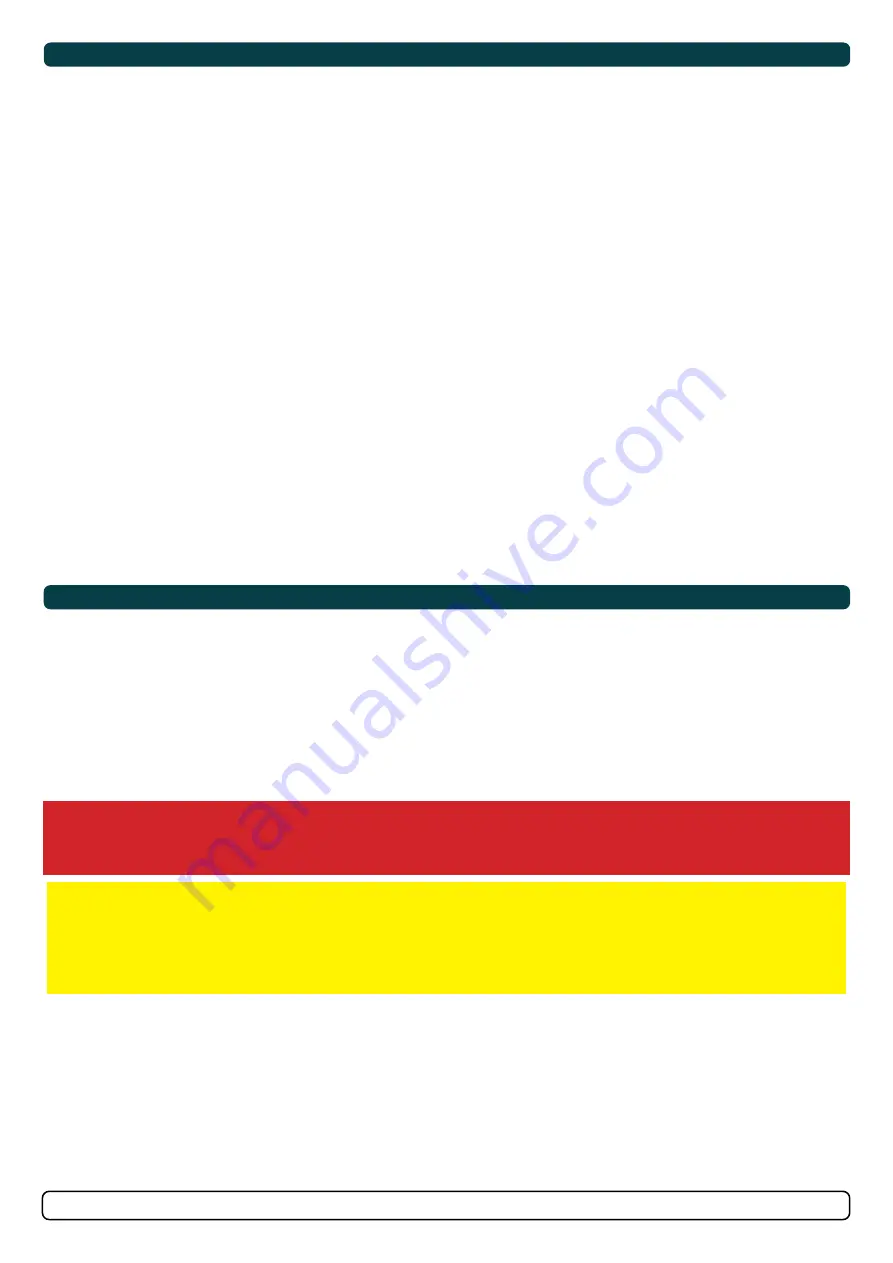
9
5926
19
2021
-
SXP35 & SXP50
MC_0072
Stern Thruster Cowls/ Grids
Installing a stern thruster cowl for stern thrusters that will allow installations in boats with shallow drafts or due to other obstructions on the stern.
These can include obstacles such as trim tabs, jets or surface drive propeller systems where shallow installation of a stern thruster is the only option.
Cowls:
Designed to aid in water redirection and reduce air entering the tunnel in shallow installations.
Grid’s:
Designed to protect the thruster from objects while in use.
