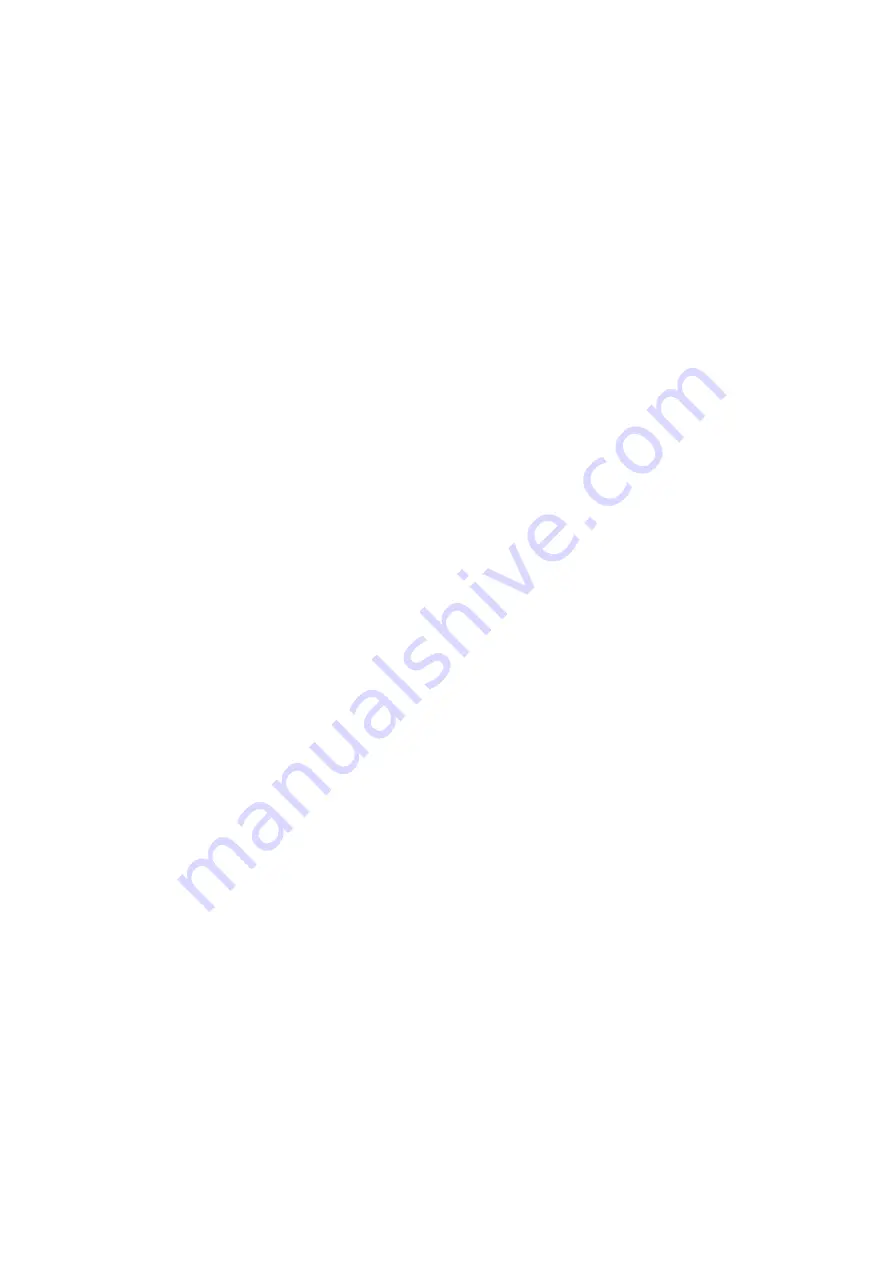
SC12205-K10-15002A
2nd
43
Copyright 2020, SIGMAKOKI Co.,Ltd.
Chapter 7: Specifications
7-1.Specifications
1. General Specifications
Power source
AC100-240[V] 50/60[Hz]
Consumption
200[VA]
Operating temperature
5
~
40[
℃]
Storage temperature
-20
~
60[
℃]
Altitude
up to 2000[m]
Indoor use only
Installation category
Ⅱ
Pollution degree
2
Ambient humidity
20 to 80%[RH] (no condensation)
External dimensions
260W×260D×95H(excluding projections) [mm]
Weight
3.3[kg]
2. Performance
Controlling axis
3 axis
Maximum driving speed (F)
0.01
~
9999999.99
μ
m/s
(1
~
4000000[PPS])
Minimum driving speed (S)
0.01
~
9999999.99
μ
m/s
(1
~
4000000[PPS])
Maximum No.of travel pulse
-134217728 [Pulse] ~ +134217727 [Pulse]
Acceleration/deceleration time (R)
1~ 1000[ms]
Sensor Input
Origin sensor / Proximity sensor / CW (-) Limit / CCW (+) Limit
(Memory switches can be used to change input logic for sensors.)
Interface
USB Interface (Serial communication)
Communication Parameters
・
Baud Rate
9600/38400/57600 [bps]
・
Data Bits
8bit
・
Parity
None
・
Stop Bit
1bit
・
Flow Control
Hardware
・
Delimiters
CR+LF
I/O
Input 4-pin (Photo-coupler Input, Internal Resistance 2.2k[
Ω
])
Output 4-pin (Open-collector Output Maximum Use Conditions DC24[V]
20m[A])