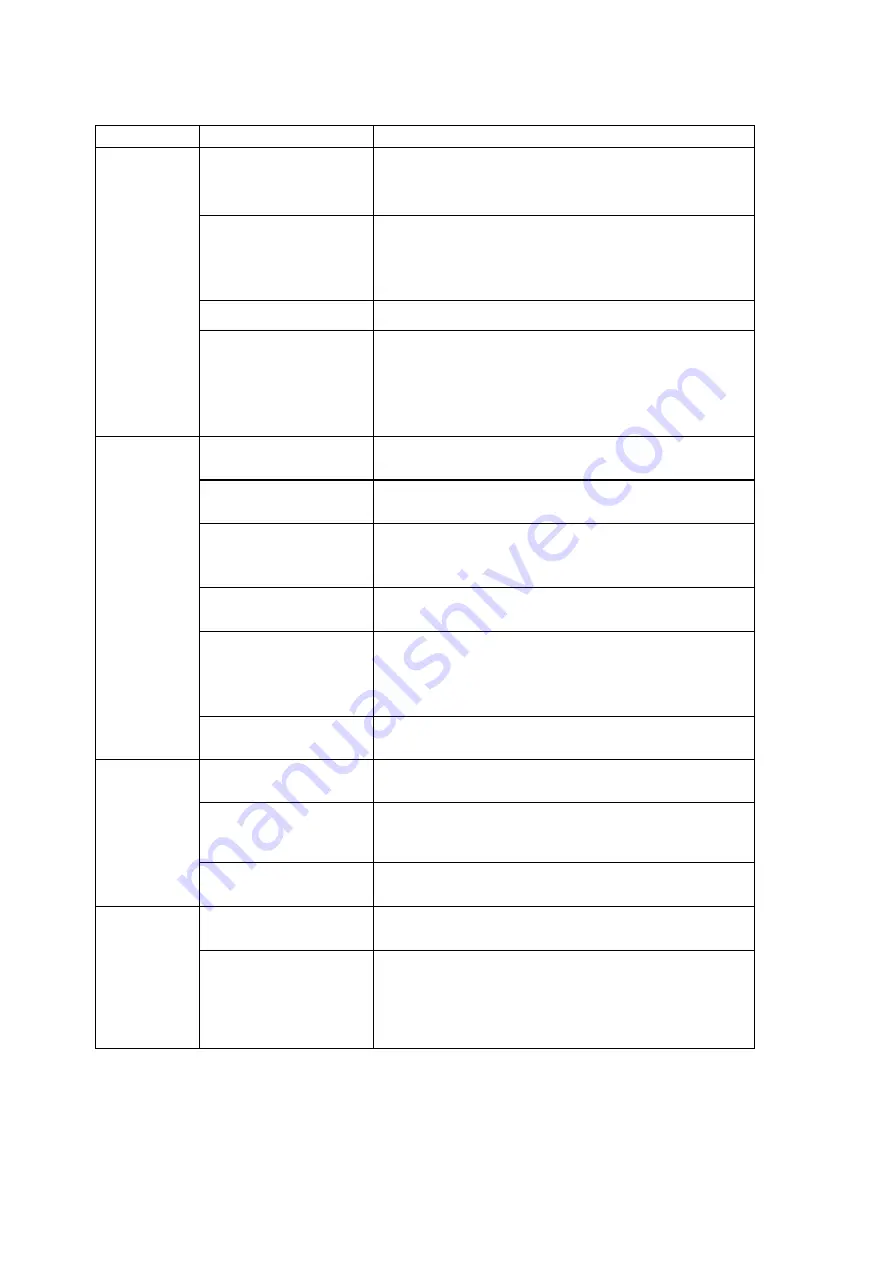
- 26 -
5. Troubleshooting
Table 12. Troubleshooting
Failure Main
cause
Action
1. Improper lubrication
●
Disassemble and apply applicable grease (lithium
soap group grease JIS #2 equivalent such as
“IDEMITSU DOUGHNY CORONEX GREASE #2”)
2. Rod deformation
●
Rod deformation is caused by offset load, side load,
over load, abnormal displacement of mounting
position, etc. Replace the piston rod assembly and
correct the abnormal load, position, etc.
3. Insufficient air pressure
●
Supply appropriate pressure.
1. Operation
is not
smooth.
4. Too slow operation
●
Even slight changes in the external conditions may
affect the speed in low speed operation. In such
case, please consider using air hydro or hydro
checker.
●
Change the cylinder to one with a larger bore size.
1. Abrasion and
damage to piston seal
●
Replace the seal.
2. Reduction in air
pressure
●
Check the pressure and the capacity of the pressure
source.
3. Insufficient air flow
●
Resistance in the passage might have increased
due to deformation of air flow passage or foreign
matter in the air. Repair and clean it.
4. Improper mounting
position of cylinder
●
Mount the cylinder in the proper position.
5. Deformation of
cylinder moving part
●
Cylinder is deformed by abnormal load, which
increases sliding resistance. Overhaul should be
performed and the piston rod assembly should be
replaced.
2. Output is
decreasing.
6. Improper lubrication
●
Refer to “Operation is not smooth” above .
1. Speed controller is
not used.
●
Use a speed controller which is suitable for the
cylinder size.
2. Lack of fine
adjustment of the
speed controller
●
Select a speed controller adequate to secure the
required operating speed by referring to the flow
characteristics curves.
3. Piston
operates too
fast.
3. Meter-in speed
controller is used.
●
To obtain stable speed even if load fluctuates, use a
meter-out speed controller.
1. Directional control
valve size is too small.
●
Use larger valve.
4. Piston
operates too
slowly.
2. Piping resistance is
too large.
●
Use appropriate size valve and other equipment.
Pay careful attention to the size of piping material
and fitting.
●
Use appropriate size equipment and piping on the
exhaust side.