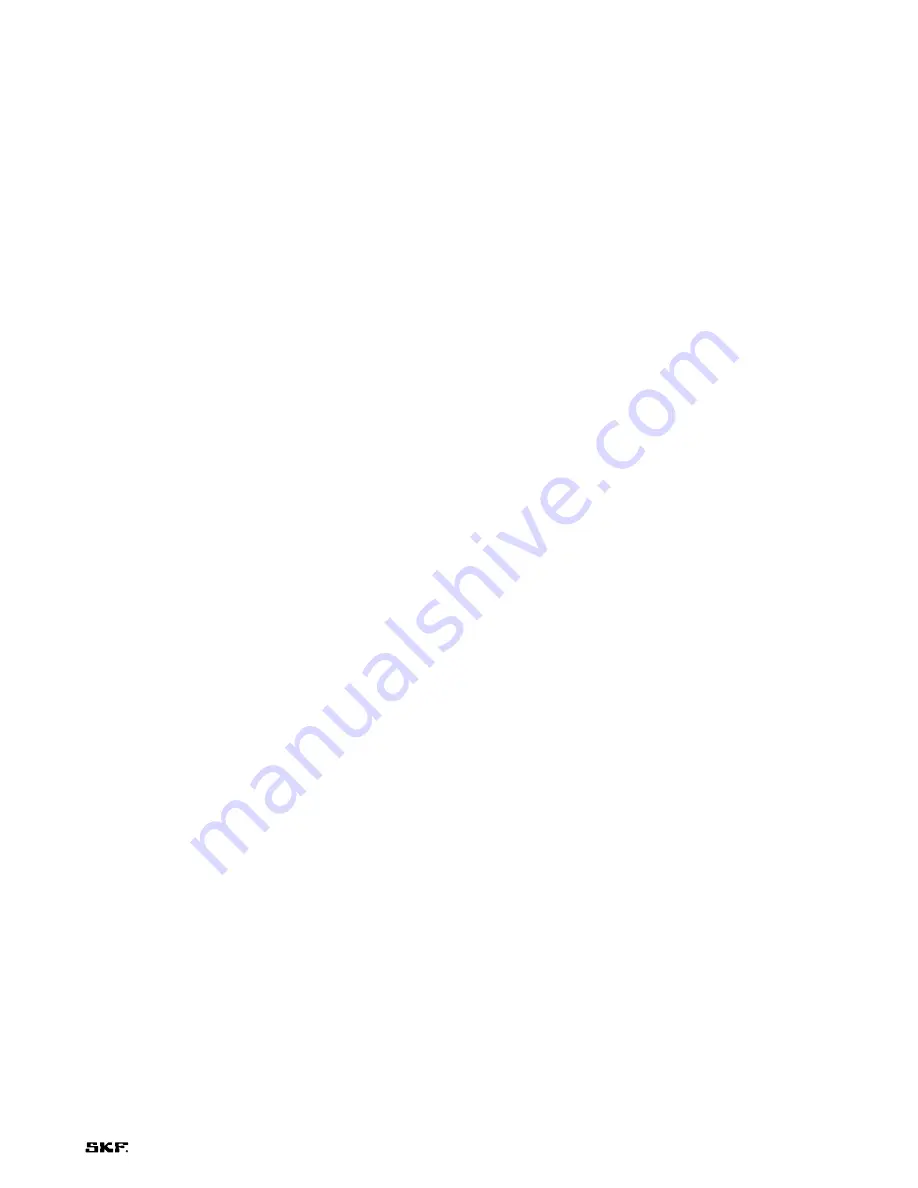
1.4 Warranty terms
The applicable and effective warranty terms are those contained in
the manufacturer’s terms and conditions of sale.
1.5 Customer service
SKF Customer Service is always available to provide technical infor-
mation and answer questions.
The contact information for SKF Customer Service can be found
on www.SKF.com.
7