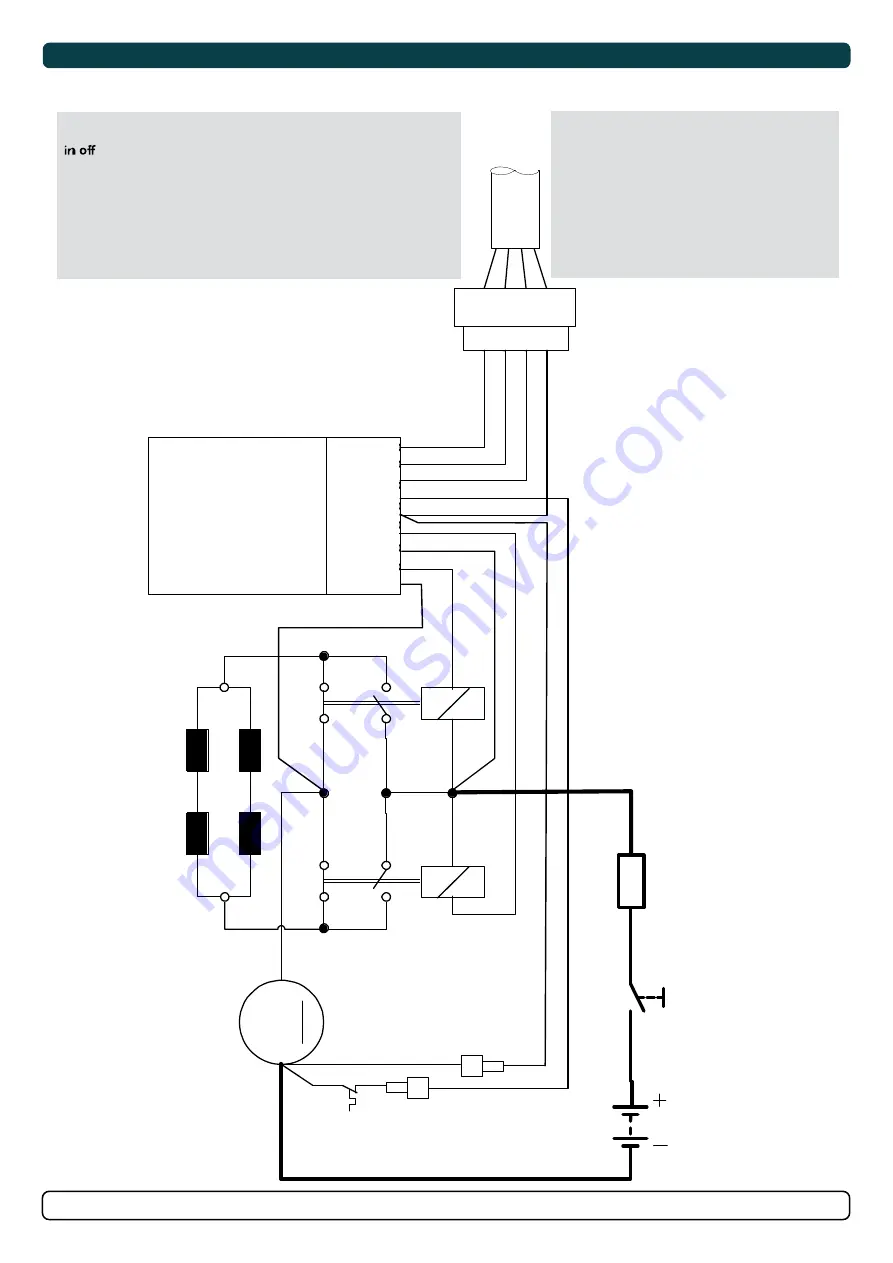
19
2653
11
2021
-
SE IP 100 & SE IP 130
Electrical Specifi cations
MC_0044
*V
alid for DC motors
Model Size
System Voltage
Nominal current
draw
Min. battery
CCA
Rec. fuse
<7m total + & -
7-14m total + & -
15-21m total + & -
22-28m total + & -
28-35m total + & -
36-45m total + & -
Min.
Rec.
Min.
Rec.
Min.
Rec.
Min.
Rec.
Min.
Rec.
Min.
Rec.
