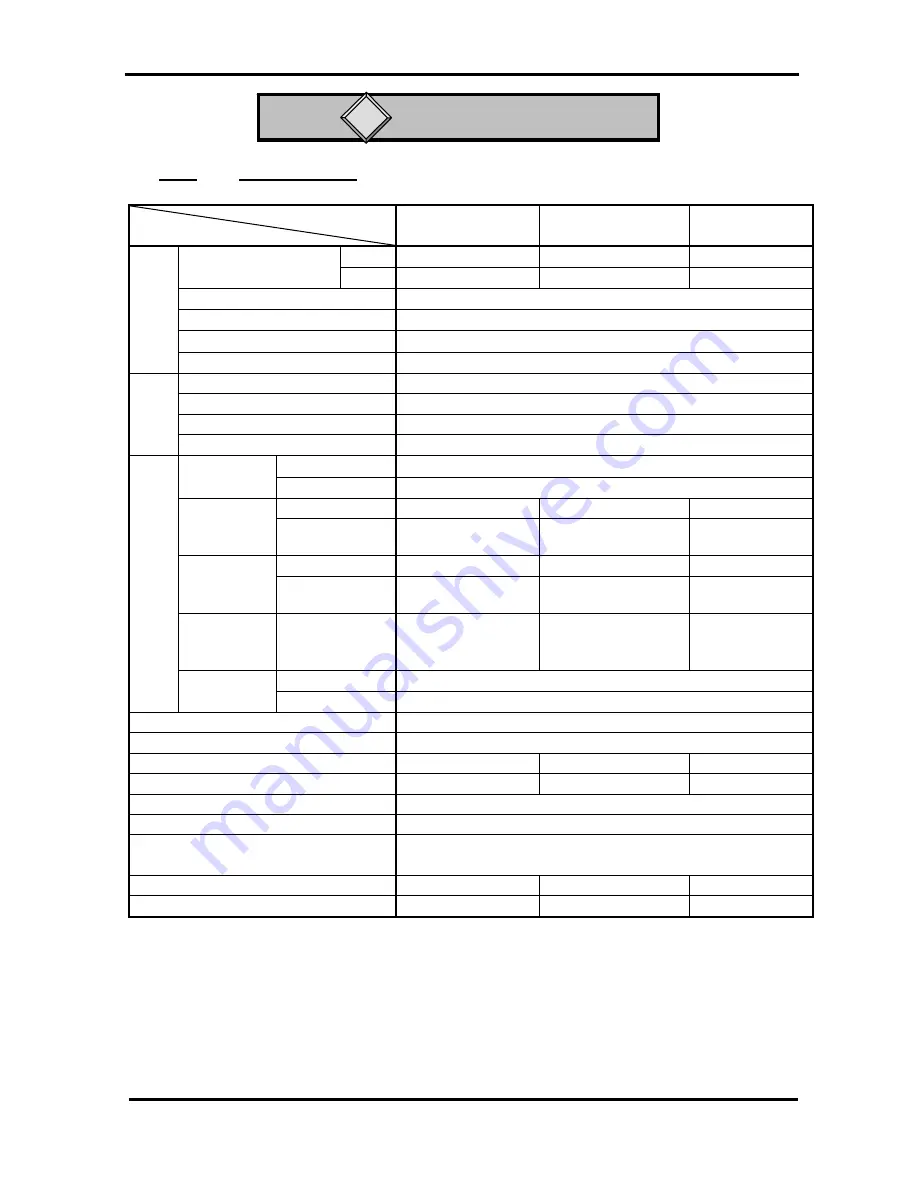
6 References
6 References
6 - 1
Specifications
Model
Specification
IDU3E IDU4E
IDU6E
50Hz 0.32
0.52
0.75
Air Flow Rate
m
3
/min (ANR)(Note 1)
60Hz 0.37
0.57
0.82
Operating Pressure
0.7MPa
Inlet Air Temperature
55
o
C
Ambient Temperature
32
o
C
R
ated C
ondition
Pressurized Dew Point
10
o
C
Working Fluid
Compressed Air
Inlet Air Temperature
5 ~ 80
o
C
Inlet Air Pressure
0.15 ~ 1.0MPa
Operati
ng
R
ange
Ambient Temperature
2 ~ 40
o
C(Relative Humidity of 85% or less)
100VAC(50/60Hz)
Single phase AC100/100
,
110V[Voltage fluctuations
±
10
%
]
Power source
200VAC(50/60Hz)
Single phase AC200/200
,
220V[Voltage fluctuations
±
10
%
]
100VAC(50/60Hz) 19/18
22/22
28/26
Starting
current
(Note 2) A
200VAC(50/60Hz) 9/8
11/10
21/20
100VAC(50/60Hz) 2.4/2.5
3.0/3.1
5.7/5.7
Operating
current
(Note 2) A
200VAC(50/60Hz) 1.2/1.3
1.5/1.5
3.4/3.0
Power
consumption
(Note 2) W
100VAC,200VAC
(50/60Hz)
180/202 208/236
385/440
100VAC 10A
Elec
trical S
pecification
Circuit Breaker
(Note 3)
200VAC 5A
Condenser
Plate fin tube type with forced air cooling
Refrigerant
R134a
(
HFC
)
Refrigerant Charge(AC100V/200V) g
200
±
5
250
±
5
260
±
5
Inlet
Outlet Rc3/8
Rc1/2
Rc3/4
Drain Connection
10mm
Painting
Melamine baking finish
Coating Color
Panel: Urbanwhite 1
Base: Urbangray 2
Weight kg
23
27
28
Applicable Compressor(Standard) kW
2.2
3.7
5.5
Note1: The data for SCFM (ANR) is referring to the conditions of 68
°
F
(
20
°
C
)
, 1atm . pressure & relative
humidity of 65%.
Note 2: The value is that of under specified condition.
Note 3: When short period power shortage (including instantly recovered shortage) is recovered, it may take
a longer starting period than usual starting or may not start due to the protective devices.
6 - 1