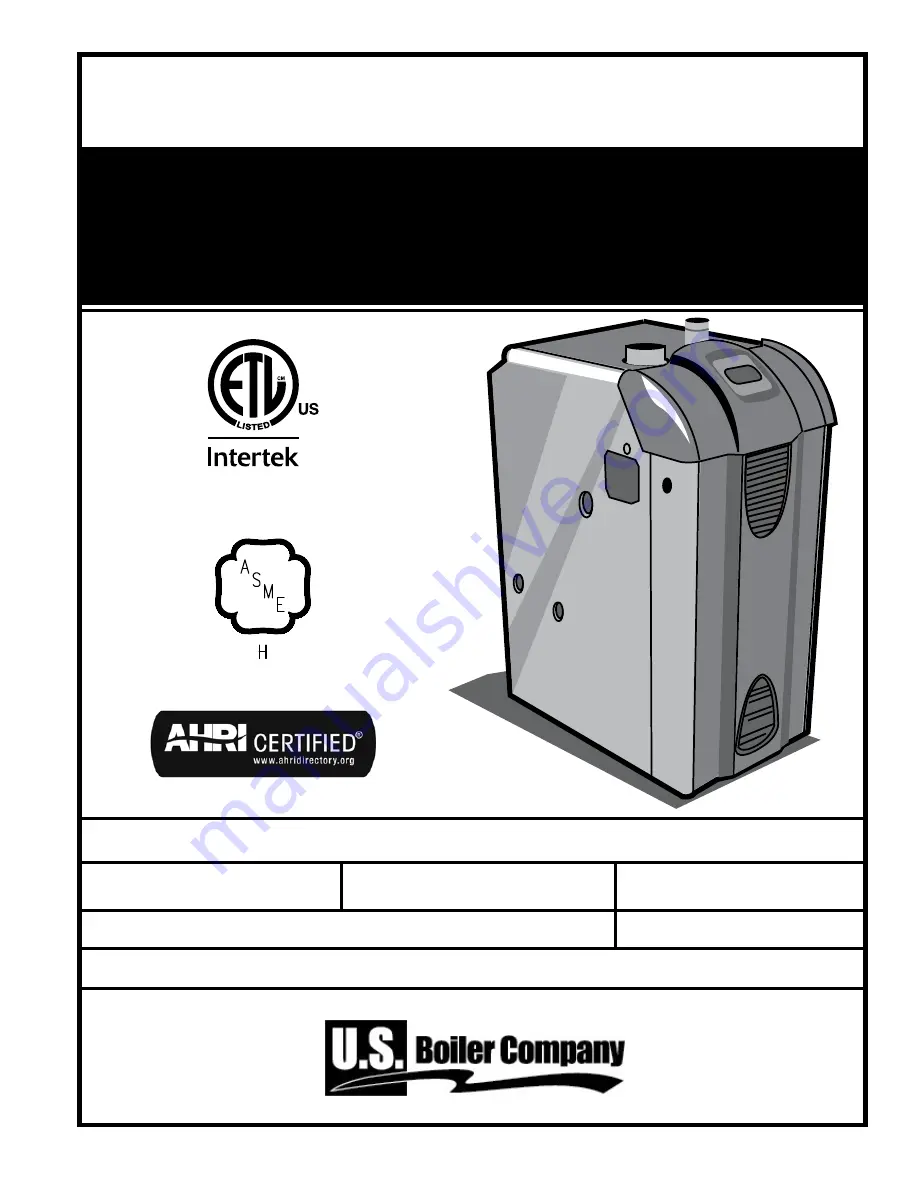
INSTALLATION, OPERATING AND
SERVICE INSTRUCTIONS FOR
ESC
™
ENHANCED SEALED COMBUSTION
Gas - Fired Boiler
103788-03 - 9/13
For service or repairs to boiler, call your heating contractor. When seeking information on boiler, provide
Boiler Model Number and Serial Number as shown on Rating Label.
Boiler Model Number
ESC_C
Boiler Serial Number
Installation Date
Heating Contractor
Phone Number
Address
9700609
Price - $5.00
Summary of Contents for ESC
Page 7: ...7 Figure S 1 Minimum Clearances to Combustibles SPECIFICATIONS continued...
Page 20: ...20 Figure 10 d Operating Instructions 10 Perform Startup Checks and Adjustments continued...
Page 37: ...37 Internal Wiring Figure IW 1 Wiring Diagram...
Page 38: ...38 Internal Wiring continued Figure IW 2 Wiring Diagram...