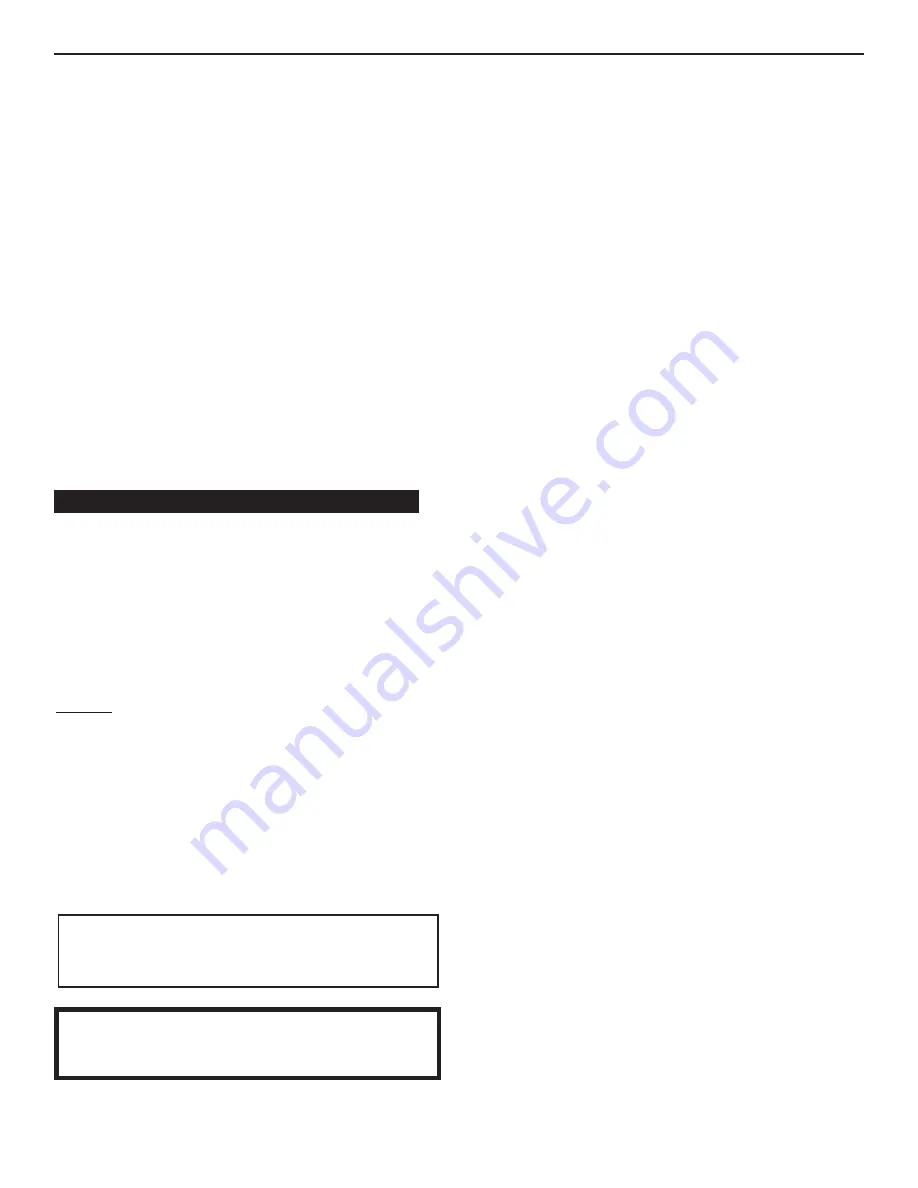
6
INTREPID TRDV
OIL SUPPLY PIPING
Install the oil tank or tanks and piping from tank to burner. Follow local
codes and practices, NFPA No. 31, INSTALLATION OF OIL BURNING
EQUIPMENT and the instruction sheet attached to the oil burner pump.
A one-pipe system should be used for gravity fed fuel systems and for lift
systems, where the total lift is less than 8 ft. Where the total lift is greater
than 8 ft., a two-pipe system must be used. In some instances, local
codes may require a two-pipe system for below grade fuel oil tanks. Be
sure to set-up the fuel oil pump for the piping system used; follow the
instructions attached to the pump. Be sure to include a good quality, low
pressure drop fuel oil filter in the supply line from the tank. This is nec-
essary, especially at low fuel oil flow rates (small nozzle sizes), to pre-
vent nozzle plugging. See Slant/Fin publication on one-pipe and two-
pipe fuel oil systems.
WIRING THE BOILER
• The wiring diagrams for the burner and boiler may be found on
pages 6-7.
• 24 volt control wiring should be approved Safety Circuit wire, protected
as needed.
• Power supply wiring to the burner must be 14 gauge or heavier, as
required, and should have a properly fused disconnect switch. 120 volt
wiring to pumps and safety controls must also be 14 gauge or heavier.
