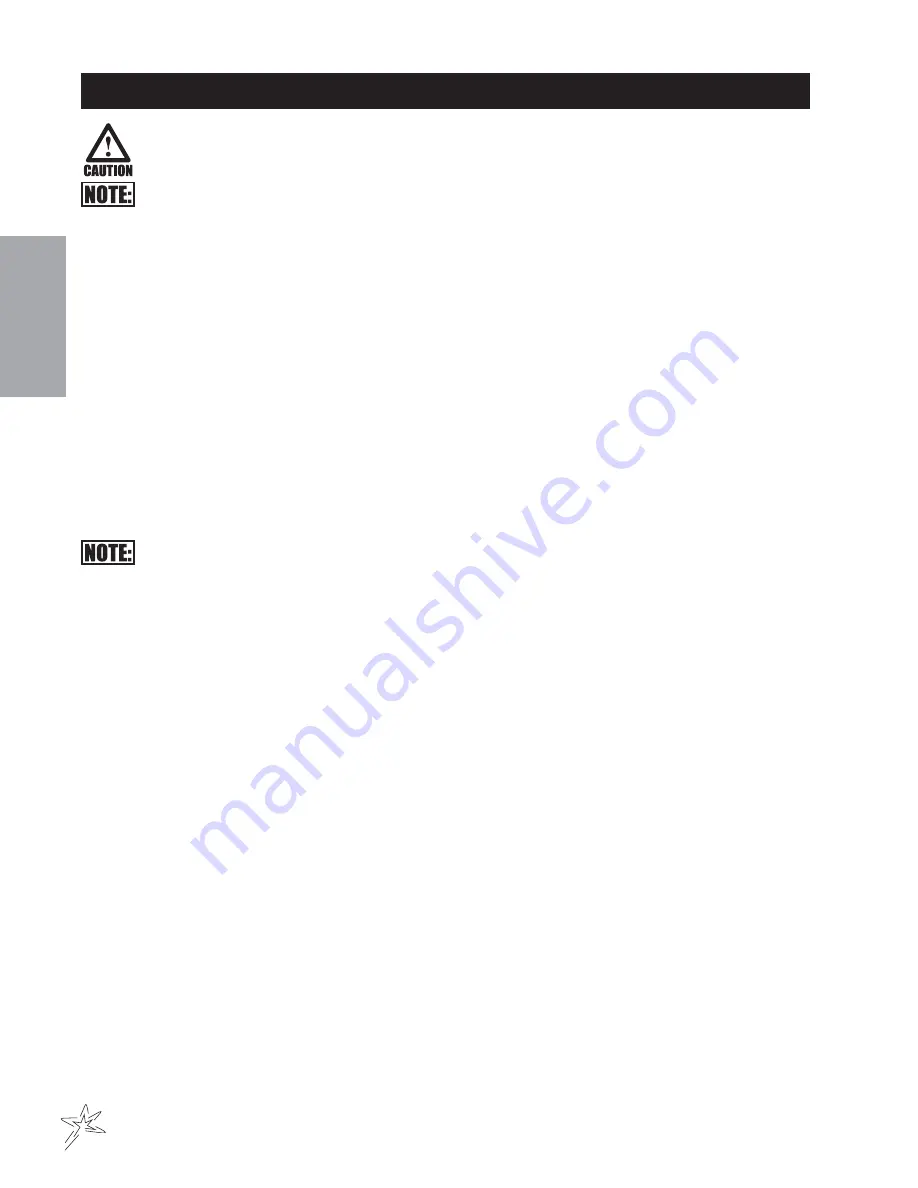
4
Service
MAINTENANCE
Before servicing or making adjustments to machine, stop engine and remove key from ignition.
Use all procedures and parts prescribed by the manufacturer's. Read the engine manual
before operation.
The suggested maintenance checklist is not offered as a replacement for the manufacturer’s but as a supple-
ment. You must adhere to guidelines established by manufacturer for warranty coverage. In adverse conditions
such as dirt, mud or extreme temperatures, maintenance should be more frequent.
LUBRICATION
Use No. 2 General purpose Lithium Base Grease and lubricate every 100 hours. The Super Rake has one
grease fitting located in bearing on steering shaft.
AIR CLEANER ON ENGINE
1. Unhook clips on both sides of cover and remove cover.
2. Carefully slide pre-cleaner off cartridge.
To service pre-cleaner, wash in liquid detergent and water. Squeeze dry in a clean cloth. Saturate in
engine oil. Squeeze in clean, absorbent cloth to remove all excess oil. Replace if very dirty or damaged.
3. Remove knob and plate. Carefully remove cartridge to prevent debris from entering carburetor. To service
cartridge, clean by tapping gently on flat surface. Do not oil cartridge. Replace if very dirty or damaged.
Do not use petroleum solvents, eg., kerosene, which will cause cartridge to deteriorate. Do
not use pressurized air to clean cartridge. Pressurized air can damage cartridge.
4. Reinstall cartridge, plate and knob.
5. Reassemble pre-cleaner on cartridge.
6. Replace cover and reattach clips to body.
AIR CLEANER ON FENDER
1. Remove end cap and filter element, clean by tapping gently on flat surface. Do not oil cartridge. Replace if
very dirty or damaged.
