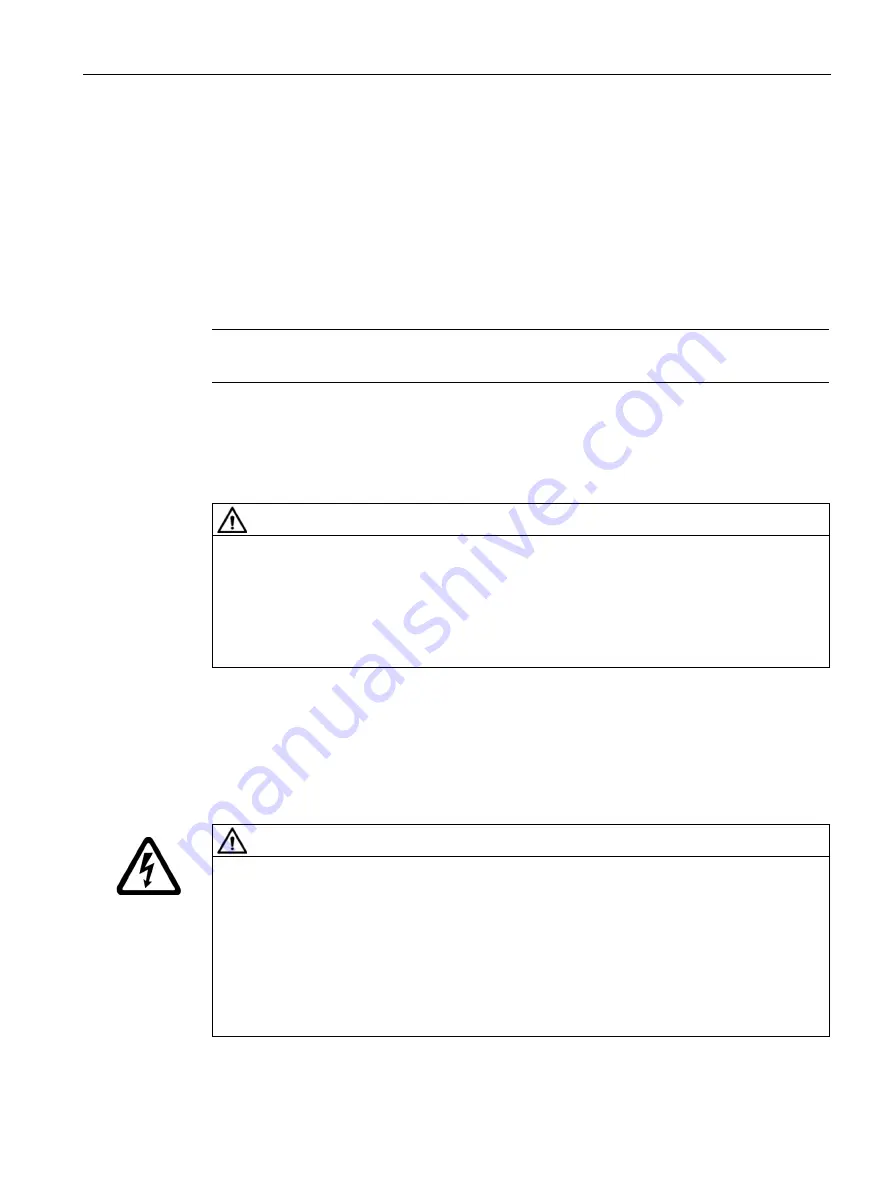
Maintenance
9.2 Inspection and maintenance
1MB..1/2/3/4 - shaft heights 63 ... 355
Operating Instructions, 06/2020, A5E44455710A
117
Cleaning the cooling air ducts
Regularly clean the cooling air ducts through which the ambient air flows.
The frequency of the cleaning intervals depends on the local degree of fouling.
Damage to the machine when cleaning with compressed air or water jets
●
Do not direct compressed air or water jets in the direction of the shaft outlet or machine
openings.
●
Avoid direct impact of compressed air and water jets on sealing elements of the machine.
Note
Please note the safety instructions for cleaning.
9.2.10
Risk of explosion due to damaged seals
WARNING
Risk of explosion due to damaged seals
The seals can be damaged if you clean motors with type of protection Ex t using
compressed air. The type of protection is no longer complied with. An explosion can occur.
This may result in death, personal injury and material damage.
•
Avoid pointing compressed air directly onto shaft sealing rings or labyrinth seals of the
machine.
9.2.11
Drain condensate
If there are condensation drain holes present, open these at regular intervals, depending on
climatic conditions.
WARNING
Hazardous voltage
The winding can be damaged if objects are introduced into the condensation holes
(optional). This can lead to death, serious injury or material damage.
Note the following to maintain the degree of protection:
•
Switch off the machine so that it is in a no-voltage condition before you open the
condensation drain holes.
•
Close the condensation drain holes, e.g. using T-plugs, before commissioning the
machine.