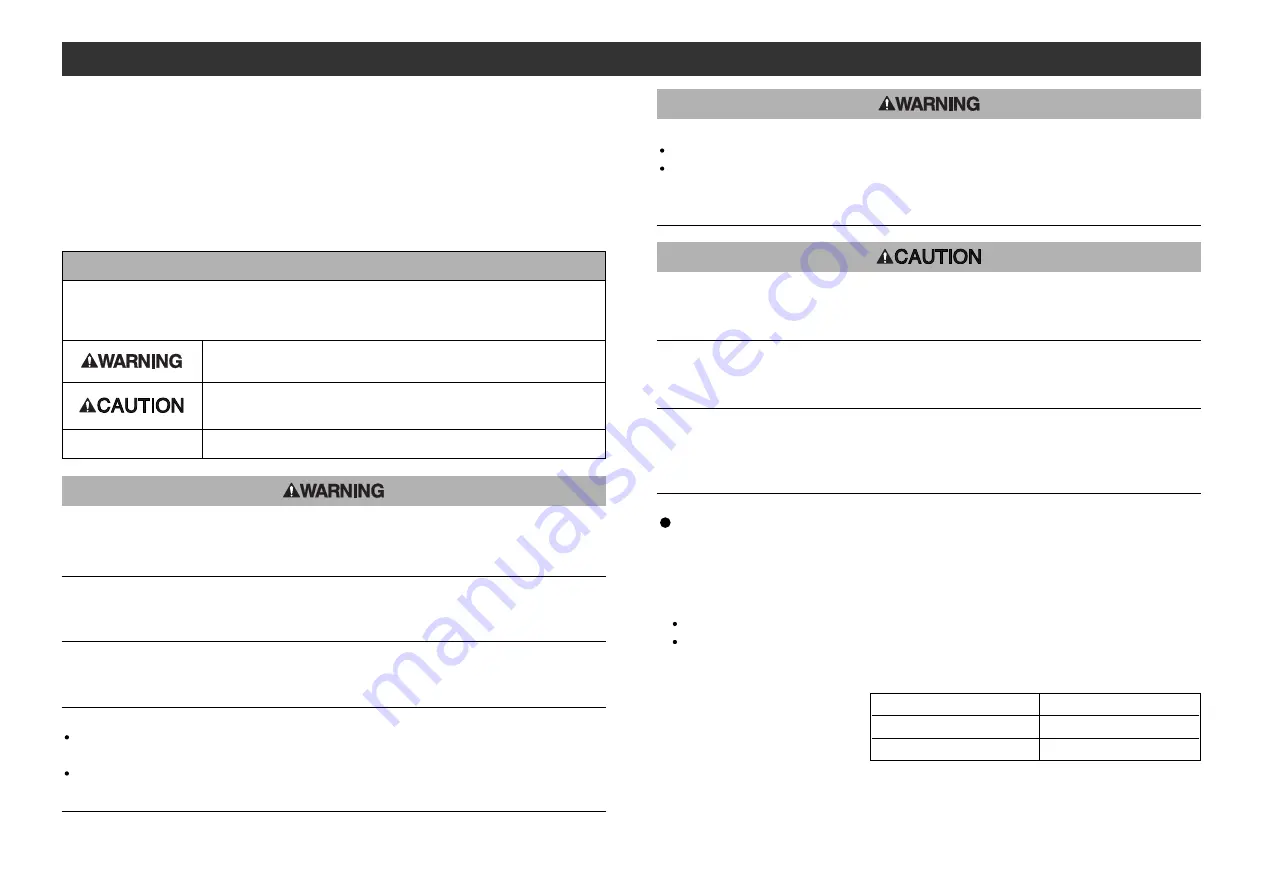
2
3
SAFETY
The body of unit and this manual contain the essential information for the protection of
users and others from possible injury and property damage and to ensure correct
handling.
Please check that you fully understand the definitions of the following messages
( symbols ) before going on to read the body of this manual, and always follow the
instructions.
Please also read the instruction manuals etc. of related machines and equipments and
understand the contents before use.
IMPORTANT MESSAGES
Indicates a potentially hazardous situation that could result in
death or severe injury if you do not follow instructions.
Read this manual and follow its instructions. Signal words such as WARNING,
CAUTION and NOTE will be followed by important safety information that must be
carefully reviewed.
Indicates a potentially hazardous situation that, if not avoided,
may result in minor injury or moderate injury.
Gives you helpful information.
NOTE
Do not disassemble,
modify ( including modification of printed circuit board ) or repair.
Otherwise injury or failure can result.
Do not operate beyond specification range.
Otherwise fire, malfunction or damage to the reduced wiring system can result.
Confirm the specifications before operation.
Do not operate in atmosphere of flammable/explosive/corrosive gas.
Otherwise fire, explosion or corrosion can result.
This reduced wiring system is not explosion-proof type.
For use in interlock circuit:
Provide double interlock system by adding different type of protection
( such as mechanical protection ).
Check that the interlock circuit is working normally.
Otherwise accident caused by malfunction can result.
Before performing maintenance:
Turn off power supply.
Stop air supply, exhaust compressed air in piping, and confirm the release to
atmosphere.
Otherwise injury can result.
Conduct proper functional inspection after completing maintenance.
In the case of abnormality such as unit does not work normally, stop the operation.
Otherwise safety cannot be assured due to unintended malfunction.
Avoid mixing of CC-Link dedicated high-performance cable and other cables (
CC-Link dedicated cable and/or Version 1.10 compatible CC-Link dedicated
cable ).
Mixing can hinder normal data transmission and cause trouble.
Provide grounding to improve safety and noise resistance of reduced wiring sys-
tem.
Provide grounding as close to the unit as possible to shorten distance for grounding.
1. UL508-compatible limited voltage/current circuit
A circuit using the secondary coil of an insulating transformer that meets following condi-
tions as power source.
Maximum voltage ( at no load ): 30Vrms ( 42.4Vpeak ) or below
Maximum current:
( 1 ) 8A or less ( including when short-circuited )
( 2 ) When limited by the circuit protector ( such as fuse )
having the following rating.
2. UL1310-compatible Class 2 power supply unit or circuit of max. 30Vrms ( 42.4Vpeak ) or
less using a UL1585-compatible Class 2 transformer as power source. ( Class 2 circuit )
No-Load Voltage ( Vpeak )
Max. Current Rating ( A )
0 to 20 [V]
5.0
Above 20 [V] to 30 [V]
100/peak voltage
Handling precautions
Use the following UL-recognized DC power supply to combine with.