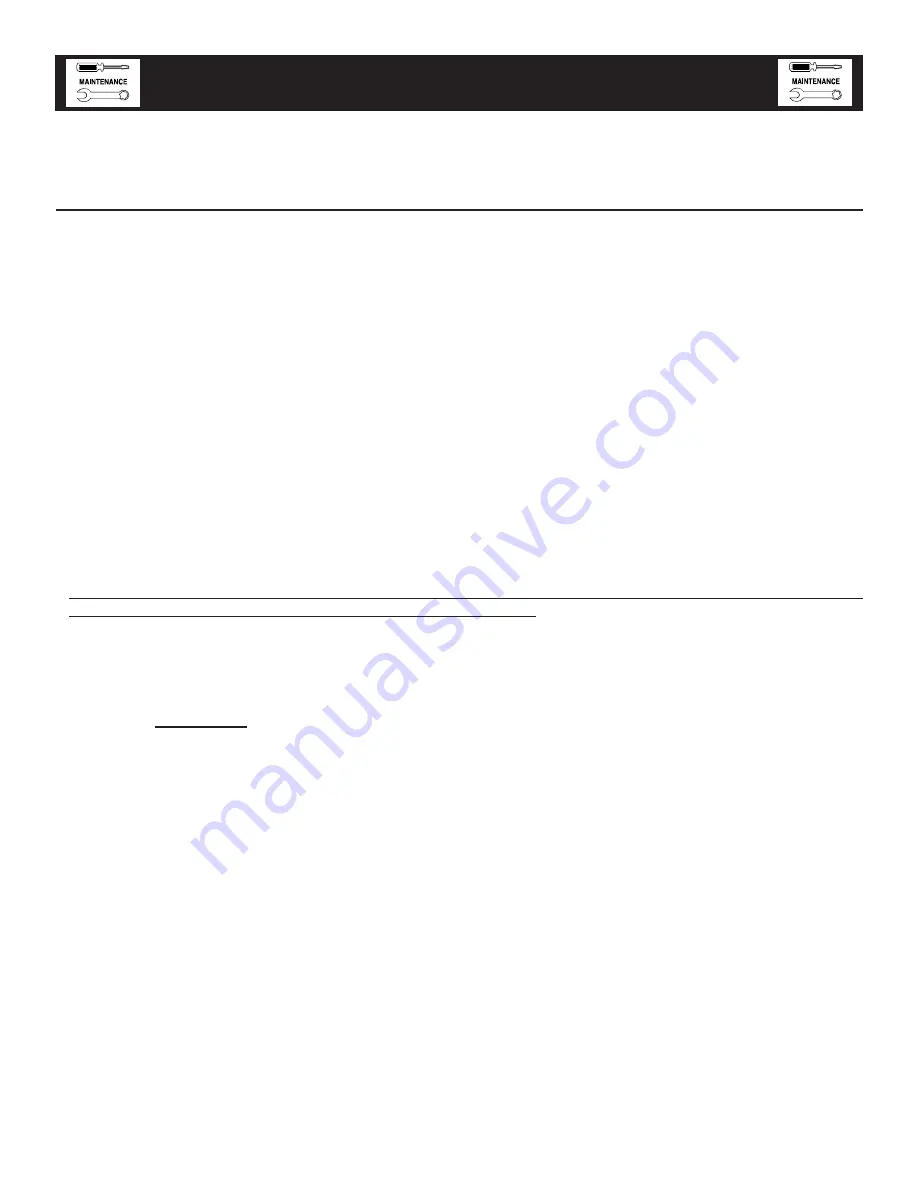
SERVICE SCHEDULE
30 KW - 150 KW STANDBY GAS ENGINE DRIVEN GENERATOR SETS
The following is a recommended maintenance schedule for standby gas engine driven generator sets from 30kW to
150 kW in size. The established intervals in the schedule are the maximum recommended when the unit is used
in an average service application. They will need to be decreased (performed more frequently) if the unit is used
in a severe application. Use calendar time, from the previous maintenance interval to determine the next required
maintenance interval.
Service Maintenance Interval Information:
The various service maintenance intervals are designated by interval numbers as follows:
1
An early inspection of the generator set to insure it is ready to operate when required and to identify any poten-
tial problem areas.
This inspection may be performed by the end user providing the following safety steps are taken to prevent
the engine from starting automatically without warning:
To prevent injury, perform the following steps in the order indicated before starting any maintenance:
•
Disable the generator set from starting and/or connecting to the load by setting the control panel Auto/Off/
Manual switch to the “OFF” position.
• Remove the 15 amp control panel fuse.
• Turn off the battery charger.
• Remove the negative battery cable.
The battery charger must be turned off BEFORE removing the battery cable to prevent an over current condition
from burning out sensitive control panel components and circuits.
Following all maintenance, reverse these steps to insure the unit is returned to standby setup for normal
operation when required.
2
A wear-in service inspection of the generator set to insure it is ready to operate and carry the load when
required, and to identify any potential problem areas.
Performed
ONLY ONCE
following the first three months or the first 30 hours of operation after purchase of
the unit.
This inspection contains some maintenance tasks which require special tools, equipment, and/or knowledge
to accomplish and should be performed only by an Authorized Service Dealer.
3
An operational inspection of the generator set to insure it is ready to operate and carry the load when required,
and to identify any potential problem areas.
Performed semi-annually or following each 50 hours of operation of the unit.
This inspection contains some maintenance tasks which require special tools, equipment, and/or knowledge
to accomplish and should be performed only by an Authorized Service Dealer.
4
A mid-level inspection of the generator set to insure it is ready to operate and carry the load when required,
and to identify any potential problem areas.
Performed annually or following each 100 hours of operation of the unit.
This inspection contains some maintenance tasks which require special tools, equipment, and/or knowledge
to accomplish and should be performed only by an Authorized Service Dealer.
5
A comprehensive inspection of the generator set to insure it is properly serviced and ready to operate and carry
the load when required, and to identify any potential problem areas.
Performed annually or following each 250 hours of operation of the unit.
This inspection contains some maintenance tasks which require special tools, equipment, and/or knowledge
to accomplish and should be performed only by an Authorized Service Dealer.
11-1
Standby Generator Sets
Service Schedule
SrvSchd001 Re
v. A 09/05
Summary of Contents for SG035 Series
Page 25: ...Standby Generator Sets Notes ...
Page 26: ...Standby Generator Sets Notes ...
Page 27: ...Standby Generator Sets Notes ...
Page 28: ......
Page 30: ......
Page 32: ......
Page 34: ......
Page 36: ......
Page 38: ......
Page 40: ......
Page 42: ......
Page 44: ......
Page 46: ......
Page 48: ......
Page 50: ......
Page 52: ......
Page 53: ......
Page 54: ......
Page 55: ......
Page 56: ......
Page 57: ......
Page 58: ......
Page 59: ......
Page 60: ......
Page 61: ......
Page 62: ......