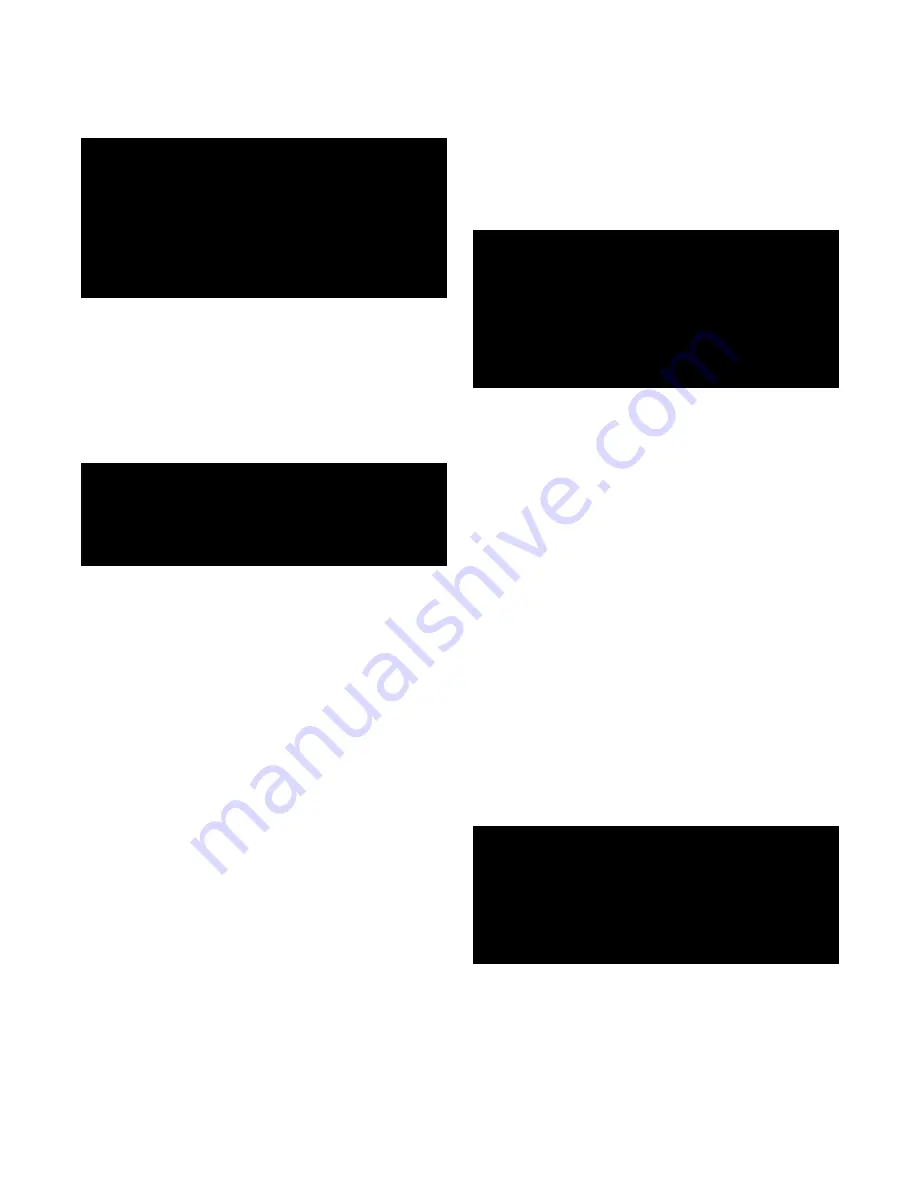
Page 21
SERIES 28RTS/HE BOILER INSTALLATION AND OPERATION INSTRUCTIONS
Line voltage fi eld wiring of any controls or other devices
must conform to the temperature limitation of type TEW
wire at 95°F, 35°C above room temperature. Use copper
conductors with a minimum size of #14 awg.
BOILER OPERATION
WARNING: Before proceeding read and fully
understand the instructions contained in this
manual. Do not attempt to operate this boiler if
it has not been installed in accordance with the
guidelines set forth in this manual. Failure to
comply with this warning can result in extensive
property damage, severe personal injury or
death!
CAUTION: The supply temperature of a boiler set
for a 20°F, 11°C temperature rise must not be below
140°F, 60°C for an oil boiler, 149°F, 65°C for a gas
boiler. Failure to protect the boiler from low return
water temperatures will damage the boiler, voiding
the warranty!
Water Boilers
Fill the boiler and all of the radiation with water to the
required system pressure. Completely purge the system
of air and adjust the system pressure as needed.
CAUTION: Thermal shock of water boilers must be
avoided! Water circulation must be established
before the burner is fi red. If hot standby is required,
special piping and operation procedures are
necessary, consult your Smith representative.
Failure to protect the boiler from thermal shock can
damage the boiler, voiding the warranty!
Water Boilers
Follow the burner manufactures lighting instructions
that were supplied with the burner.
WARNING: Never attempt to start the burner
if the combustion chamber contains excess
oil or gas, when the boiler is full of vapor or
the combustion chamber is very hot. Failure
to comply with this warning can result in an
explosion causing extensive property damage,
severe personal injury or death!
A properly adjusted gas burner on high fi re will produce
a maximum CO
2
of 10.4% with a maximum CO of 300
ppm. When fi ring on oil at high fi re, the burner should
be adjusted to produce a maximum CO
2
of 13.4%
with only a maximum trace of smoke. The fl ue gas
samples should be taken at the smoke hood. Confi rm
proper burner adjustment with a calibrated combustion
analyzer.
BURNER INSTALLATION
WARNING: The burner must be installed in
accordance with the burner manufactures
instructions. Check the boiler rating plate to
make sure that the boiler is for the type of fuel
that will be used. If it isn't, do not connect the
burner to the fuel supply. Failure to comply with
this warning can result in extensive property
damage, severe personal injury or death!
Follow the burner manufacturer’s installation instructions
for the proper installation, fuel piping, wiring, burner
adjustment and servicing. Mount the burner per the
instructions on page 13.
When applicable, provisions for vent, bleed and gas
relief lines must be made in accordance with the latest
revision of ANSI Z223.1/NFPA 54.
WARNING: Never use an open fl ame to test for
gas leaks. Always use an approved leak
detection method. Failure to comply with this
warning can cause extensive property damage,
severe personal injury or death!
Whenever the gas supply piping is pressure tested
the boiler gas controls must be protected. If the test
pressure is equal to, or less than 1/2 psig, 3.5 kPa
isolate the boiler by closing the manual shut off valve in
the gas supply pipe to the boiler. If the test pressure is
greater than, or equal to 1/2 psig, 3.5 kPa, disconnect
the boiler and its individual shut-off valve from the gas
supply.
ELECTRICAL WIRING
Electrical Power Connections
CAUTION: Label all wires prior to disconnection
when servicing controls. Wiring errors can cause
improper and dangerous operation! Verify proper
operation after servicing.
The electrical connections to this boiler must be made
in accordance with all applicable local codes and the
latest revision of the National Electrical Code, ANSI/
NFPA-70. Installation should also conform with CSA
C22.1 Canadian Electrical Code Part I if installed in
Canada. Install a separate circuit properly rated for the
boiler. A shut-off switch should be located at the boiler.
The boiler must be grounded in accordance with the
authority having jurisdiction, or if none, the latest revision
of the National Electrical Code, ANSI/NFPA-70.