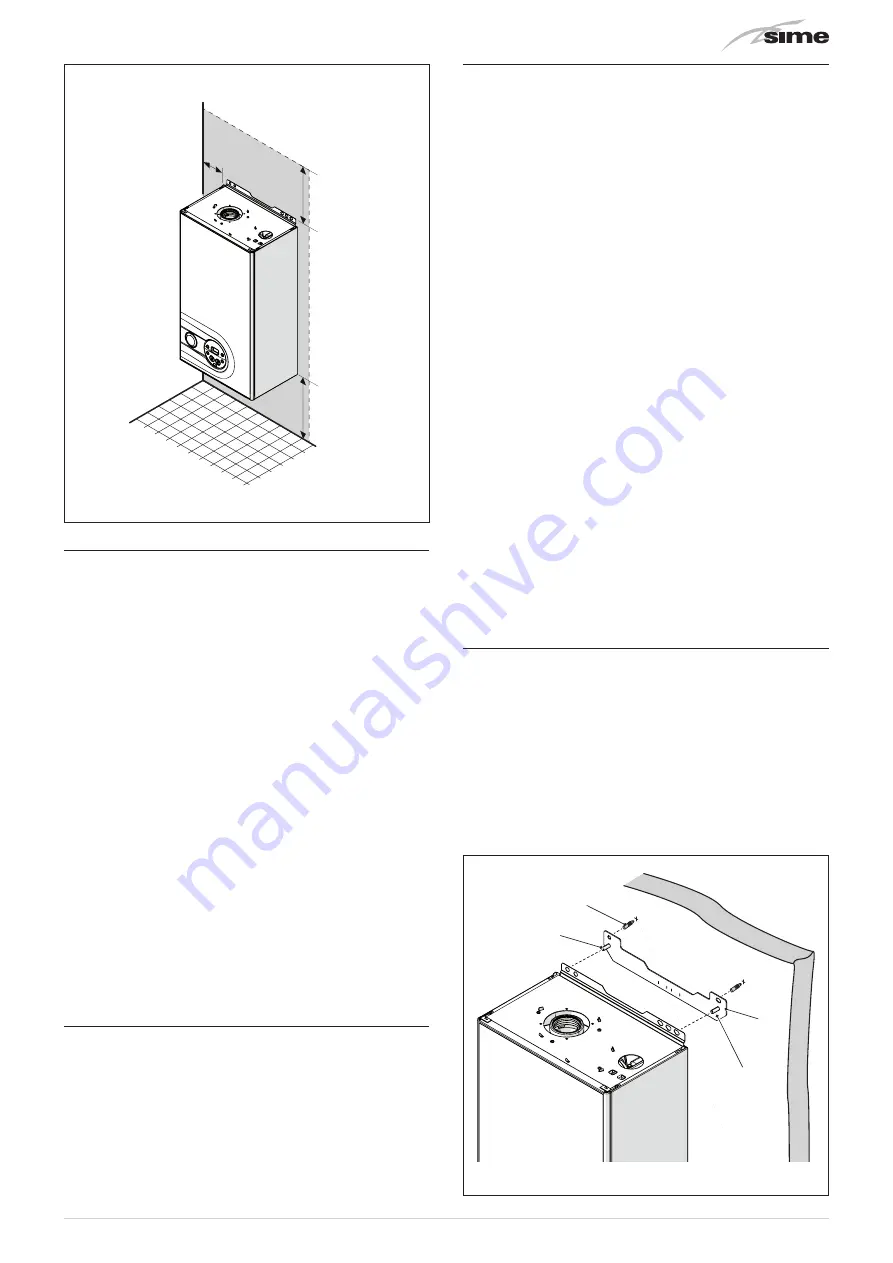
27
APPROXIMATE MINIMUM DISTANCES
≥ 15 mm
≥ 200 mm
≥ 200 mm
Fig. 17
6.5
New installation or installation of a re-
placement appliance
The boiler must be installed in a fixed location and only by spe-
cialized and qualified person in compliance with all instructions
contained in this manual.
The installation of this boiler must be in accordance with the
relevant requirements of the current Gas Safety (installation
and use), the local building regulations and I.E.E. wiring reg-
ulations.
Detailed recommendations for air supply and fluing are given
in BS5440.
The following notes are for general guidance: it is not neces-
sary to have a purpose provided air vent in the room or com-
partment in which the appliance is installed.
m
CAUTION
It is a condition of the warranty that the boiler is in-
stalled in accordance with the instructions in this
manual. The boiler must be registered with Gas Safe
Register, the Benchmark record must be completed
and the boiler is serviced annually and recorded in
this manual.
m
CAUTION
If the domestic water supply is metered or should a
water meter be added at a later time, a small expan-
sion vessel should be included in the domestic water
pipework.
6.6
Cleaning the system
Before connecting the boiler it is recommended that the system
be flushed in accordance to BS 7593, to eliminate any foreign
bodies that may be detrimental to the operating efficiency of
the appliance.
m
CAUTION
Failure to flush and add inhibiter to the system may
invalidate the warranty.
6.7
Characteristics of feedwater and system
treatment
– All recirculatory systems will be subject to corrosion unless
an appropriate water treatment is applied. This means that
the efficiency of the system will deteriorate as corrosion
sludge accumulates within the system, risking damage to
pump and valves, boiler noise and circulation problems.
– Before connecting the boiler the associated central heating
system must be flushed in accordance with the guidelines
given in BS 7593 “Treatment of water in domestic hot water
central heating systems”.
–
Sime Ltd
recommends only the use of FERNOX products for
the flushing and final treatment of the system water. This is
particularly important in hard water areas. Failure to flush
and add inhibitor to the system may invalidate the appliance
warranty. Artificially softened water must not be used to fill
the heating system. Naturally soft water areas can corrode
aluminium heat exchangers. Adding Fernox F1 or Mb-1 will
guard against corrosion.
–
Sime Ltd
promote the fitting of TF1 System filter with any new
boiler installation.
– It is important to check the inhibitor concentration after in-
stallation, system modification and annually on a service visit
in accordance with the manufacturer’s instructions. (Note
on benchmark service record this has been complete). Test
kits are available from inhibitor stockists; the return of the
Fernox test report should be kept with the Benchmark to val-
idate warranty.
– Where Central heating systems are susceptible to freezing
a mixture of inhibitor and anti-freeze should be added in ac-
cordance with the DWTA code of practice and the Manufac-
tures instructions.
– The addition of sealing agents to system water is not rec-
ommended because deposits can be left in heat exchanger
causing circulation issues.
6.8
Boiler installation
Murelle Pro HE MkII
are supplied with a hanging bracket and a
template to assist installation.
For installation:
– position the bracket (1) on the wall (2), where you want to
install the boiler
– check that it is straight and mark where to make the holes
for the plugs
– drill the holes and insert the expansion plugs (3) which will
be used to fix the bracket securely
– hook the boiler onto the pins (4) and secure it using the nuts
and washers supplied.
1
2
3
4
Fig. 18