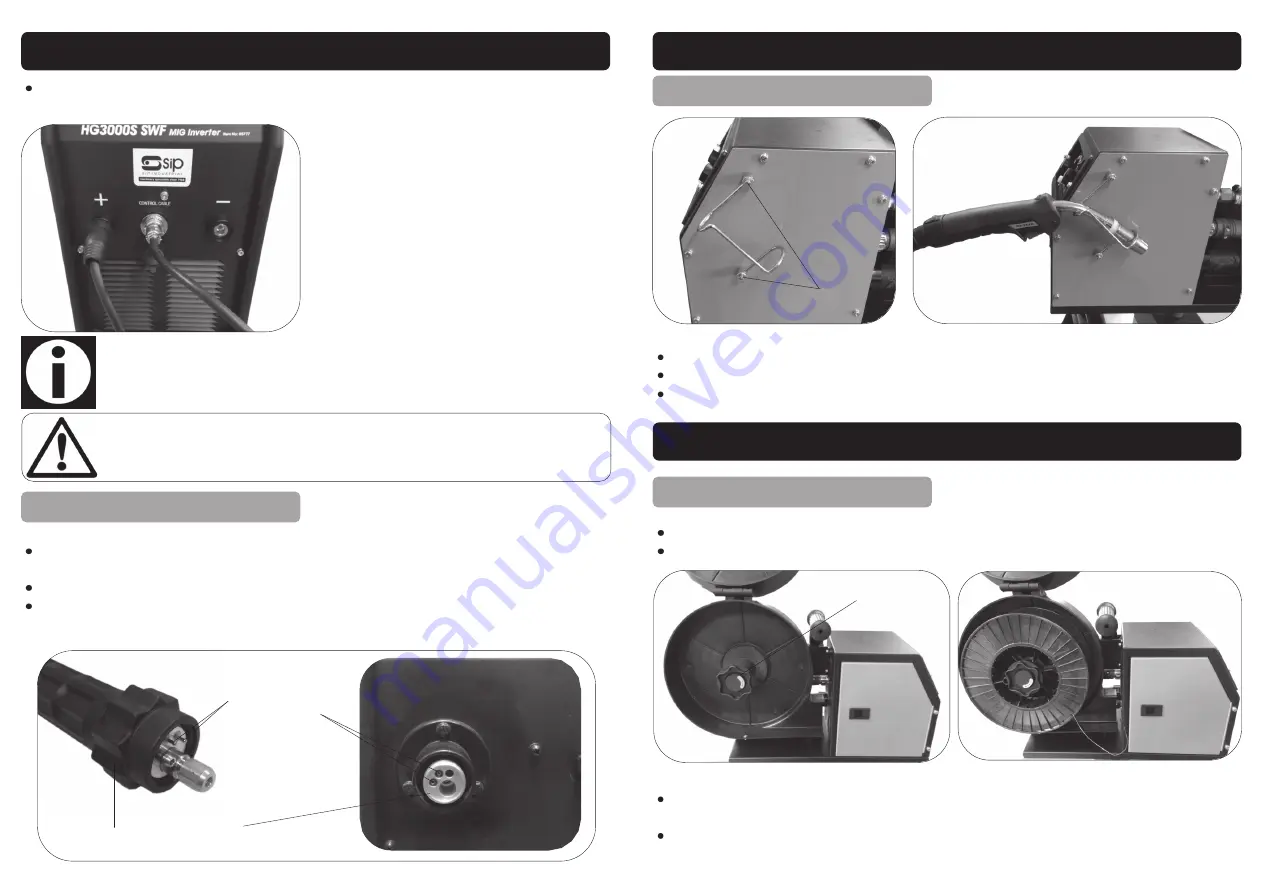
18
ASSEMBLY INSTRUCTIONS….cont
Danger:
Ensure that the gas pipe is secure and leak free before operation.
Connect both parts at the opposite end of the interconnecting cable to the
front of the welder (see below).
Align the 2 torch pins on the welding torch with the 2 connector holes on the euro
adaptor.
Push the welding torch in to the euro adaptor.
Screw the torch locking ring on to the euro adaptor and tighten to secure.
Locking ring
Euro adaptor
Torch pins
Holes
CONNECTING THE TORCH
Note:
Connect the lead to the positive (+) terminal for standard welding
and negative (-) for flux cored welding.
19
ASSEMBLY INSTRUCTIONS….cont
Lift up the wire spool cover.
Turn the wire retaining nut clockwise to loosen and remove it.
Retaining Nut
Fit the welding wire over the spool holder so that the wire will feed from the
bottom of the roll.
Refit the retaining nut, and secure in place by tightening it.
Retaining Screws
Loosen the torch holder retaining screws.
Fit the torch holder.
Retighten the retaining screws.
FITTING THE TORCH HOLDER
LOADING THE WIRE
OPERATING INSTRUCTIONS