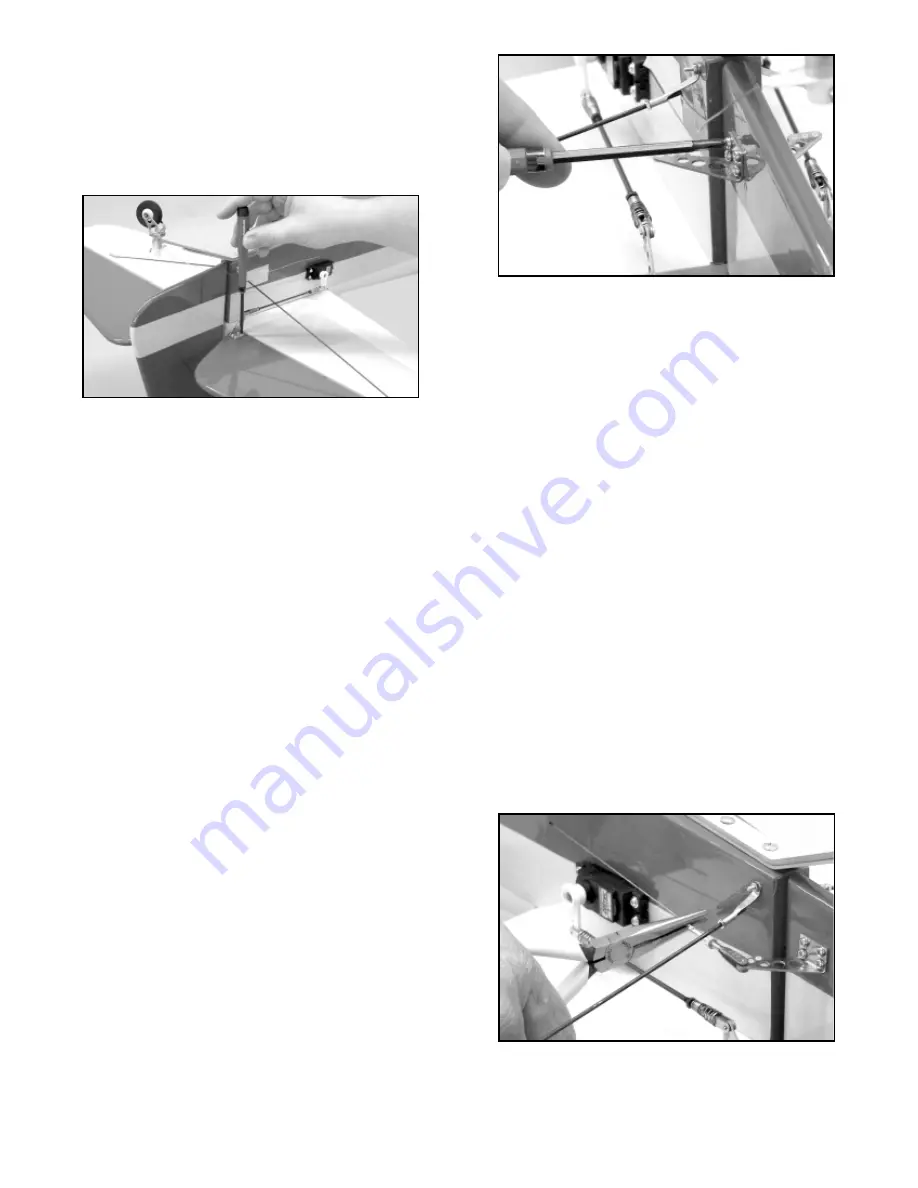
14
❑
34) You will need two metal control horns for the elevators, one
left and one right, and eight M2.8 x 10mm metal screws. Hold the
control horn in place on the elevator, lined up with the elevator
servo output arm. Make sure the pivot holes in the control horn
line up with the hinge line. Mark the control horn mounting holes
on the elevator with a felt pen. Drill a 3/64" dia. (or #56 drill) pilot
hole for each screw, then screw the horn in place. Repeat this
procedure on the opposite elevator.
