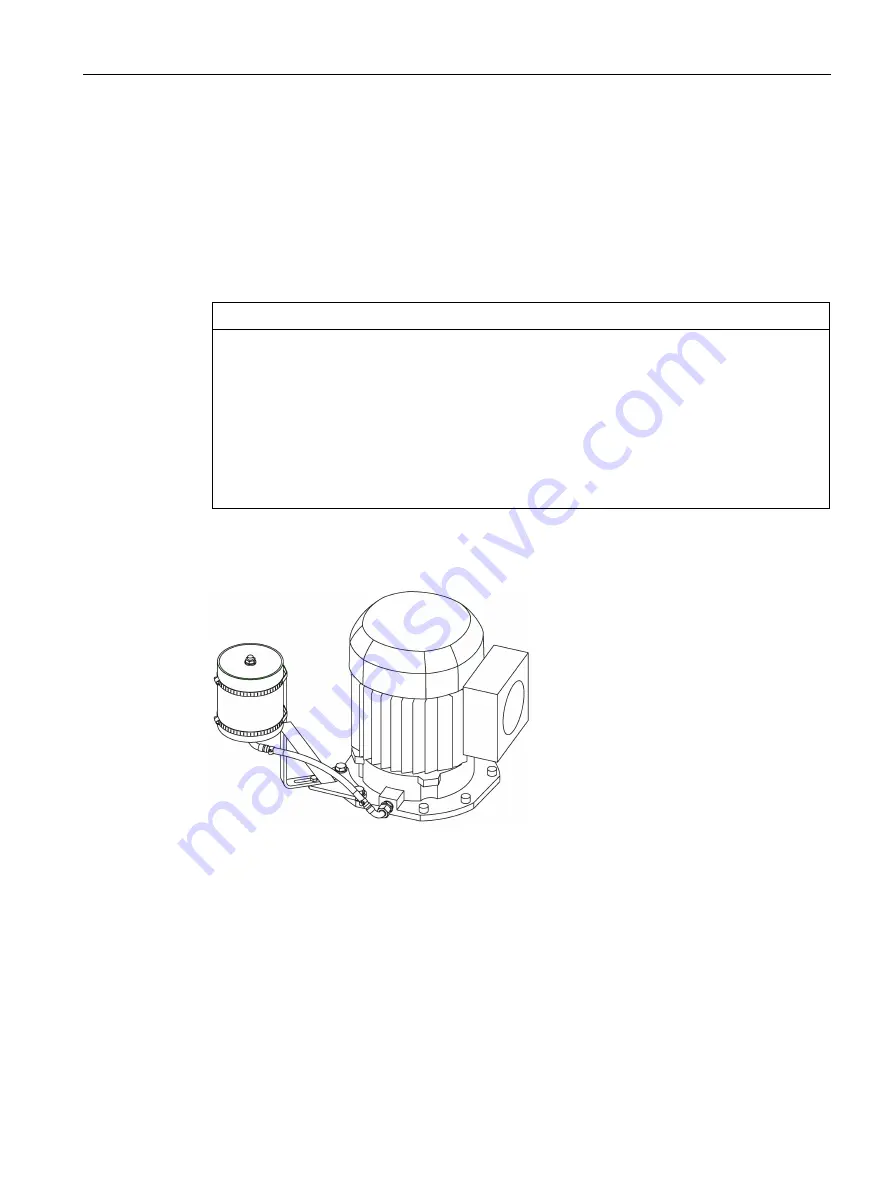
Commissioning
5.3 Mount the oil expansion unit
BA 2030 (2KJ4)
Operating Instructions, 07/2020, A5E50009094A/RS-AL
49
Procedure
1.
Assemble the mounting kit
①
-
⑤
.
2.
Screw on the unit with the screwed connection
⑤
at the uppermost drill hole of the gearbox
housing or of the motor bearing shield.
3.
Align the oil expansion unit so that it is vertical.
Oil expansion unit size 109 - 189
NOTICE
Hose with leaks
The hose of the oil expansion unit is subject to a natural aging process.
Check the hose for tears or leaks.
Never commission a leaky hose. Replace the hose, if necessary.
The hose of the oil expansion unit is not suitable for the ambient temperatures below -
25 °C.
If the ambient temperatures differ, contact Technical Support.
The unit is supplied as a mounting kit. The installation is described in the supplied Compact
Installation Instructions KA 2530-1.
Figure 5-3
Example of an oil expansion unit size 109-189
Summary of Contents for SIMOGEAR 2KJ40
Page 1: ......
Page 2: ......
Page 8: ...Table of contents BA 2030 2KJ4 6 Operating Instructions 07 2020 A5E50009094A RS AL ...
Page 58: ...Operation BA 2030 2KJ4 56 Operating Instructions 07 2020 A5E50009094A RS AL ...
Page 82: ...Disposal BA 2030 2KJ4 80 Operating Instructions 07 2020 A5E50009094A RS AL ...
Page 148: ......