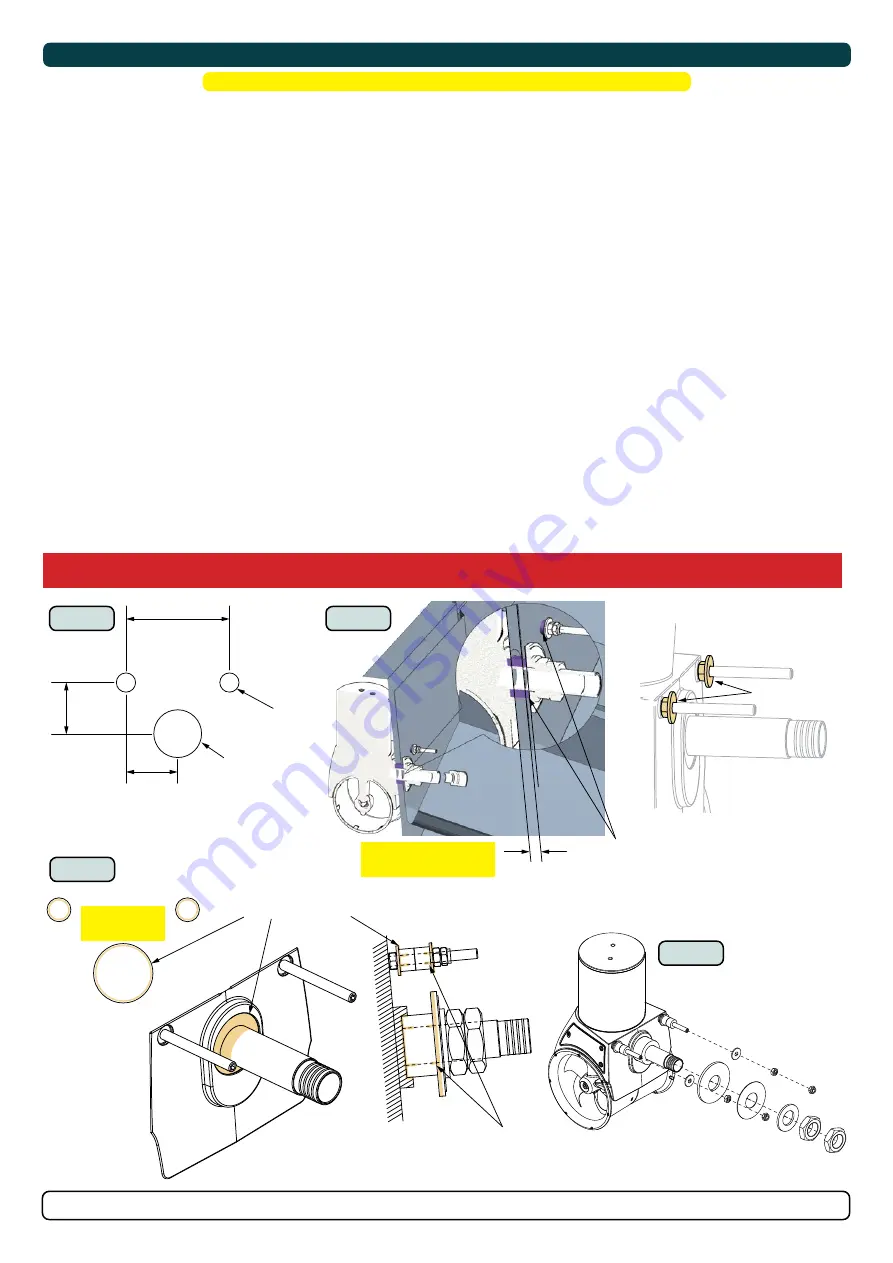
13
5926
19
2021
-
SXP35 & SXP50
SX Spacer
Follow the installation of the SX thruster in the
Motor Installation
to step 3
.
see next page
1. Defi ne the location to install the thruster.
(NB: Ensure the thruster does not protrude past the transom profi le on any side and there is no
obstruction to the thrusters water flow. Also, check internally the thruster will not obstruct any objects.)
