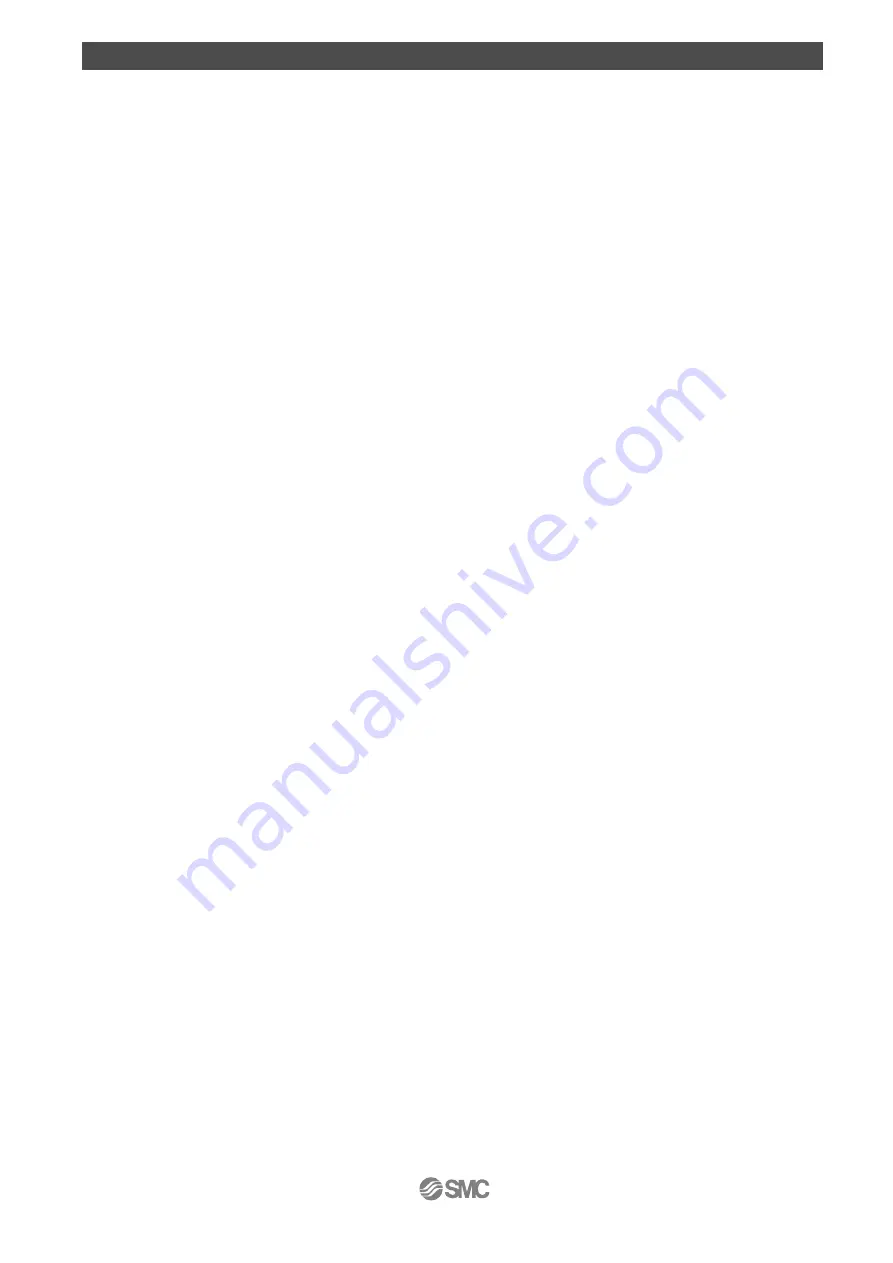
-1-
Contents
Safety Instructions ..................................................... 2
1. How to Operate ....................................................... 5
1.1 Outline ....................................................................... 5
1.2 Installation and Piping .............................................. 5
1.3 Wiring of the DC plug ............................................... 6
1.4 Terminal Block .......................................................... 7
1.5 Operation Method ..................................................... 7
1.6 Operation step (with photoelectric sensor) ............ 8
1.7 Removal of side cover .............................................. 9
2. Desktop Duster Box/ ZVB Series ........................ 10
2.1 Specifications.......................................................... 10
2.2 How to Order ........................................................... 10
2.3 Construction ........................................................... 11
2.4 Dimensions ............................................................. 12
2.5 Offset Voltage and Discharge Time ....................... 13
3. Ionizer Functions .................................................. 14
3.1 Functions ................................................................. 14
4. Maintenance.......................................................... 15
4.1 Maintenance of Ionizer ........................................... 15
4.2 Valve Maintenance .................................................. 16