*20/1
10S
12 V
150 A
DIN: 200 SAE: 380 EN: 330
ANL
150
mm2
25
35
35
50
50
70
70
95
95
95
120
2 x 70
AW
G
3
2
2
1/0
1/0
2/0
2/0
3/0
3/0
3/0
2 x 4/0
2 x 2/0
*25/1
10S
12 V
200 A
DIN: 200 SAE: 380 EN: 330
ANL
150
mm2
25
35
50
50
70
70
95
95
120
120
2 x 70
2 x 70
AW
G
3
2
1/0
1/0
2/0
2/0
3/0
3/0
4/0
4/0
2 x 2/0
2 x 2/0
*30/125S *30/140
12 V
245 A
DIN: 200 SAE: 380 EN: 330
ANL
150
mm2
35
50
50
70
70
95
95
120
120
2 x 70
2 x 70
2 x 95
AW
G
2
1/0
1/0
2/0
2/0
3/0
3/0
4/0
4/0
2 x 2/0
2 x 2/0
2 x 3/0
*40/125S *40/140
12 V
315 A
DIN: 300 SAE: 570 EN: 520
ANL
250
mm2
35
50
70
95
95
120
120
2 x 70
2 x 95
2 x 95
2 x 120
2x 120
AW
G
2
1/0
2/0
3/0
3/0
4/0
4/0
2 x 2/0
2 x 3/0
2 x 3/0
2 x 4/0
2 x 4/0
*50/140S
12 V
370 A
DIN: 350 SAE: 665 EN: 600
ANL
325
mm2
50
50
70
95
120
2 x 70
2 x 70
2 x 95
2 x 95
2 x 120
2 x 120
2 x 120
AW
G
1/0
1/0
2/0
3/0
4/0
2 x 2/0
2 x 2/0
2 x 3/0
2 x 3/0
2 x 4/0
2 x 4/0
2 x 4/0
24 V
170 A
DIN: 175 SAE :332 EN: 280
ANL
150
mm2
25
25
25
35
35
50
35
50
50
70
70
70
AW
G
3
3
3
2
2
1/0
2
1/0
1/0
2/0
2/0
2/0
*60/185S *60/140
12 V
370 A
DIN: 350 SAE: 665 EN: 600
ANL
325
mm2
50
50
70
95
120
2 x 70
2 x 70
2 x 95
2 x 95
2 x 120
2 x 120
2 x 120
AW
G
1/0
1/0
2/0
3/0
4/0
2 x 2/0
2 x 2/0
2 x 3/0
2 x 3/0
2 x 4/0
2 x 4/0
2 x 4/0
24 V
170 A
DIN: 175 SAE: 332 EN: 280
ANL
150
mm2
25
25
25
35
35
50
35
50
50
70
70
70
AW
G
3
3
3
2
2
1/0
2
1/0
1/0
2/0
2/0
2/0
*80/185T
12 V
530 A
DIN: 550 SAE: 1045 EN: 940
ANL
400
mm2
70
70
120
2 x 70
2 x 95
2 x 95
2 x 120
2x 120
2 x 120
NA
NA
NA
AW
G
2/0
2/0
4/0
2 x 2/0
2 x 3/0
2 x 3/0
2 x 4/0
2 x 4/0
2 x 4/0
24 V
280 A
DIN: 300 SAE:570 EN: 520
ANL
250
mm2
35
35
35
50
50
70
70
95
95
120
120
2 x 95
AW
G
2
2
2
1/0
1/0
2/0
2/0
3/0
3/0
4/0
4/0
2 x 3/0
*100/185T
12 V
740 A
DIN: 750 SAE: 1425 EN: 1320
ANL
500
mm2
95
95
2 x 70
2 x 95
2 x 120
NA
NA
NA
NA
NA
NA
NA
AW
G
3/0
3/0
2 x 2/0
2 x 3/0
2 x 4/0
24 V
340 A
DIN: 400 SAE: 760 EN: 680
ANL
325
mm2
50
50
50
70
70
95
95
120
120
2 x 95
2 x 95
2 x 120
AW
G
1/0
1/0
1/0
2/0
2/0
3/0
3/0
4/0
4/0
2 x 3/0
2 x 3/0
2 x 4/0
*120/215T
24V
420 A
DIN: 450 SAE: 855 EN: 760
ANL
325
mm2
70
70
70
70
70
95
95
120
120
2 x 70
2 x 70
2 x 95
AW
G
2/0
2/0
2/0
2/0
2/0
3/0
3/0
4/0
4/0
2 x 2/0
2 x 2/0
2 x 3/0
