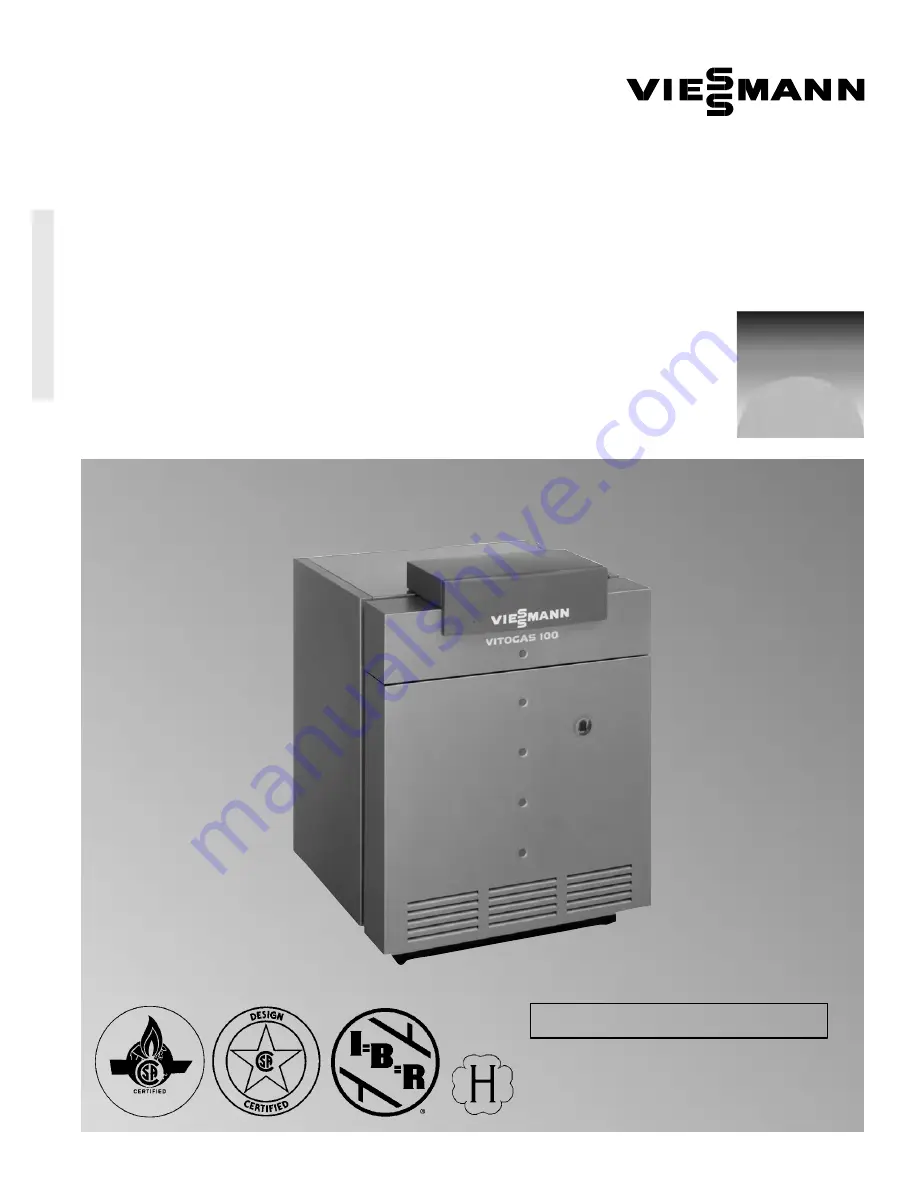
Read and save these instructions
for future reference.
IMPORTANT
VITOGAS 100
Installation Instructions
for Use by Heating Contractor
Vitogas 100
GS1 Series
Natural gas-/propane-fired, single-stage
atmospheric cast-iron boiler
Heating input
90 to 240 MBH
26 to
70 kW
P
le
a
s
e
fi
le
in
S
e
r
v
ic
e
B
in
d
e
r
5167 463 v1.3 02/2011
Summary of Contents for Vitogas 100 GS1 Series
Page 35: ...35 5167 463 v1 3 ...