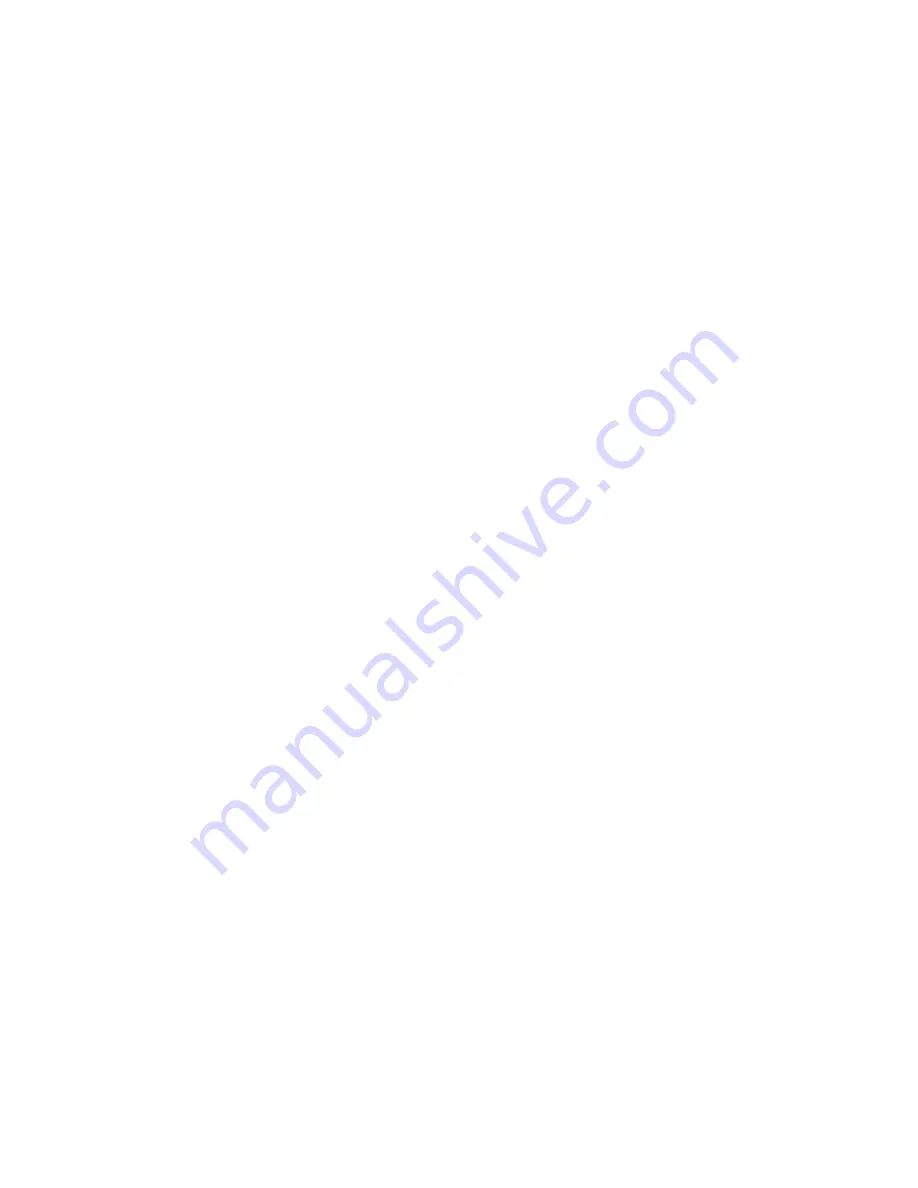
7
TROUBLESHOOTING GUIDE
Note:
BEEP sounds are emitted from the Solenoid Valve Module (not from
Faucet Spout). For the first ten (10) minutes of operation (or after battery
replacement or electrical power is reconnected), the unit BEEPS every
time the faucet is activated to indicate that the range limits are set. To
conserve battery power, the battery model will not BEEP again until it
indicates low battery power.
1. PROBLEM: Module emits audible “BEEPs” when activated.
CAUSE:
Electrical power supplied to the faucet is extremely low
(battery power is nearly exhausted or brownout electrical
conditions exist).
SOLUTION:
Reconnect electrical power.
To ensure proper operation, insert four (4) new C-size
Alkaline batteries. Check that the orientation of each
battery matches the positive (+) and negative (-)
symbols shown at the bottom of the Battery
Compartment. Reinstall Battery Compartment.
2. PROBLEM: Sensor is activated but faucet does not deliver water.
INDICATOR:
Module DOES NOT produce audible “BEEPs.”
CAUSE:
No electrical power is supplied to the faucet (battery
power is fully exhausted or blackout electrical conditions
exist).
SOLUTION:
Replace or reconnect electrical power supply.
To ensure proper operation, insert four (4) new C-size
Alkaline batteries. Check that the orientation of each
battery matches the positive (+) and negative (-)
symbols shown at the bottom of the Battery
Compartment. Reinstall Battery Compartment.