*130/250T
12V
800 A
DIN: 750 SAE: 760 EN: 680
ANL
500
mm2
95
95
2 x 95
2 x 95
2 x 120
2 x 120
NA
NA
NA
NA
NA
NA
AW
G
3/0
3/0
2 x 2/0
2 x 3/0
2 x 4/0
2 x 4/0
24V
350 A
DIN: 400 SAE: 760 EN: 680
ANL
325
mm2
50
50
50
70
70
95
95
120
120
2 x 70
2 x 95
2 x 95
AW
G
2
1/0
1/0
2/0
2/0
3/0
3/0
4/0
4/0
2 x 2/0
2 x 3/0
2 x 3/0
*150/215T
24V
610 A
DIN: 560 SAE: 1064 EN: 940
ANL
500
mm2
70
70
95
95
120
120
2 x 70
2 x 95
2 x 95
2 x 120
2 x 120
2 x 120
2
2/0
2/0
3/0
3/0
4/0
4/0
2 x 2/0
2 x 3/0
2 x 3/0
2 x 4/0
2 x 4/0
2 x 4/0
*170/250
24V
550 A
DIN: 560 SAE: 1064 EN: 940
ANL
400
mm2
70
70
70
95
95
120
120
2 x 95
2 x 95
2 x 95
2 x 120
2 x 120
AW
G
2/0
2/0
2/0
3/0
3/0
4/0
4/0
2 x 3/0
2 x 3/0
2 x 3/0
2 x 4/0
2 x 4/0
*210/250
24V
500 A
DIN: 560 SAE: 1330 EN: 940
ANL
400
mm2
70
70
70
95
95
120
120
2 x 70
2 x 70
2 x 95
2 x 95
2 x 120
AW
G
2/0
2/0
2/0
3/0
3/0
4/0
4/0
2 x 2/0
2 x 2/0
2 x 3/0
2 x 3/0
2 x 4/0
*250/300
24V
610-670 A
DIN: 700 SAE: 1330 EN: 1
170
ANL
500
mm2
70
70
95
120
120
2 x 95
2 x 95
2 x 95
2 x 95
2 x 120
2 x 120
2 x 120
AW
G
2/0
2/0
3/0
4/0
4/0
2 x 3/0
2 x 3/0
2 x 3/0
2 x 3/0
2 x 4/0
2 x 4/0
2 x 4/0
*300/300
24*2
400-450A
(48V)
DIN: 400 SAE: 760 EN: 680
ANL
325
mm2
50
70
50
70
70
95
95
120
120
120
140
NA
48V
AW
G
1/0
2/0
1/0
2/0
2/0
3/0
3/0
4/0
4/0
4/0
4/0
MG_0035
Technical Wiring Diagram
A2
A
1
Fu
se
re
d
gr
ey
bl
ue
bl
ac
k
gr
ey
bl
ue
br
own
re
d
6 1
23
2i
El
ect
ro
ni
c
con
tr
ol b
ox
Th
er
m
al
swi
tc
h
Ba
tt
er
y
12
V
or
24
V
Ba
tt
er
y
m
ai
n
sw
itc
h
M
4
3 2 1
3
4
2
1
8
6
9
5
re
d
re
d
bl
ac
k
7
whi
te
NB!
Make sure to not use
any electronic interface
box (delay box) older than
the 6 1232i (ex. 6 122x)
on SP75Ti, SP95Ti, and
SP125Ti.
NB!
Make sure to not use
any electronic interface
box (delay box) older than
the 6 1232i (ex. 6 122x)
NB! Very important to check the following with main-switch
position:
After all electrical connections have been completed check with an
ohm meter that there is no electrical connection between electro-
motor body and positive terminal on the motor and between the
electro motor body and the negative (A1) terminal on the motor.
If you feel unsure on how to perform this check, contact skilled
personnel for guidance.