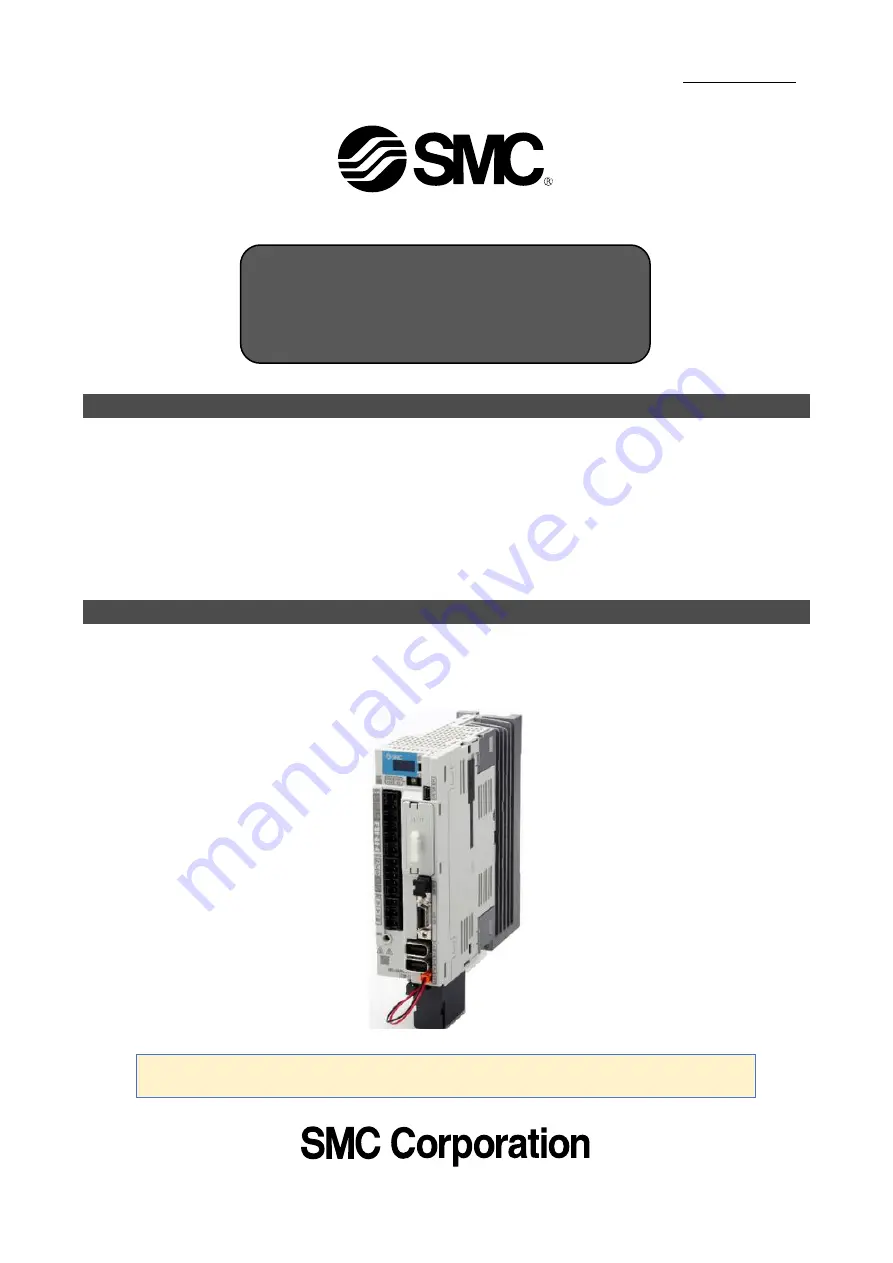
No.
DOC1020530
NN57821800
PRODUCT NAME
AC Servo Motor Driver
(
Network card type
)
MODEL / SERIES / PRODUCT NUMBER
LECSN-T
□
Series
Operation Manual
(Simplified edition)
When connecting LECSN-T with MR Configurator2
TM
, please select the model: "MR-J4-TM".
For SMC products, please contact the SMC sales office.