Wire must be enclosed in approved conduit.
• All wiring must be installed in compliance with the National Electric
Code, or any local or insurance codes having jurisdiction.
PRECAUTIONS BEFORE STARTING OIL BURNER
Make a positive check of A through F before starting burner:
A. Boiler and system are full of water. All air is vented from system. See
below.
B. All wiring is completed. See pages 6-7.
C. Oil supply is connected to the burner; nozzle is installed correctly; oil
valve is open at tank.
D. All combustible materials are cleared away.
E. All vent piping is properly installed and sealed.
F.
Burner settings are adjusted as per pages 8-11 and as shown on
boiler jacket label.
CAUTION:
DO NOT START THE BURNER UNLESS ALL CLEANOUT
DOORS ARE SECURED IN PLACE
STARTUP
(COMBUSTION TEST INSTRUMENTS MUST BE USED)
A. Make sure the boiler is installed and wired properly and is full of
water.
•
Start the oil burner (see burner instructions for bleeding air from oil,
etc.) IMMEDIATELY, set burner air bands to obtain a bright fire with
out smoke or oil stain.
•
All readings MUST be taken at the test port in the flue adapter.
See Figure 6 for test port location.
•
Smoke reading should be a trace or less on the smoke paper. Adjust
the burner as necessary for proper operation.
CLEANING AND FILLING A NEW WATER BOILER
I. BEFORE FILLING WATER BOILER
A.
Check burner to be certain it is ready for firing. DO NOT FIRE
into an empty boiler.
B.
Be prepared to heat raw water to at least 180°F. as soon as it is
introduced into the boiler. This procedure will remove dissolved,
corrosive gases.
C.
Provide drain line, with valve, from boiler. Use a bottom tapping.
Line and drain must be suitable for handling caustic solution.
II. CLEANING WATER BOILER SYSTEM
A.
Prepare a boil-out solution of
sodium hydroxide
(caustic soda) or
tri-sodium phosphate.
NOTE: Use caution in handling chemicals. Caustic soda is
harmful to skin, eyes and clothing.
1.
Proportions: 1 lb. of either chemical per 50 gallons of sys-
tem water.
2.
Stir chemical in water until dissolved and pour into the boiler
through a top tapping. Replace plug.
B.
Fill the entire system with water.
C.
Start the burner, using the start-up procedure.
D.
Circulate the water through the entire system.
E.
Vent the system, including the radiation.
F.
Allow boiler water to reach operating temperature, if possible.
G.
Continue to circulate the water for a few hours.
H.
Shut off the burner.
I.
With CAUTION, drain the boiler solution to a safe location. DO
NOT LEAVE SOLUTION SITTING IN SYSTEM OVER 2
HOURS.
J.
Wash the water side of the boiler thoroughly using a high pres-
sure water stream. Fill and drain the boiler several times.
III. TREATING WATER FOR CORROSION CONTROL
(This is not scale control)
A.
Prepare a solution of
sodium chromate
.
Proportions: 6 oz. per 50 gallons of system water.
B.
Stir chemical into water until dissolved and pour into the boiler
through a top tapping. Replace plug.
IV. FILLING AND VENTING THE WATER BOILER
A.
Refill the system with fresh water.
B.
Bring water temperature to at least 180° F. promptly.
C. Circulate water through entire system.
D.
Vent the system, including the radiation.
E.
The boiler is now ready to be put into service or on standby.
F.
If brand-name air-control devices are used, venting instructions
furnished with the devices should be followed.
V. SAFETY CHECK FOR CONTROL SYSTEM
High limit control test: Set thermostat high enough for boiler water
temperature to reach high limit control setting. When this tempera-
ture is reached, the high limit switch should open, and the burner
should shut off automatically. If the high limit does not operate to
shut off the burner, the high limit or the wiring is faulty. Repair or
replace immediately.
Wiring to the boiler must come through an emergency power isolation
switch with a clearly marked red switch plate. This switch should be
located so that it is apparent to the homeowner when entering the base-
ment or other boiler area. The homeowner should be made familiar with
operating the toggle to provide or stop the power to the boiler.
Note: The draft is not adjustable.
The draft should not exceed 0.35”WC
during burner operation
THE FLUE IS UNDER POSITIVE PRESSURE DURING
OPERATION. ALL VENTING MUST BE SEALED AND
CHECKED ON A REGULAR INTERVAL.
OPERATING INSTRUCTIONS
Summary of Contents for INTREPID TRDV Series
Page 4: ...4 INTREPID TRDV...
Page 9: ...INTREPID TRDV 9 Basic Module Wiring less circulator...
Page 14: ...14 INTREPID TRDV Notes...
Page 15: ...INTREPID TRDV 15 Notes...