CAUSE:
Electrical power supply is not properly connected
(Batteries or Battery Compartment is not installed
properly).
SOLUTION:
Check that the orientation of the batteries match the
positive (+) and negative (-) symbols shown at the
bottom of the Battery Compartment. Reinstall the Battery
Compartment.
CAUSE:
Solenoid Valve Module is defective.
SOLUTION:
Replace EBF-11-A Solenoid Valve Module.
INDICATOR:
Module produces audible “BEEPs” when all electrical
connections are made and after 30-second calibration
procedure, but NOT when a target is placed in the
detection zone of the Sensor.
CAUSE:
Fiber Optic Cable is not connected correctly to Solenoid
Valve Module or was not connected when proper
electrical connections were made.
SOLUTION:
Reconnect Fiber Optic Cable to Solenoid Valve Module.
Unscrew Coupling Ring to open Battery Compartment
and reset the electrical system. Reattach the Battery
Compartment to the Valve Module. Tighten Coupling
Ring.
CAUSE:
Fiber Optic Cable is defective.
SOLUTION:
Replace EBF-1009-A Sensor Cable, or the Faucet/Sensor
Assembly listed below.
For an EBF-85 model:
Replace EBF-10-A Faucet/Sensor
Assembly.
For an EBF-187 model:
Replace EBF-170-A
Faucet/Sensor Assembly.
CAUSE:
Solenoid Valve Module is defective.
SOLUTION:
Replace Solenoid Valve Module.
Replace EBF-11-A Solenoid Valve Module.
INDICATOR:
Module produces audible “BEEPs” when a target is
placed in the detection zone of the Sensor and
Solenoid Valve produces an audible “CLICK,” but NO
water flows.
CAUSE:
Water supply to faucet is not open.
SOLUTION:
Open supply stop(s) completely.
CAUSE:
Bak-Chek
®
is installed backward.
SOLUTION:
Reinstall Bak-Chek
®
properly.
CAUSE:
Solenoid Filter is clogged.
SOLUTION:
Remove, clean, and reinsert. Replace with EBF-1004-A
Solenoid Filter Kit if necessary.
CAUSE:
Aerator or Spray Head is clogged.
SOLUTION:
Remove, clean, and reinsert.
INDICATOR:
Module produces audible “BEEPs” when a target is
placed in the detection zone of the Sensor, but Solenoid
Valve does NOT produce an audible “CLICK,” and NO
water flows.
CAUSE:
Solenoid Valve Module is defective.
SOLUTION:
Replace EBF-11-A Solenoid Valve Module.
3. PROBLEM: Faucet delivers only a slow flow or dribble when
Sensor is activated.
CAUSE:
Water Supply Stop(s) are partially closed.
SOLUTION:
Open the Supply Stop(s) completely.
CAUSE:
Solenoid Filter is clogged.
SOLUTION:
Remove, clean, and reinsert. Replace with EBF-1004-A
Solenoid Filter if necessary.
CAUSE:
Aerator or Spray Head is clogged.
SOLUTION:
Remove, clean, and reinsert.
4. PROBLEM: Faucet does not stop delivering water or continues to
drip after user is no longer detected (automatic shut-
off fails even when batteries are removed).
CAUSE:
Solenoid Valve is connected backward.
SOLUTION:
Disassemble Solenoid Valve compression fittings at the
inlet and outlet positions. Water should flow from inlet
through the Solenoid Valve to outlet according to the
direction shown by the arrow on the side of the Solenoid
Valve. Reconnect the fittings in the correct orientation.
CAUSE:
Solenoid Valve seat is dirty.
SOLUTION:
Remove, clean, and reinsert Solenoid Filter. Activate
faucet several times to flush out dirt.
CAUSE:
Solenoid Valve is dirty.
SOLUTION:
Backflush by reversing water flow (opposite to the
direction shown by the arrow on the side of the Solenoid
Valve) through the Solenoid Valve. Reconnect the
compression fittings in the correct orientation. Activate
faucet.
CAUSE:
Solenoid Valve Module is defective.
SOLUTION:
Replace EBF-11-A Solenoid Valve Module.
5. PROBLEM: The water temperature is too hot or too cold on a
faucet connected to hot and cold supply lines with
Bak-Chek
®
.
CAUSE:
Supply Stops are not adjusted properly.
SOLUTION:
Adjust Supply Stops.
CAUSE:
Bak-Chek
®
is installed backward.
SOLUTION:
Reinstall Bak-Chek
®
correctly.
NOTE:
For some systems, a thermostatic mixing valve may be
required.
For additional information about Sloan Mixing Valves or Trim Plates,
consult our Installation Instructions and Maintenance Guides.
If further assistance is required, please contact the Sloan Valve Company Installation Engineering Department at 1-888-SLOAN-14 (1-888-756-2614)