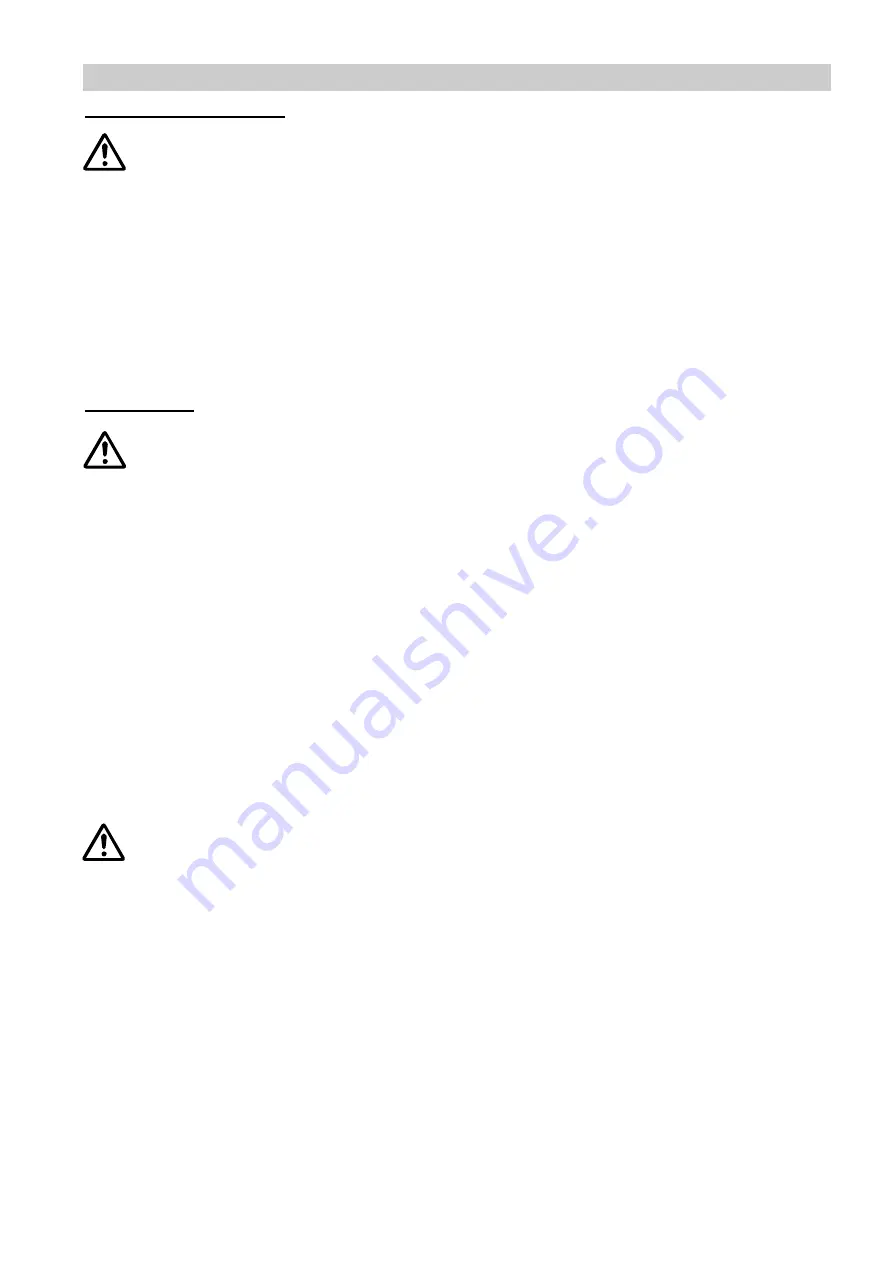
Operating Environment
①
Do not use in an atmosphere containing corrosive gases, chemicals, sea water, water, steam, or
where there is direct contact with any of these.
Refer to the construction diagram for information on the materials used in the rotary table.
②
Do not expose the product to direct sunlight for an extended period of time.
③
Do not use in a place subject to heavy vibration and/or shock.
④
Do not mount the product in locations where it is exposed to radiant heat.
⑤
Do not use in dusty locations or where water oil, etc., splash on the equipment.
Maintenance
①
Perform maintenance inspection according to the procedures indicated in the operation
manual.
If handled improperly, malfunction and damage of machinery or equipment may occur.
②
Maintenance work
If handled improperly, compressed air can be dangerous. Assembly, handling, repair and element
replacement of pneumatic systems should be performed by a knowledgeable and experienced
person.
③
Drain flushing
Remove drainage moisture from air filters regularly.
④
Removal of equipment, and supply/exhaust of compressed air
When components are removed, first confirm that measures are in place to prevent workpieces from
dropping, run-away equipment, etc. Then, cut off the supply pressure and electric power, and exhaust
all compressed air from the system using the residual pressure release function.
When machinery is restarted, proceed with caution after confirming that appropriate measures are in
p
l
ace to prevent cylinders from sudden movement.
①
For lubrication, use the designated grease for each specific product.
The use of a non-designated lubricant could damage the seals.
- 10 -
Warning
Caution
Warning