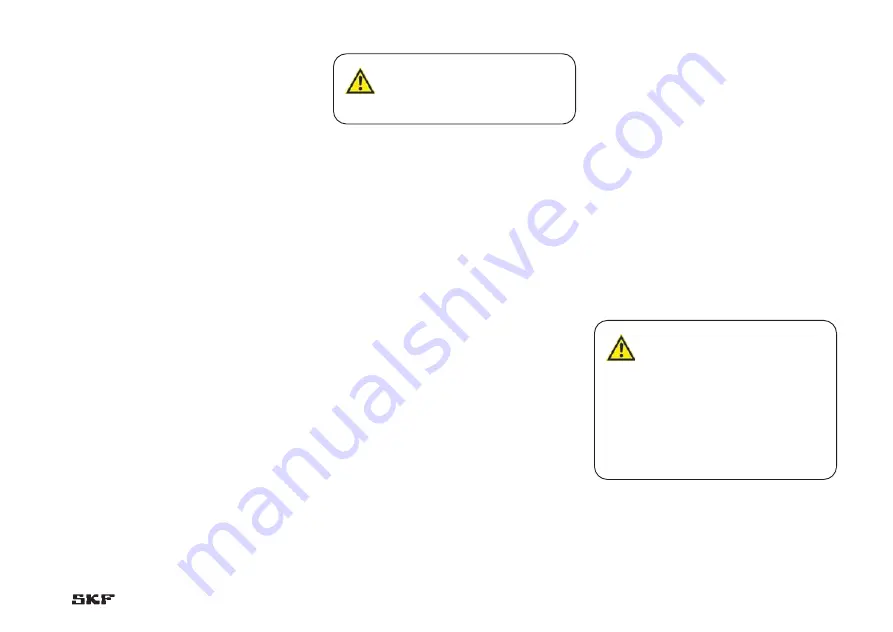
4. Installation
instructions
The minimal quantity lubrication system de-
scribed in the mounting instructions may
only be installed, operated, maintained, and
repaired by qualified experts. Qualified per-
sonnel are persons who have been trained,
instructed, and familiarized by the user of
the end product into which the system is in-
stalled. These persons are considered capa-
ble of such tasks due to their education,
training, and experience with valid stan-
dards, conditions, accident prevention regu-
lations in effect, and installation conditions.
They should be able to carry out the required
tasks and to recognize – and thus avoid – any
dangers that might otherwise occur.
A definition of what constitutes a qualified
person and who are unqualified persons are
stipulated in DIN VDE 0105 and IEC 364.
Before installing/positioning the minimal
quantity lubrication system, remove the
packaging material and any transportation
safety devices such as sealing plugs. Keep
the packaging material until any and all
problems have been clarified.
Country-specific accident prevention reg-
ulations and the operating and maintenance
instructions for the operator must be ob-
served when carrying out all installation
work on machines.
C A U T I O N !
The lubrication system must not
be tipped over or thrown.
4.1 Positioning and
installation
The system must be protected from mois-
ture and vibrations but on the other hand
mounted so that it is easily accessible to en-
sure that all further installation work can be
carried out without difficulty. Ensure that
there is sufficient circulating air to prevent
the system from overheating. For informa-
tion on the maximum permitted ambient
temperature, see technical data.
C A U T I O N !
The minimal quantity lubrication
system must be securely fixed to its sup-
port to avoid accidental tipping. If the
system falls it could be damaged or
cause damages and can also injure an
operator or another person.
19
Summary of Contents for VectoLub VE1B
Page 2: ......