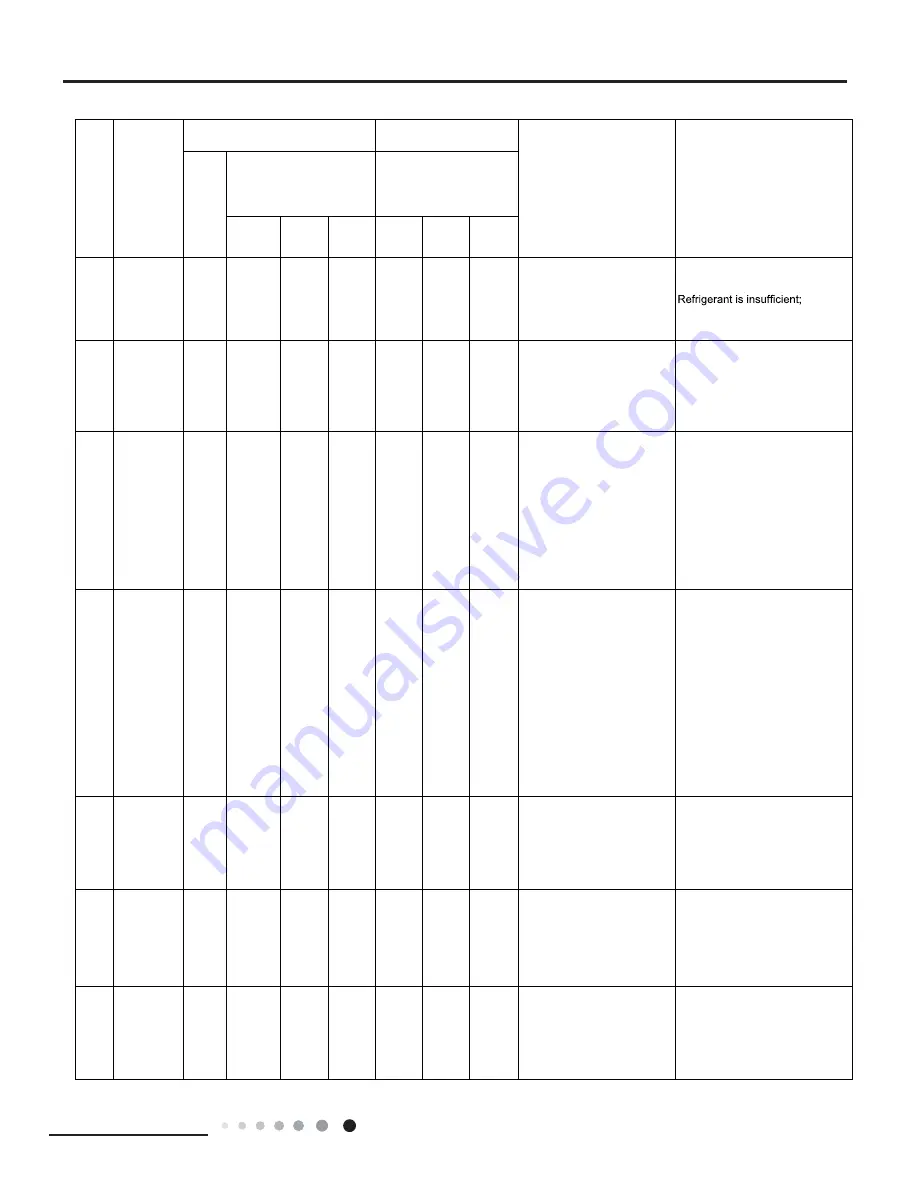
33
Installation and Maintenance
Service Manual
NO.
Malfunction
Name
Display Method of Indoor Unit
Display Method of Outdoor
Unit
A/C status
Possible Causes
Dual-8
Code
Display
Indicator Display (during
blinking, ON 0.5s and OFF
0.5s)
Indicator has 3 kinds of
display status and during
blinking, ON 0.5s and OFF
0.5s
Operation
Indicator
Cool
Indicator
Heating
Indicator
Yellow
Indicator
Red
Indicator
Green
Indicator
19
Decrease
frequency
due to
high air
discharge
F9
OFF 3S
and blink
9 times
OFF 1S
and
blink
twice
All loads operate normally,
while
operation frequency for
compressor is decreased
Overload or temperature is too
high;
Malfunction of electric expansion
valve (EKV)
20
Limit/
decrease
frequency
due to
antifreezing
FH
OFF 3S
and blink
2 times
OFF 3S
and blink
2 times
OFF 1S
and
blink
4 times
All loads operate normally,
while operation frequency for
compressor is decreased
Poor air-return in indoor unit or fan
speed is too low
21
Voltage for
DC bus-bar
is too high
PH
OFF 3S
and blink
11 times
OFF 1S
and
blink
13 times
During cooling and drying
operation, compressor will stop
while indoor fan will operate;
During heating operation, the
complete unit will stop
operation.
1. Measure the voltage of position
L and N on wiring board (XT), if the
voltage is higher than 265VAC, turn
on the unit after the supply voltage
is increased to the normal range.
2.If the AC input is normal,
measure the voltage of electrolytic
capacitor C on control panel (AP1),
if its normal, theres malfunction
for the circuit, please replace the
control panel (AP1)
22
Voltage of
DC bus-bar
is too low
PL
OFF 3S
and blink
21 times
OFF 1S
and
blink
12 times
During cooling and drying
operation, compressor will stop
while indoor fan will operate;
During heating operation, the
complete unit will stop
1. Measure the voltage of position
L and N on wiring board (XT), if the
voltage is higher than 150VAC,
turn on the unit after the supply
voltage is increased to the normal
range.
2.If the AC input is normal,
measure the voltage of electrolytic
capacitor C on control panel (AP1),
if its normal, theres malfunction
for the circuit, please replace the
control panel (AP1)
23
Compressor
Min
frequence in
test state
P0
(during
blinking,
ON
0.25s
and OFF
0.25s)
(during
blinking,
ON
0.25s
and OFF
0.25s)
Showing during min. cooling or
min. heating test
24
Compresso r
rated
frequenc e in
test state
P1
(during
blinking,
ON
0.25s
and OFF
0.25s)
(during
blinking,
ON
0.25s
and OFF
0.25s)
Showing during nominal cooling or
nominal heating test
25
Compressor
maximum
frequence in
test state
P2
(during
blinking,
ON
0.25s
and OFF
0.25s)
(during
blinking,
ON
0.25s
and OFF
0.25s)
Showing during max. cooling or
max. heating test
Summary of Contents for ASH-09AIM PT
Page 1: ...SERVICE MANUAL ASH 09AIM PT ASH 13AIM PT MATRIX SERIE ...
Page 2: ......
Page 12: ...7 Technical Information Service Manual 596 354 838 899 303 378 550 Unit mm ASH 13AIM PT ...
Page 79: ......
Page 80: ...PARTS GUIDE MATRIX SERIE ASH 09AIM PT ASH 13AIM PT ...
Page 82: ...Service Manual Exploded View and Parts List ASH 09AIM PT ...
Page 84: ...Service Manual ASH 13AIM PT ...
Page 86: ...Service Manual Outdoor Unit ASH 09AIM PT ...
Page 88: ...Service Manual ASH 13AIM PT ...