2. Remove air clearner cap and clean. Cap can be washed in solvent, make sure its dry before reinstalling.
HYDRAULIC OIL
1. Use SAE 10W-40 API Service SG/SH/CD/EC-11 motor oil.
2. For proper warranty, change oil every 500 hours or annually, which ever is first and change filter after the
first 20 hours, then at 100 hours, then every 250 hours thereafter.
3. The oil level should be 2" to 2
1
/
2
" from top of fill neck when fluid is cold. Do not overfill.
4. After changing oil and/or filter, run the machine for a few minutes. Check oil level and for leaks.
5. Always use caution when filling hydraulic oil tank or checking level to keep system free of contaminants.
Check and service more frequently when operating in extremely cold, hot or dusty conditions.
6. If natural color of fluid is now black or smells burnt, it is possible that an overheating problem exists.
7. If fluid becomes milky, water contamination may be a problem.
8. If either of the above conditions happen, change oil and filter immediately after fluid is cool and find cause.
Take fluid level readings when system is cold.
9. In extreme temperatures you can use straight weight oil. We recommend SAE 30W API Service SG when
hot (above 90°F (33°C)) and SAE 10W API Service SG when cold (below 32°F (0°C) ambient temperature.
Use either motor oil or hydraulic oil, but do not mix.
10. Oil being added to the system must be the same as what is already in the tank. Mark tank fill area as to
which type you put in.
Summary of Contents for 13-550-C
Page 13: ...NOTES...
Page 18: ...16 Diagrams WIRINGSCHEMATIC2WHEELDRIVE...
Page 19: ...17 Diagrams HYDRAULICSCHEMATIC2WHEELDRIVE HYDRAULCISCHEMATIC3WHEELDRIVE...
Page 20: ...18 Parts MAINFRAMEDRAWING...
Page 22: ...20 Parts MAINFRAMEDRAWING...
Page 24: ...22 Parts ACCELERATORLINKAGEDRAWING...
Page 26: ...24 Parts RIGHTFENDERANDENGINEDRAWING...
Page 28: ...26 Parts LEFTFENDERANDTANKDRAWING...
Page 30: ...28 Parts CONSOLEDRAWING...
Page 32: ...30 Parts TWOWHEELDRIVEFRONTFORKDRAWING...
Page 34: ...32 Parts THREEWHEELDRIVEFRONTFORKDRAWING...
Page 36: ...34 Parts ENGINEANDPUMPDRAWING...
Page 38: ...36 Parts REARAXLEDRAWING...
Page 40: ...38 Parts HYDRAULICOILFILTERDRAWING HYDRAULICOILTANKDRAWING...
Page 42: ...40 Parts REARRAKELIFTDRAWING...
Page 44: ...42 Parts ON OFFVALVEDRAWING...
Page 46: ...44 Parts HYDRAULICVALVEDRAWING...
Page 48: ...46 Parts 13 110VARIABLEPUMPDRAWING...
Page 50: ...48 Parts 13 032FRONTWHEELMOTOR 4 9C I DRAWING...
Page 52: ...50 Parts 13 615REARWHEELMOTOR 7 5C I DRAWING...
Page 54: ...52 Accessories 13 505LIFTASSEMBLYDRAWING...
Page 60: ...58 Accessories 13 355HYDRAULIC3 BANKVALVEDRAWING...
Page 62: ...60 Accessories 13 644SANDPLOWDRAWING...
Page 64: ...62 Accessories 13 644SANDPLOWDRAWING...
Page 66: ...64 Accessories 13 107INFIELDSCARIFIERDRAWING...
Page 68: ...66 Accessories 13 116WEEDCULTIVATORDRAWING...
Page 70: ...68 Accessories 13 199EDGERKITDRAWING...
Page 72: ...70 Accessories 13 577SCARIFIERVERTICALBLADESDRAWING...
Page 74: ...72 Accessories 13 111DRAGMATKITDRAWING...
Page 76: ...74 Accessories 42 02684 213CM STAINLESSSTEELTOURNAMANTRAKEDRAWING...
Page 78: ...76 Accessories 42 02684 213CM STAINLESSSTEELTOURNAMENTRAKEDRAWING...
Page 80: ...78 Accessories 42 12872 183CM STAINLESSSTEELTOURNAMENTRAKEDRAWING...
Page 82: ...80 Accessories 42 12872 183CM STAINLESSSTEELTOURNAMENTRAKEDRAWING...
Page 84: ...82 Accessories 13 438RAKEASSEMBLYWITHFINISHINGBLADESDRAWING...
Page 86: ...84 Accessories 13 606RAKEASSEMBLYWITHLEXANBLADESDRAWING...
Page 88: ...86 Accessories 13 298FANRAKEATTACHMENTDRAWING...
Page 90: ...88 Accessories 26 007PROFESSIONALINFIELDFINISHERDRAWING...
Page 92: ...90 Accessories 26 008FLEXACTIONFIELDFINISHERDRAWING...
Page 94: ...92 Accessories 26 008FLEXACTIONFIELDFINISHERDRAWING...
Page 96: ...94 Accessories 34 191BOXGRADERDRAWING...
Page 98: ...96 Accessories SUPERRAKELIFTASSEMBLY...
Page 100: ...98 Accessories 34 190SPIKERDRAWING...
Page 102: ...100 Accessories SUPERRAKE LIFTASSEMBLY...
Page 104: ...102 Reference NOTES...
Page 108: ......