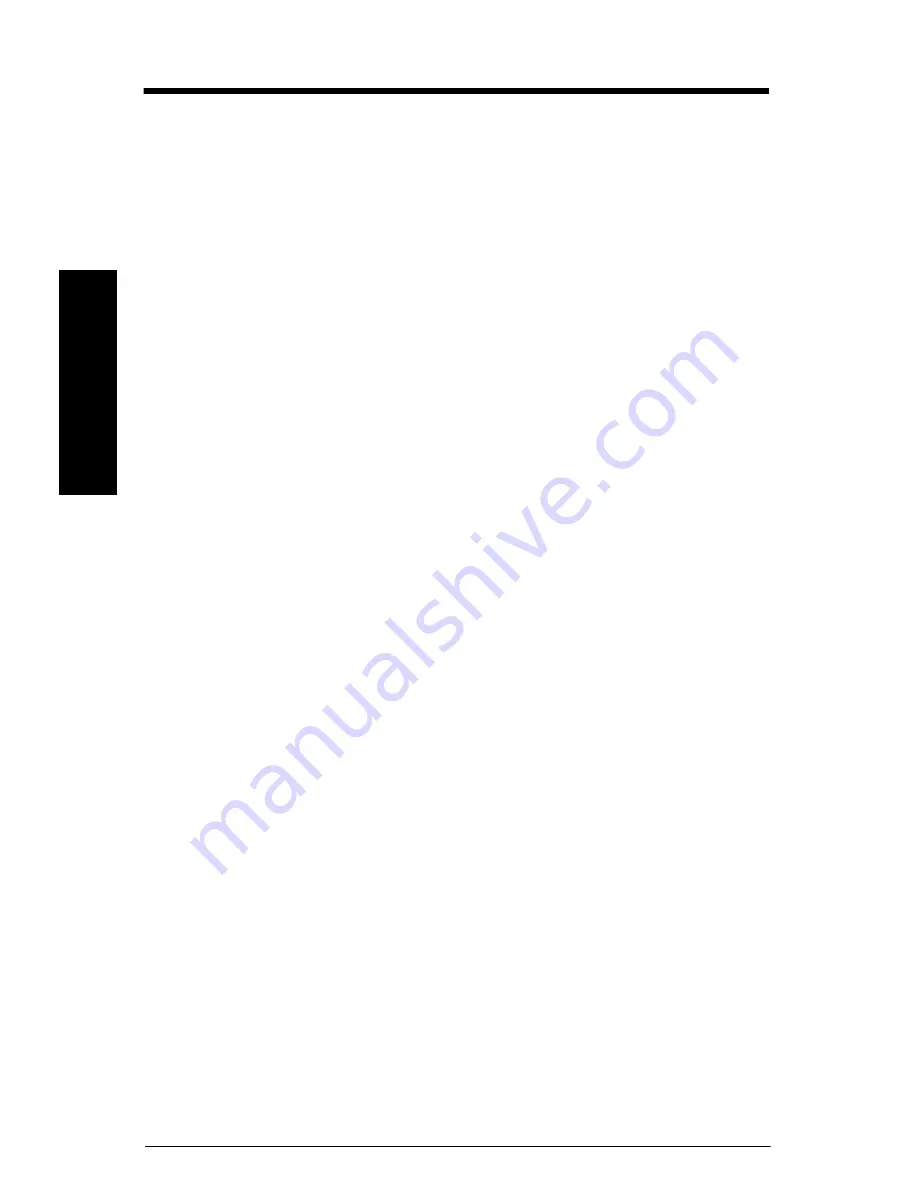
Page 4
SmartLinx PROFIBUS DP-V1 – Operating Instructions
A5E36197302
m
m
m
m
m
Sm
ar
tL
in
x
PR
O
FI
B
U
S
D
P-
V1
Specifications
Application
Compatible with the MultiRanger 200 HMI and the HydroRanger 200 HMI.
Communication settings
Baud rate: 9.6 Kbaud to 12 Mbaud, automatically detected.
Termination
Switch selectable, open or special active termination as per PROFIBUS specification (see
Termination switch on page 6).
Cable
Belden PROFIBUS cable 3079A, or equivalent.
Summary of Contents for PROFIBUS DP-V1
Page 1: ...Operating Instructions SmartLinx PROFIBUS DP V1 08 2015 Edition Communication ...
Page 4: ...ii mmmmm Table of Contents ...
Page 30: ......
Page 31: ......