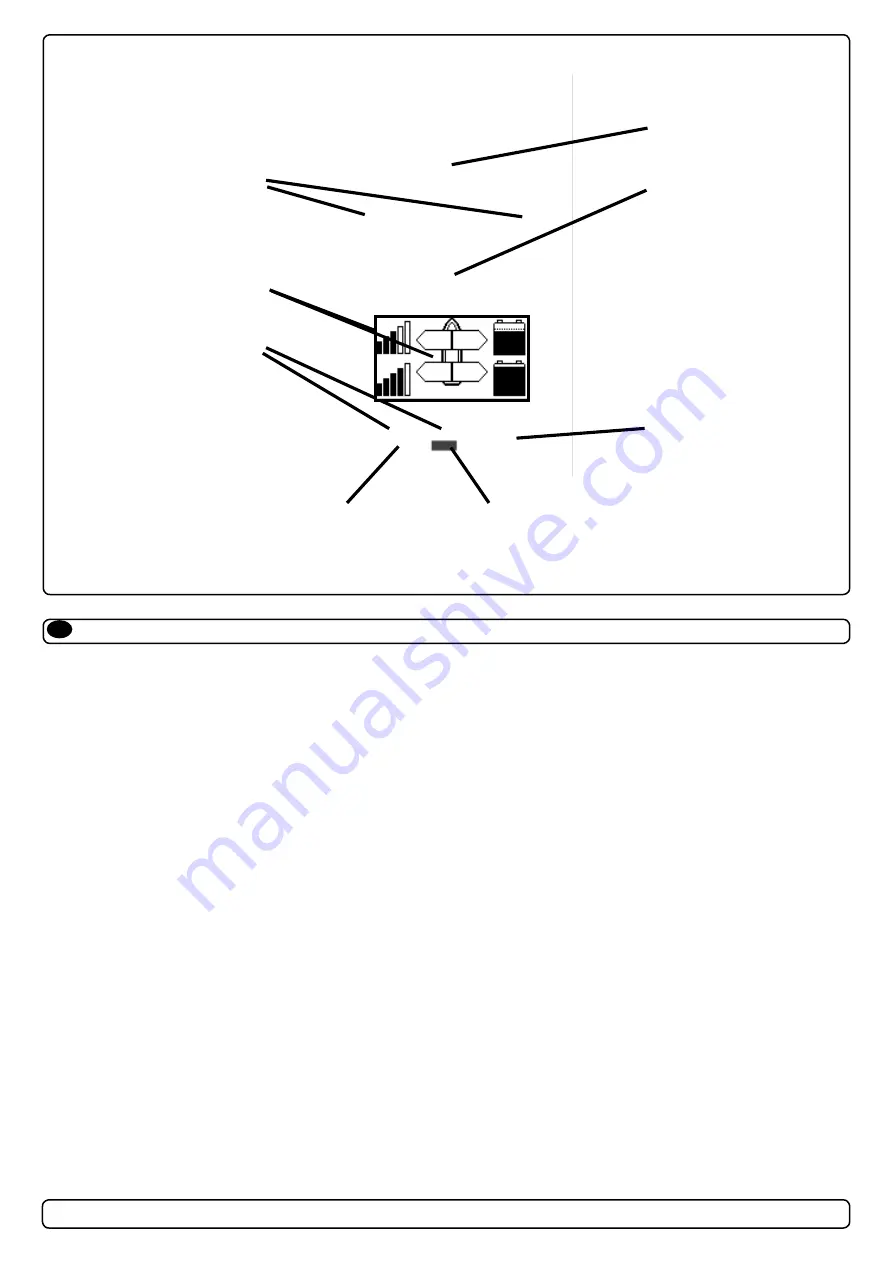
28
SRV(P)130_170_210
1.1.8 - 2017
How to use a bowthruster
1. Turn main power switch for the bow thruster on. (Always turn off
the main power switch when not on board.) A Side-Power Automatic
Main Switch will turn on/off when the panel is turned on/off.
2. Please take some time to exercise thruster usage in open water
to avoid damages to your boat.
3. Turn the control panel on by pushing both “ON” buttons on the
original Side-Power panel simultaneously.
4. Move the joystick in the direction you wish the bow
to move. Other controls like foot switches or toggle-switches on
the throttle can be used. These are connected to the S-link control
system by a S-link interface (Refer to schematics in interface manual
for installation)
5. Depending on the sideways speed of the bow, you must
disengage the control device shortly before the bow is in the
desired direction, as the boat will continue to move after stopping
the bow thruster.
How to use a single stern thruster
Some boats might however have installed a single stern thruster
because of space limitation in the bow. In this case the stern
thruster is used in the same way as a single bow thruster or moving
the boat’s stern.
How to use a bow and stern thruster combined
The combination of a bow and stern thruster offers total
manoeuvrability to the boat and the opportunity to move the bow
and the stern separately from each other. This enables you to
move the boat sideways in both directions and to turn the boat
around its own axis staying at the same place. Refer to the PCJ
control panel manual for detailed instructions.
• Again, if in doubt, try in open water first!
SIDE-POWER
THRUSTER SYSTEMS
CONFIDENCE BY CONTROL
SIDE-POWER
THRUSTER SYSTEMS
User info, PJC-212 - 1/4
TECH INFO
USER INFO
PJC-212 Control panel
PJC-212
Control panel with S-link
™
CAN-bus connection
Product features
• For proportional thruster control with the new Power Controlled DC-thrusters
• Finger tip control speed control with purpose designed joysticks
• Hold
-
function for easy docking, runs thrusters at selected power
• Back-lit
LCD
display with instant feedback
-
System status
-
Amount of thrust
&
direction of thrust
-
Thruster temperature/remaining run time
-
Battery supply voltage to thrusters
-
Monitoring of Automatic Mainswitch (informs if the fuse has blown
or the manual override is activated)
• Interactive multi-language menus
• CAN-Bus communication with thrusters and accessories
• Plug
&
play cables, waterproof and compact connectors
• System setup via “wizard”
• Diagnostics via panel/computer interface
• Built-in audible alarm “buzzer”
• Connector for external “buzzer”/loud audible alarms
S-link
Speed control joystick for
bow thuster
Speed control joystick for
stern thuster
Holding function for auto-
running of bow and stern
thrusters together in the
direction of the arrows at
selected power
Press “+” for more and
“-” for less power.
Information display, see
next page for details.
Press both “ON” buttons
simultanously to activate
control panel.
Press to change
between day and
night light
Press to access menu
system and choose
items in menus
Press to de-activate
control panel or cancel or
go back in menu system
How to use Side-Power thrusters
EN