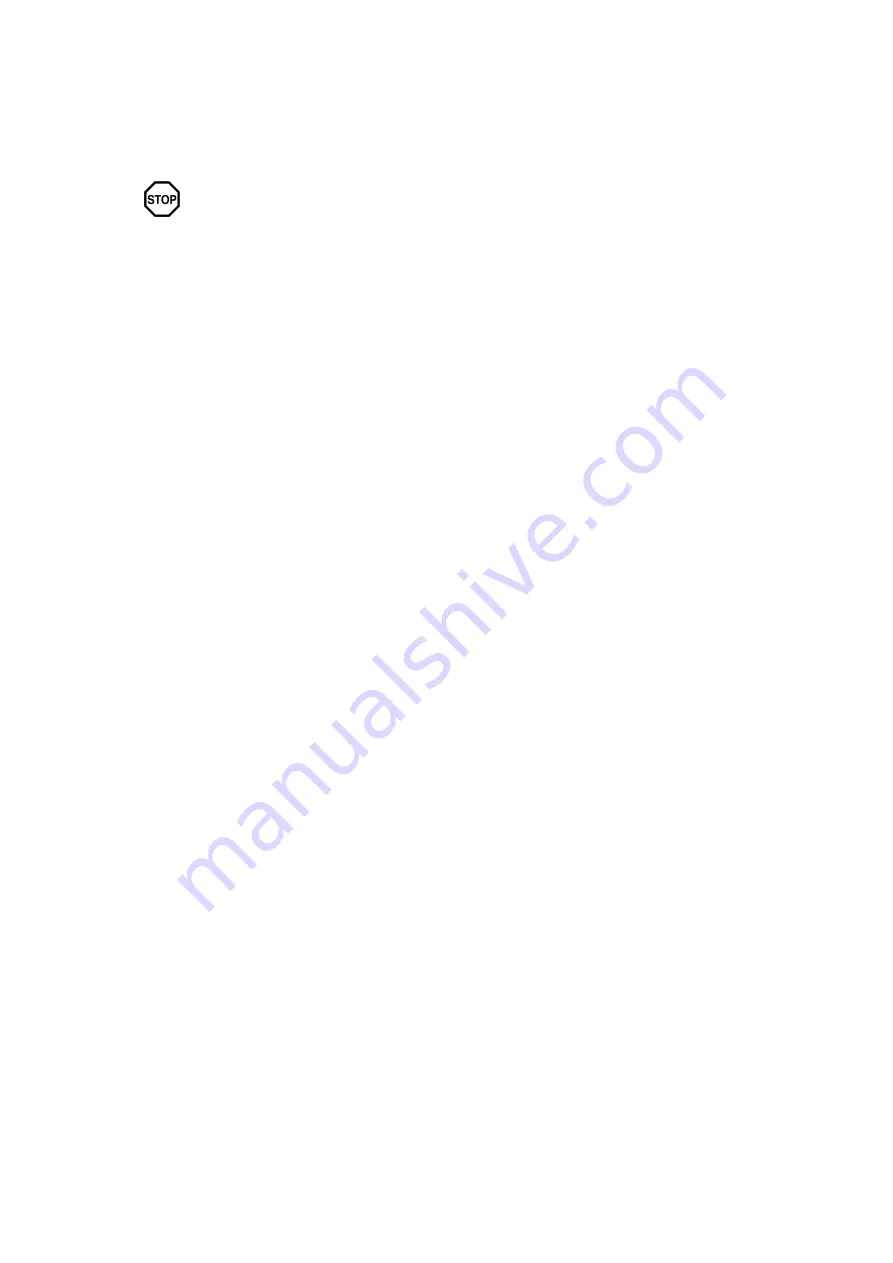
BA 5200 EN 08/2010
2.
General notes
2.1
Introduction
These instructions are an integral part of the gear unit supplied and must be kept in its vicinity for reference
at all times.
All persons carrying out work on the gear unit must have read and understood these
instructions and must adhere to them. Siemens accepts no responsibility for damage
or disruption caused by disregard of these instructions.
The
"FLENDER gear unit"
dealt with in these instructions has been developed for driving machines in
general engineering applications. Possible areas of use for gear units of this type are (e.g.) sewage
treatment, excavators, chemical industry, iron and steel industry, conveyor systems, crane systems,
foodstuffs industry, paper machinery, cableways, cement industry, etc.
The gear unit is designed only for the application specified in section 1, "Technical data". Other operating
conditions must be contractually agreed.
The gear unit has been manufactured in accordance with the state of the art and is delivered in a condition
for safe and reliable use.
The gear unit must be used and operated strictly in accordance with the conditions laid down in the contract
governing performance and supply agreed by Siemens and the customer.
The gear unit described in these instructions reflects the state of technical development at the time these
instructions went to print.
In the interest of technical progress we reserve the right to make changes to the individual assemblies and
accessories which we regard as necessary to preserve their essential characteristics and improve their
efficiency and safety.
2.2
Copyright
The copyright to these instructions is held by
Siemens AG
.
These instructions must not be wholly or partly reproduced for competitive purposes, used in any
unauthorised way or made available to third parties without our agreement.
Technical enquiries should be addressed to the following works or to one of our customer services:
Siemens AG
Südstraße 111
44625 Herne
Tel.:
+49 (0)2323 / 940-0
Fax:
+49 (0)2323 / 940-200
Service‐Hotline: 0172 / 2810100