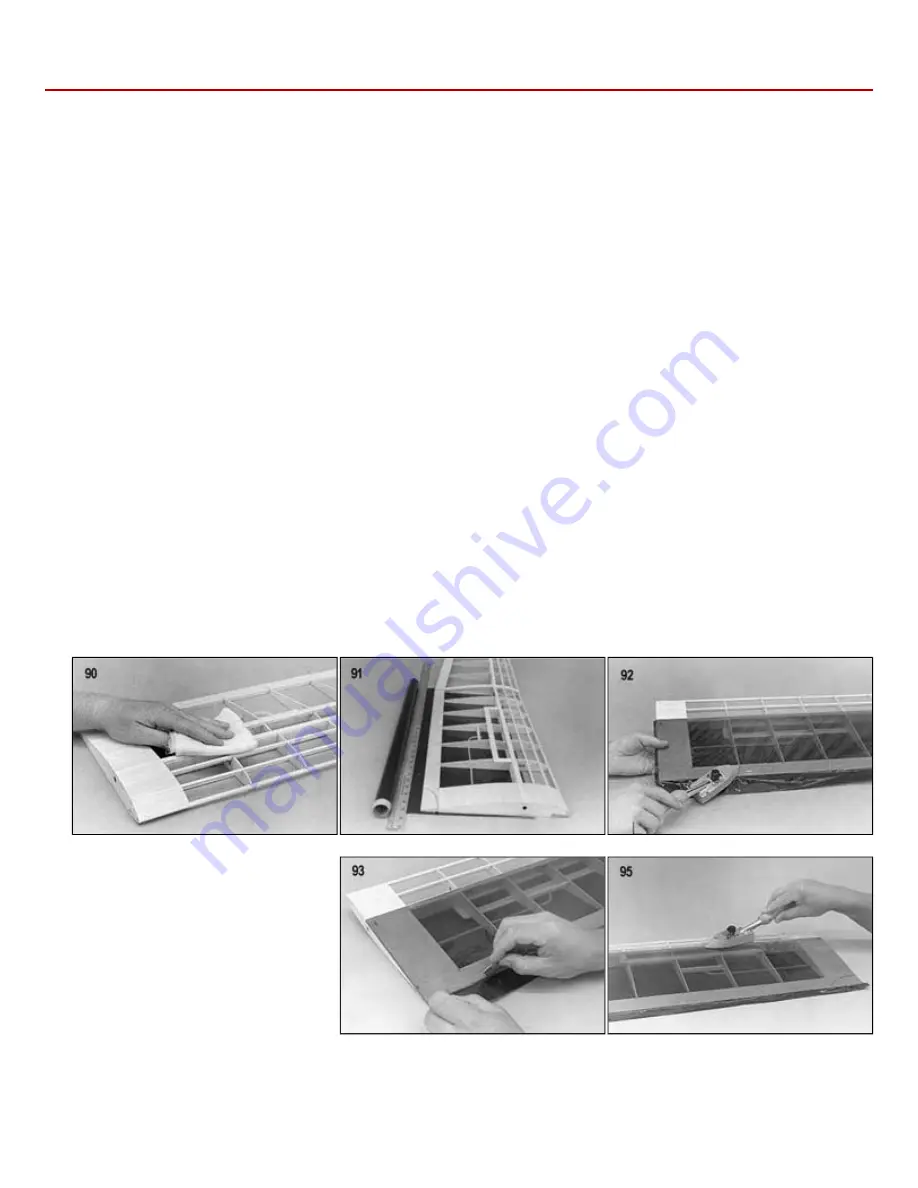
.
COVERING
All of the RISER 100 prototypes were covered with Sig Supercoat Iron-On Plastic Covering. The covering is ideal for
sailplanes because of it's light weight and ease of application.
Start by covering the wing from the main spar to the trailing edge with Transparent Blue. Next, cover the wing panel from
the spar forward to the leading edge with White. The white should overlap the Blue about 1/2" at the spar! Follow the same
procedures to cover the top and bottom of all four wing panels.
The fuselage should be completely covered with White Supercoat, and the Red and Blue stripes are then added with the
striping tape. Completely cover the stabilizer, elevators, fin, and rudder with Transparent Blue. Cut the White for the leading
edges of the stabilizer and fin from Sig SuperTrim, remove the paper backing, and press the White trim in place. Add Red
striping tape to the stab and fin to finish them.
NOTE: If you choose another brand of covering material, be sure to read the manufacturer's directions that come with the
material. Follow their instructions closely when applying the material, as different brand coverings can have slightly different
handling characteristics and application temperatures. However, the basic techniques for applying iron-on plastic coverings
of any brand are similar, and the following hints and photos should be helpful.
90.
The structure that is to be covered must be clean, dry, and dust free. Finish sand all the surfaces smooth with 220 or finer
abrasive paper. Remember that the covering material cannot hide poor workmanship. Whip the entire surface with a tack
rag or a cloth dampened with alcohol to remove excess dust.
91.
You should start by covering the bottom of the wing first and then the top of the wing. This leaves the overlapping seam on
the bottom where it is less visible. Cut the covering to size, allowing approximately one inch excess around the edges.
Remove the plastic backing from the covering and lay the adhesive side against the structure. Lay it down as smooth as
possible.
92.
Using your hot sealing iron (set a 200 deg. F for Sig Supercoat), tack down the covering material at several places around
the outside edges. Once it is smoothly tacked in place, work completely around the edges, sealing the covering entirely to
the structure. Don't try to shrink the covering tight at this time.
NOTE: If the surface of the sealing iron becomes contaminated with the colored adhesive that often oozes from under the
covering, wipe the iron clean with a dry cloth.
93.
Trim off the excess covering with a
sharp razor blade or modeling knife.
94.
Go over all of the edges of the covering
again with the hot sealing iron to make
sure they are sealed down securely.
95.
Repeat the process from Step 91 to
cover the top of the wing. Overlap all
covering seams at least 3/8" with the
covering material on the other side.
96.
To shrink the covering drum tight in the inner areas, we recommend that you use a "heat gun". A household hair dryer will
not get hot enough to shrink plastic model covering. You need a special heat gun made specifically for shrinking model
coverings. If you do not have a heat gun, you can also use your sealing iron to shrink the coverings tight. Cover the iron
with a sock and turn up the heat a little more than it was for sealing the edges to compensate for the sock being on. The
sock helps keep the iron from scratching the glossy surface of the covering material.