IMPORTANT: After mounting the elevator control horns for the
first time, take them back off and set aside temporarily. Put a few
drops of Thin CA into each of the screw holes in the elevators. The
Thin CA will soak into the threads in the wood, increasing their
holding power. Be sure to use Thin CA, not medium or thick CA.
Let the thin dry completely before remounting the control horns.
❑
35) Because the elevator servos are staggered in the fuselage
two assembled elevator pushrods have been provided for the
elevators. The 4-40 pushrod for the left elevator measures 5-1/2",
and the pushrod for the right elevator measures 4". Use your radio
to center the elevator servos and then mount the output arms in
place at 90
O
upright. Tape the elevators to the stabilizer in the
neutral position. Attach the pushrod to the servo output arm in the
second hole from the end of the arm. Adjust the threaded R/C
links to fit into the middle hole of each elevator horn. Remove the
tape holding the elevators in the neural and test the movement of
the elevators with you radio system. Adjust as required to get both
elevators exactly at neutral (if you are using the Miracle "Y" chord,
you can turn the pot adjustment screw to achieve exact neutral
very easily). The final elevator throw adjustments and locking the
R/C links in place with the hex nuts will be made later.
❑
36) Tape the rudder in the neutral position. Remove the tape
holding the pull-pull cable to the fuselage and pull it straight back
against the rudder - note the cable exits the fuselage and runs
parallel to the bottom of the stabilizer.
Hold the cable in this
position and mark its location onto the side of the rudder with a
non-permanent marker pen. This line represents the mounting
location for the Metal control horns (one on each side of the
rudder). Re-tape the pull-pull cable back onto the fuselage side for
now.
❑
37) Place the 90
O
angle of the control horn onto the line just
made. In top view, line up its three linkage holes with the hinge line
of the rudder. Hold the control horn in position and use a marking
pen to mark the four base mounting hole locations onto the rudder.
Four 5/64" dia. holes are now drilled through the rudder at the four
marks just made. Make sure you hold the drill perpendicular to the
rudder when drilling these four holes. Then bolt the two control
horns in place using four M2.5 x 14mm (1/2") and four M2.5 Hex
nuts. Temporarily remove the horns and harden the holes with thin
CA . Allow the glue to cure and re-drill the holes with the 5/64" dia.
drill bit and reinstall the control horns.
BUILDER'S TIP (or straighten up and drill right):
Make a drill guide from a piece of scrap hardwood such as maple
and drill a hole through the scrap with the desired size of drill bit
in a drill press. Mark the location of the hole to be drilled with an
awl and slip the guide (scrap hardwood) over the drill bit. Place
the drill bit in the marked hole and hold the drill guide flush with the
surface. Drill through the surface making sure that your fingers are
out of the way when you drill through the surface.
❑
38) Center the R/C Link in the middle of the threads of the
rigging coupler and run the knurled stop nut up snuggly against the
R/C Link. Attach the rigging couplers and the R/C Links in the
outer holes of the rudder control horns. Turn on your radio system
and make sure the servo is centered and the trim on the
transmitter is also set in the middle of its range. Slip one of the
copper swage tubes onto the end of the cable. Then thread the
end of the cable through the small hole in the end of the rigging
coupler and take up any slack in the cable. Loop the end of the
cable back and run it through the copper swaging tube and pull up
the swaging tube up to the rigging coupler about 1/2" away from it.
Do not crimp the swaging tube at this time. Repeat this procedure
for the remaining pull-pull cable.
Next, with the rudder still taped in the neutral position, remove any
excess slack from each of the pull-pull cable by pulling on the short
end of the cable and sliding the swaging to towards the rigging
coupler. Using pliers or a crimping tool, squeeze the copper tube
tightly over the cable locking it in place. Cut off the excess short
end of the cable. Adjust the threaded R/C Links until you get both
pull-pull cables to approximately the same mild tension - Its not
necessary to pull the cables extremely tight.
Remove the tape holding the rudder in place, turn on the radio
system, and test the movement and centering of the rudder. Make
adjustments if needed. When satisfied with the operation of the
pull-pull system, tighten the knurled stop nut on each rigging