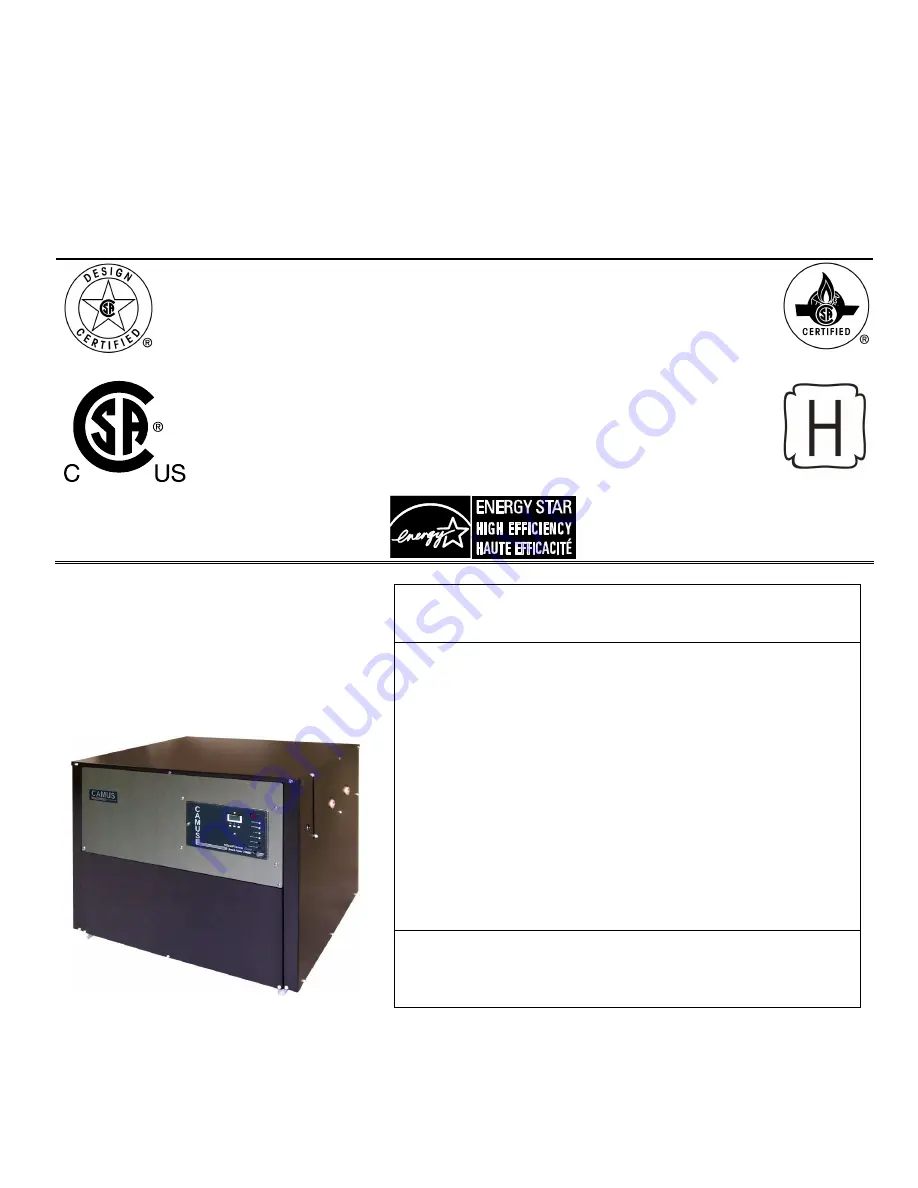
99-0073
Rev. 00
INSTALLATION OPERATION
AND SERVICE MANUAL
MODULATING MICOFLAME SERIES
GAS FIRED RESIDENTIAL AND COMMERCIAL COPPER TUBE
BOILERS
FOR HYDRONIC HEATING
Non-Condensing Models; MFH060, 100, 150, 200, 250, 300, 400, 500, 600
Condensing Models; MFH062, 102, 152, 202, 252, 302, 402, 502, 602
HOT WATER SUPPLY
Non-Condensing Models; MFW060, 100, 150, 200, 250, 300, 400, 500, 600
Condensing Models; MFW062, 102, 152, 202, 252, 302, 402, 502, 602
WARNING: If the information in these instructions is not
followed exactly, a fire or explosion may result causing
property damage, personal injury or death
•
Do not store or use gasoline or other flammable
vapours and liquids in the vicinity of this or any other
appliance.
•
WHAT TO DO IF YOU SMELL GAS
o
Do not try to light any appliance,
o
Do not touch any electrical switch; do not use any
phone in your building,
o
Immediately call your gas supplier from a
neighbour’s phone. Follow the gas supplier’s
instructions,
o
If you cannot reach your gas supplier, call the fire
department.
•
Qualified installer, service agency or the gas supplier
must perform installation and service.
To the installer: After installation, these instructions must be
given to the end user or left on or near the heater.
To the End User: This booklet contains important information
about this heater. Retain for future reference.
CAMUS HYDRONICS LTD.
6226 Netherhart Road, Mississauga, Ontario, L5T 1B7