MG_0017
Shallow installation
Cowl water flow redirection
An angled edge further
preventing air attraction into
the tunnel
Composite material with smooth
inner walls for optimal water flow
and strength
A standard Sidepower stern
thruster tunnel with add-on cowls
for shallow installation
cowls to change the
water flow direction to
avoid obstructions on
the stern
cowls help prevent air
from the water surface
entering the tunnel in
shallow installations
Radius corners prevent
turbulence
Easy installation for easy
bolt-on fitting
A
B
C
D
IMPORTANT
Angled cowls out of horizontal, must be
installed deeper to avoid air entry in the
thruster tunnel
Model #
90126
90080
90077
90136
90130
90220
90560
A (mm/ in)
528/ 20.8
681/ 26.6
823/ 32.4
850/ 33.5
1010/ 39.75
1208/ 47.6
1580/ 62.2
B (mm/ in)
166/ 6.5
172/ 6.8
243/ 9.6
260/ 10.2
330/ 13
393/ 15.5
515/ 20.3
C (mm/ in)
130/ 5.1
240/ 9.4
D (mm/ i n)
170/ 6.7
256/ 10.1
256/ 10.1
288/ 11.3
340/ 13.4
419/ 16.5
540/ 21.3
IMPORTANT
Install the cowls/ grids before mounting the tunnel to the SX thruster.
100mm
177mm
537mm
174mm
MC_0071
Installation Considerations and Precautions
• Do not install the thruster in a position where you need to cut a stiffener/ stringer/ support for the hull integrity without checking with the boat
builder this can be done safely.
• Contacts/ plugs or other joints in the control cables must be mounted so they remain dry at all times.
• We advise painting the gear house and propellers with anti-fouling.
(NB: Do not paint the sealing/ rubber fi ttings or propeller shafts.)
• Do not fi nish the inside of the tunnel with a layer of gel-coat/ topcoat or similar. There is only room for a thin coat of primer and two layers of anti-
fouling between the tunnel and the propellers.
• Keep installation within advised measurements. The entire surface is hard coated seawater resistant aluminium. Do not damage/penetrate the coat.
• The external stern thruster assembly and controller unit are ignition protected and can be installed in areas with the chance of explosive gases in
accordance to ISO 8846 and ABYC c1500. (Certifi cation pending)
• Ensure that the external stern thruster assembly does not disturb the water flow under the hull. At higher speeds, if the thruster is installed to
low it can cause damage to the thruster and/ or add additional drag and unwanted water splashing.
• The recommended minimum tunnel depth from the water surface is 140mm (5,51‘) to the centre of tunnel diameter. Place the Thruster as deep as
possible for better performance and reduced noise.
• When installing the thruster ensure it does not foul existing equipment inside the boat like motor bedding etc.
• If able ensure that stern-drives/ trim-tabs do not interfere with the water flow from the thruster as this can reduce the thrust effectiveness
considerably. We recommend the use of our Sleipner cowls to enhance the performance and allow installation in shallow draft boats. Sleipner
cowls will also minimise the effect if stern-drives/ trim-tabs obstruct the thruster.
• Ensure there is enough space both inside and outside the transom of the boat and the thruster does not get in conflict with existing equipment
inside the boat like steerage links etc.
(NB: It is possible to mount the tunnel offset from the boat’s centre line if necessary.)
• Heat protection cut off is calculated from the thruster motor. To avoid cable overheating do not install place the volt cables from the thruster to the
control box near any heat sources.
MC_0257
Thruster Installation Considerations and Precautions
Before installation, it is important that the installer reads this guide to ensure necessary acquaintance with this product.
• The electro motor must be handled with care. Do not lift it by internal cable connections, main terminals or placed down on the drive shaft.
• The thruster power supply circuit must include the recommended sized fuse and a battery isolation switch.
• Never run the thruster out of water.
• It is important to follow the guidelines in this manual. Failure can result in severe damage to the thruster.
MC_0267
NEVER
Disassemble any part of the Ignition Protected stern thruster assembly. Tampering with the Ignition Protected stern thruster assembly or any attempt
to disassemble anything on this thruster assembly inside the boat can cause an explosion with severe consequences. If there is a problem with your
Ignition Protected stern thruster, please contact your dealer.
IMPORTANT NOTICE S-LINK™ SYSTEM
When installing an S-Link™ system DO NOT connect any other control equipment directly to the S-Link™ bus except original Sleipner S-Link™
products. Connecting third-party equipment must always be connected through a Sleipner-supplied interface product. Any attempt to directly
control or connect into the S-Link™ control system without a designated or approved interface will render all warranties and responsibilities
of all connected Sleipner products. If you are interfacing the S-Link™ bus by agreement with Sleipner through a designated Sleipner supplied
interface, you are required to install at least one original Sleipner control panel to enable efficient troubleshooting if necessary.
MC_0265