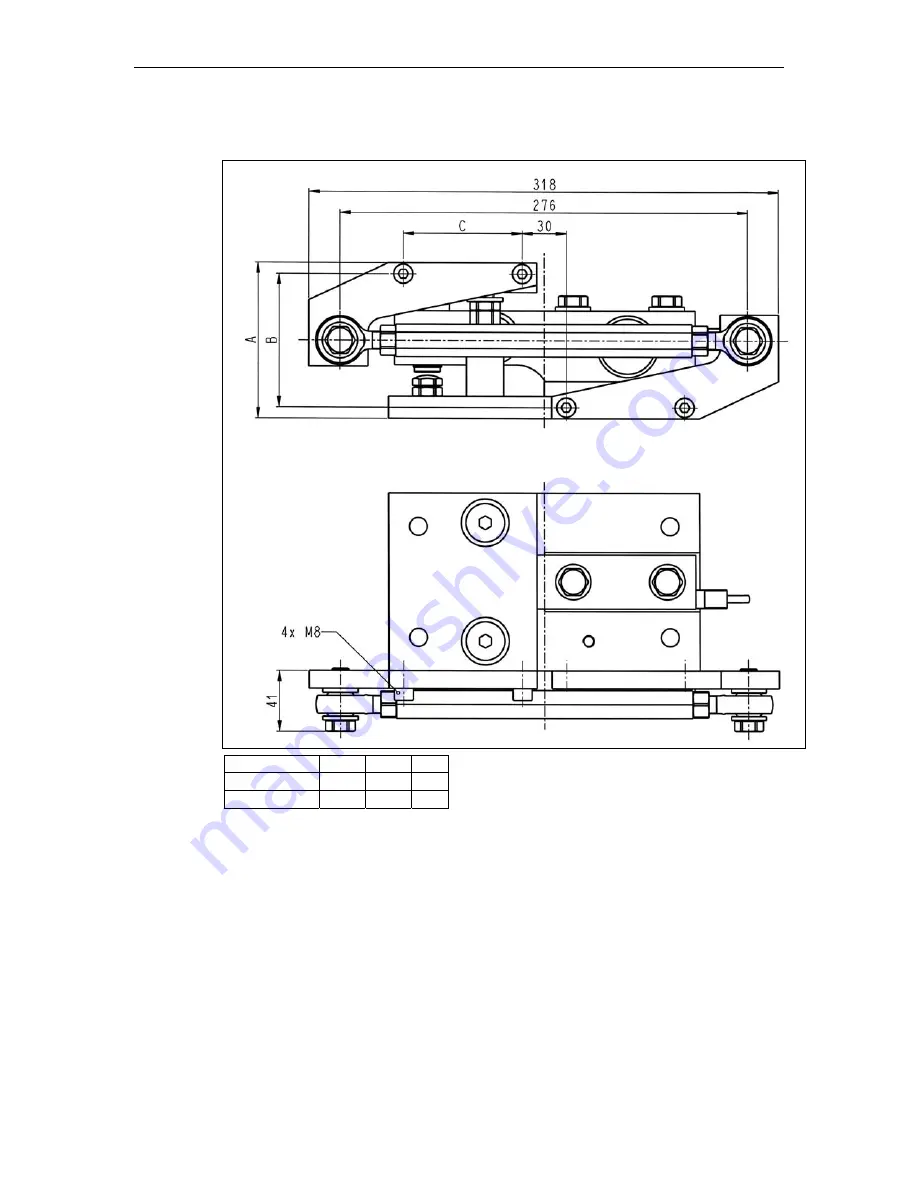
Revision 09/04
Guiding for comb. mounting unit
Document No.: A5E00353789B
Page 35
4.3.2 Dimensions
4.4 Care
and
Maintenance
The guidings must be kept free of contamination. They are normally maintenance-free. In
case of dynamic fluctuating loads, check regularly for loosening of screws.
Rated load
A
B
C
0.5 t, 1 t, 2 t
105
90
80
5
t
140 120
100
Fig. 4-5 Dimensions of guiding