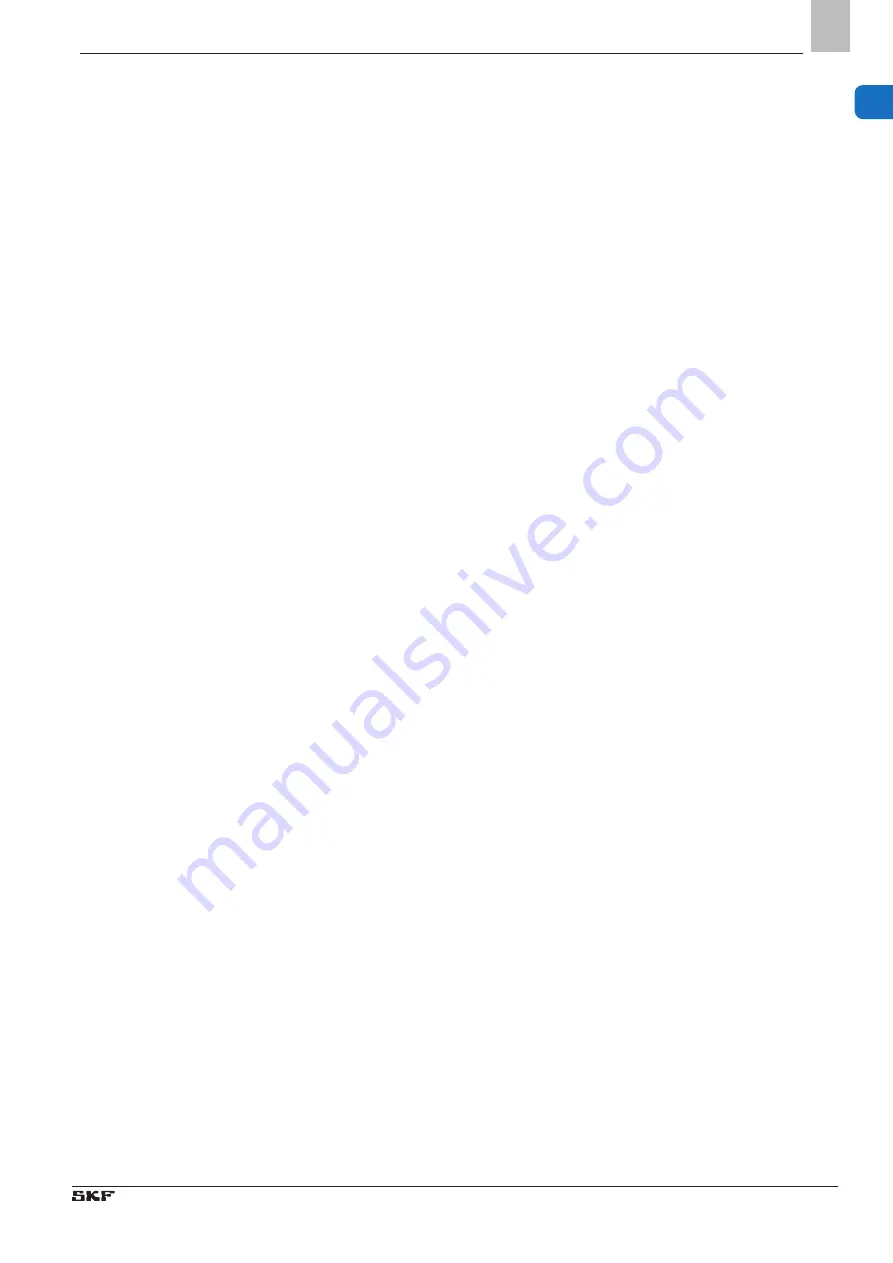
- 11 -
EN
951-180-074-EN Version
03, last updated 2019 / 07
1
1. Safety instructions
○
All components used must be designed
for:
- The maximum operating pressure
- The maximum/minimum ambient
temperature
-The lubricant to be delivered
-The required ATEX zone
-The operating/ambient conditions
at the place of use.
○
No parts of the centralized lubrication
device may be subjected to torsion, shear,
or bending.
○
Check all parts for contamination before
use and clean if necessary. Lubrication
lines should be filled with lubricant prior
to assembly. This simplifies subsequent
venting of the system.
○
Adhere to the specified torques. Use
a calibrated torque wrench when
tightening.
○
Use suitable hoisting equipment when
working with heavy parts.
○
Avoid mixing up/incorrectly assembling
disassembled parts. Label parts.
1.17 Initial commissioning, daily
startup
Ensure that:
○
All safety mechanisms are fully present
and functional.
○
All connections are properly connected.
○
All parts are correctly installed.
○
All warning labels on the machine are
fully present, visible, and undamaged.
○
Illegible or missing warning labels are
immediately replaced.
○
The machine is properly grounded
1.18 Cleaning
○
Fire and explosion hazard from the use
of flammable cleaning agents. Use only
non-flammable cleaning agents that are
suitable for the intended purpose.
○
Do not use harsh cleaning agents.
○
Do not use sharp-edged or sparking
tools for cleaning (e.g., of the cooling fins
on the motor).
○
Do not use stream-jet equipment / high-
pressure cleaners. This may damage
electrical components. Observe the IP
protection class.
○
Cleaning work on conducting compo-
nents may be performed only by quali-
fied electricians.
○
Mark wet areas accordingly.
1.19 Identification of hazards
The operator must identify all hazards
resulting from integration into the main
machine as well as the hazards at the ma-
chine’s place of installation. The operator
must take necessary measures for safety
and health protection.
1.20 Provision of necessary
information
The operator must the relevant required
instructions available to all persons assigned
with operation, repair, and maintenance.
The operator must ensure that the persons
in question have read and understood the
required instructions.
The same applies to all relevant safety
data sheets, operational instructions,
accident prevention regulations, instructions
from suppliers of purchased parts and
consumables.
Depending on the operational organiza-
tion, the relevant instructions may need
to be made available to further persons/
departments.
1.21 Duty to provide instruction and
training
The operator clearly defines the responsi-
bilities of the personnel for operation/instal-
lation/maintenance. Prior to the first use of
the machine, the operator is obligated to in-
struct all persons authorized to use the ma-
chine on its proper handling in accordance
with their respective field of activity
and responsibility using practical exercises.
The instruction includes at least:
○
Zone classification
○
Scope and limits of the area of activ-
ity and responsibility for the respective
group of people
○
Safety-conscious behavior/behavior in an
emergency
○
Avoidance of hazards when handling the
machine
○
Meaning of warnings, warning labels
○
Handling operating materials and clean-
ing agents
○
If necessary, use and monitoring of per-
sonal protective gear
These instructions must be documented and
repeated at regular intervals. New staff may
operate the gerotor pump unit/the machine
only under the supervision and instruction
of experienced staff.