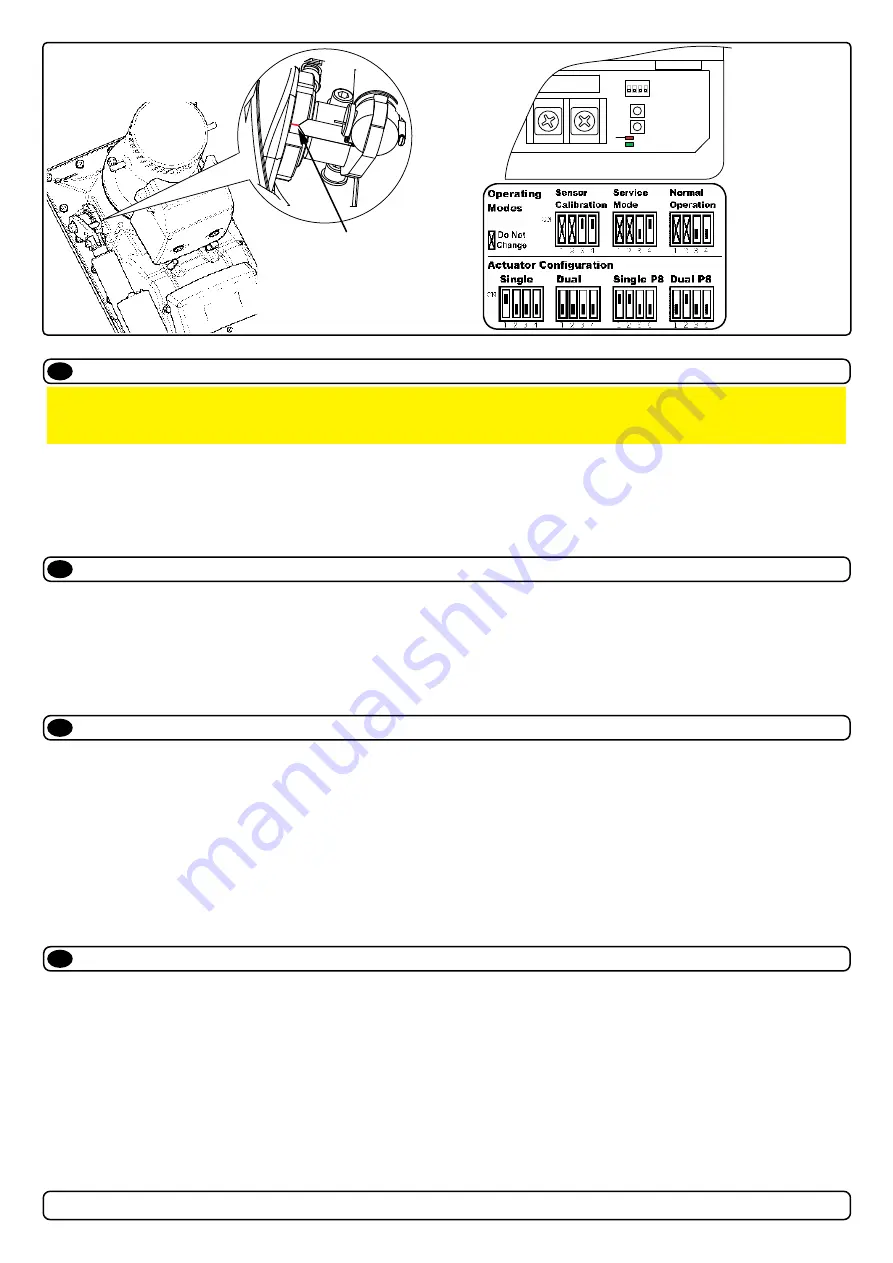
22
5927
7
2021
-
SRP 300
MG_0063
GASKET
4x SCREWS
58 mm
67 mm
125 mm
116 mm
132.7 mm
75.7 mm
Ø 4.5 mm
Ø 4.5 mm
Ø 4.5 mm
Ø 4.5 mm
(S-link)
External alarm buzzer
12V / 24V DC - max 0,5A
External alarm / buzzer connection
Supply
+ 12V / 24V DC
-
+
Ø 4.5 mm
Rear
side
of pa
nel
Internal
fuse / relay
MG_0108
Align pointer on lever
arm with red mark on
bearing
Actuator arm and bearing
Controller
SETTINGS
UP
DOWN
FAULT
STATUS
(FUSE)
ON
1 2 3 4
MC_0069
MC_0069
MC_0069
MC_0069
Check drive shaft alignment
Calibrate drive shaft alignment
Actuator Confi guration
LED Indication
EN
EN
EN
EN
1) Connect power to thruster and S-link system.
2) Sett DIP-switch on the controller to 0000.
3) Turn on the panel. (The drive shaft deploys.)
4) The actuator lever arm and the bearing are set to alignment marking
5) If marks align, turn panel off. Drive shaft retracts.
6) If the marks do not align, proceed to calibrate drive shaft.
(NB: The drive shaft is correctly aligned when manufactured)
1) With dip-switches select ‘Service Mode’.
2) Align the arrow on the actuator arm with the calibration mark, using the UP/DOWN buttons.
3) With dip-switches select ‘Sensor Calibration Mode’.
4) Press and hold both UP and DOWN buttons until STATUS LED light up green.
(NB: If FAULT LED light-up red, then the calibration is out of position (wrong align mark).
5) With dip-switches select ‘Operation Mode’, thruster retracts.
Dip-switch number 1 & 2 confi gures the actuator(s).
No.1 set to OFF when the retract has two actuators.
No.1 set to ON when the retract only has one actuator.
No.2 set to OFF when the retract does not have P8 type actuator(s).
No.2 set to ON when the retract has the P8 type actuator(s).
If dip-switch no.2 is set to ON and the actuator gives a rattling noise when the door closes, then there probably is not P8 actuator(s) and dip-switch
no.2 needs to be set to OFF.
The actuator is a P8 type:
-If the actuator has a plastic cap at the back where you can adjust the actuator manually.
-If it is marked with a sticker with P8
-If the manufacturer label says P8
Continuous red light:
Motor over-temp, Controller over-temp, Controller no communication, Motor relay failure, Low battery voltage, Position sensor failure, No
power to actuators, Retractable unit failure, Temp sensor open circuit.
Flashing red light:
Red light fast blinking: Dip-switch in an invalid position.
Red light short flash every 2 seconds: Shaft not calibrated, or shaft calibrated out of range.
Continuous green light:
Normal mode, Service mode (actuators operated by UP/DOWN buttons).
Re-calibrated “down”-position.
Flashing green light:
No S-Link communication.
IMPORTANT
Before the thruster motor is operated, check the drive shaft alignment is completely straight when it reaches the end position form the control
panel operation: