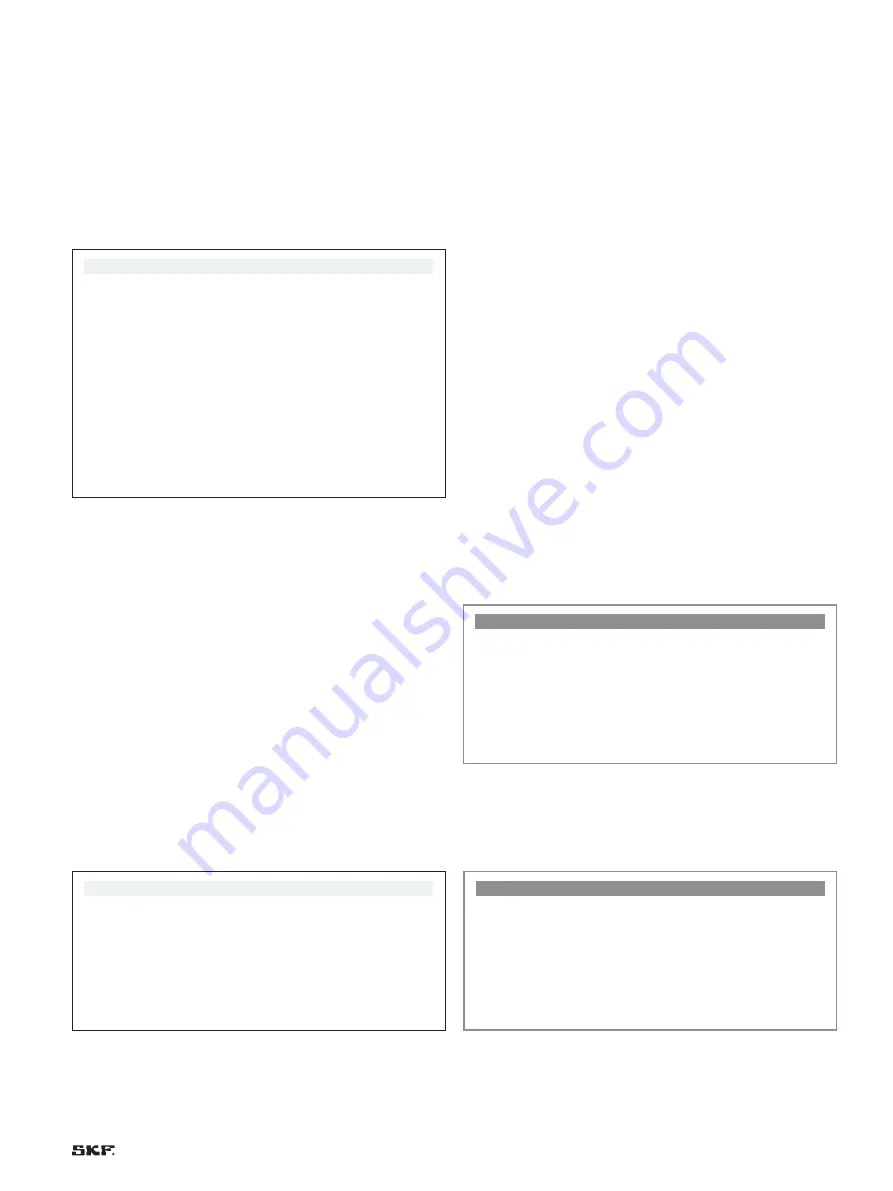
1. Safety instructions
The described product was manufactured in accordance with all
generally acknowledged regulations pertaining to technology, occu-
pational safety, and accident prevention. However, dangers that can
cause physical injury to persons or damage to other material assets
might still occur during the use of the product.
NOTE
These instructions must be read and understood by all persons
who are involved with the installation, operation, maintenance,
and repair of the product. These instructions must be kept close
to the equipment for future reference.
Note that these installation instructions is an integral part of
the product. It must be handed over to the new operator of the
product if the product is sold.
In addition to the information provided in the installation ins-
tructions, all generally applicable regulations on accident pre-
vention and the environment must be observed.
1.1 Intended use
The product is designed for the lubrication of moving conveyor
chains. Other use or use beyond this purpose is considered
unintended.
Products of SKF must not be used in conjunction with subs-
tances and mixtures classiied as hazardous by the Annex I part
2-5 of the CLP regulation (EC 1272/2008), and identiied with
hazard pictograms GHS01-GHS06 and GHS08.
None of the products manufactured by SKF can be used in
conjunction with gases, liqueied gases, pressurized gases in solu-
tion and luids with a vapor pressure exceeding normal atmosphe-
ric pressure (1013 mbar) by more than 0,5 bar at their maximum
permissible temperature.
Unless otherwise noted, products of SKF must not be used in
conjunction with explosive atmospheres according to the ATEX-Di-
rective 2014/34/EU.
NOTE
All SKF products may be used strictly respecting the instructions
described in this brochure or the operating instructions.
1.2 Authorized personnel
The products described in the installation instructions may only be
installed, operated, maintained, and repaired by qualiied experts.
Qualiied experts are persons who have been trained, instructed, and
familiarized with the end product into which the described product is
installed.
These persons are considered capable of such tasks due to their
education, training, and experience with valid standards, conditions,
accident prevention regulations in effect, and installation conditions.
They should be able to carry out the required tasks and to recognize
– and thus avoid – any dangers that might otherwise occur.
A deinition of what constitutes a qualiied person and who are
unqualiied persons are stipulated in DIN VDE 0105 and IEC 364.
1.3 Danger relating to electric
current
The electrical connection for the described product may only be
established by qualiied, instructed persons who have been autho-
rized by the operator or owner to carry out this task. If the product is
improperly connected, substantial material or personal damage my
be the consequence.
1.4 Danger relating to system
pressure
C AUTION!
Working on products that have not been disconnected from the
power supply can cause serious injury or death to persons. Ins-
tallation, maintenance, and repair work may only be carried out
by qualiied experts on products that have been disconnected
from the power supply. The supply voltage must be turned off
before any product components are opened.
C AUTION!
Centralized lubrication systems are under pressure when they
are being operated. Such systems must therefore be depressu-
rized before starting installation, maintenance, or repair work
and before making any changes to the system.
5