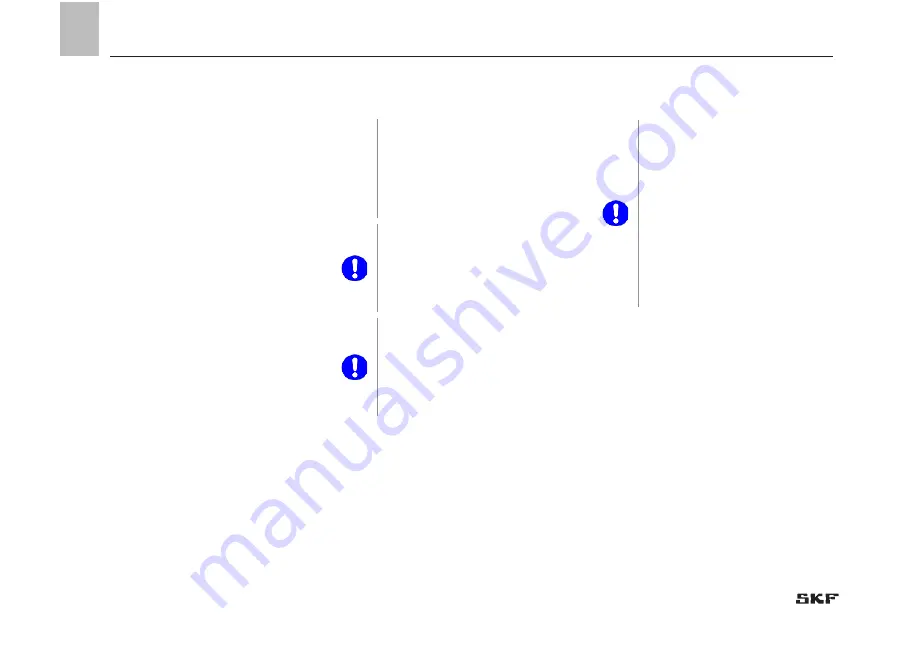
18
EN
Only lubricants specified for the
product may be used. Unsuitable
lubricants may lead to a failure of
the product.
Do not mix lubricants. This may
have unforeseeable effects on
the usability and therefore on the
function of the centralized lubri-
cation system.
When handling lubricants the rel-
evant safety data sheets and haz-
ard designations, if any, on the
packaging have to be observed.
2.5 Ageing of lubricants
After a prolonged downtime of the machine,
the lubricant must be inspected prior to
re-commissioning as to whether it is still
suitable for use due to chemical or physical
ageing. We recommend that you undertake
this inspection already after a machine
downtime of 1 week.
If doubts arise as to a further suitability of
the lubricant, please replace it prior to re-
commissioning and, if necessary, undertake
initial lubrication manually.
It is possible for lubricants to be tested in the
company's laboratory for their suitability for
being pumped in centralized lubrication sys-
tems (e.g. "bleeding").
Please contact SKF. if you have further ques-
tions regarding lubricants.
You may request an overview of the lubri-
cants tested by SKF.
Due to the multitude of possible
additives, individual lubricants,
which according to the manu-
facturer's data sheets fulfil the
necessary specification, may not,
in fact, be suitable for use in cen-
tralized lubrication systems (e. g.
incompatibility between synthetic
lubricants and materials).
In order to avoid this, always use
lubricants tested by SKF.
2. Lubricants