2. Mark the locations of the three drill holes using the defi ned measurements in this manual or from a template.
(NB: Maximum hull thickness is
50mm including optional spacer or 150mm for extended hull thickness models.)
3. Drill main hole, then two support bolt holes. Clean the area from dust for installation of the thruster.
(NB: Hull holes must be drilled fi rst before
attaching the spacer as the top support holes are larger than the spacers.)
---------
4. Drill out the two support bolt holes in the spacer.
5. Apply MS Polymer sealant or equal to the back surface face of the spacer.
6. Place the spacer to the hull.
Continue the installation of the SX thruster from step 4 in the
Motor Installation.
MC_0074
!
Please refer to the graphic for special considerations relating to your model
!
IMPORTANT
If using the 50mm spacer ensure you have the extended tube SX model.
MG_0262
Hull
Hull
12mm
Spacer
Apply MS Polymer sealant or
equal to back surface face
50mm
Spacer
Drill
8.5 / 9 mm
Drill
8.5 / 9 mm
4
6
5
IMPORTANT
The spacer and hull have different hole
diameters for the support bolts. This is to
allow the compression rings to be inserted
into the hull only.
The spacer and hull for the main tube have
the same hole diameter so compression
rings can be inserted for the total length of
the hole.
Compression
ring
Compression
ring
MG_0113
130 mm
5,12”
65 mm
2,56”
35,80 mm
1,41”
50 mm
1,97”
Drill holes in hull
Hole size
for hull
Sealant (MS Polymer)
Thruster and attachment bolts
18 mm
0,71”
All rings need
+10% compression
All rings need
+10% compression
Bolt and Washer
Hull thickness
Maximum hull thickness
is 50 mm or 150mm
Cover the
entire surface
1 - 3
6
7 - 8
4 - 5
Motor Installation
1. Defi ne the location to install the thruster.
(NB: Ensure the thruster does not protrude past the transom profi le on any side and there is no
obstruction to the thrusters water flow. Also, check internally the thruster will not obstruct any objects. Ensure cables internally do not obstruct
any objects. Do not place cables or control box close to high heat radiating parts EG. Turbo/ exhaust manifolds etc.)
2. Mark the locations of the three drill holes using the defi ned measurements in this manual or from a template.
(NB: Maximum hull thickness is
50mm including optional spacer or 150mm for extended hull thickness models.)
3. Drill main hole, then two support bolt holes. Clean the area from dust for installation of the thruster.
4. Install a bolt and washer to ensure top bolts contact surface area is level with the main tube. Temporally place the thruster through the holes to
ensure correct fi tting. Using the cable leads from the thruster defi ne the location within the vessel for the installation of the control box.
(NB: If
using a spacer the support bolt and washer are not required.)
5. Check the length of the compression rings. Compression rings must be longer than hull thickness to allow for compression
(NB: Cut compression
sealants to length top achieve 10% compression.)
6. The thruster assembly must sit flush on the transom. Grind and sand the area if required to ensure a secure fi t.
(NB: Use caution when grinding/
sanding surfaces as to not remove too much fi breglass.)
7. Ensure both bolts and washers to the support bars on the thruster are attached.
Apply a sealant (MS Polymer) to:
- the inside surface of the cut-out holes on the hull.
-To the surface of the washer to the thread and
- in the recess of the main tube to the thread.
- 1cm deep inside all compression ring.
place all compression rings to bolt threads.
(NB: Ensure ample sealant (MS Polymer) around the bolts and centre tube for a watertight fi tting.)
8. Insert the thruster with compression rings into the hole.
9. Fasten the thruster
MC_0074
!
Please refer to the graphic for special considerations relating to your model
!
For installations in high corrosive environments (saltwater) the exposed aluminium parts of the thruster must be coated with an epoxy primer
before antifouling or/and use.